1 thermal motor model – Watson-Marlow MM440 User Manual
Page 229
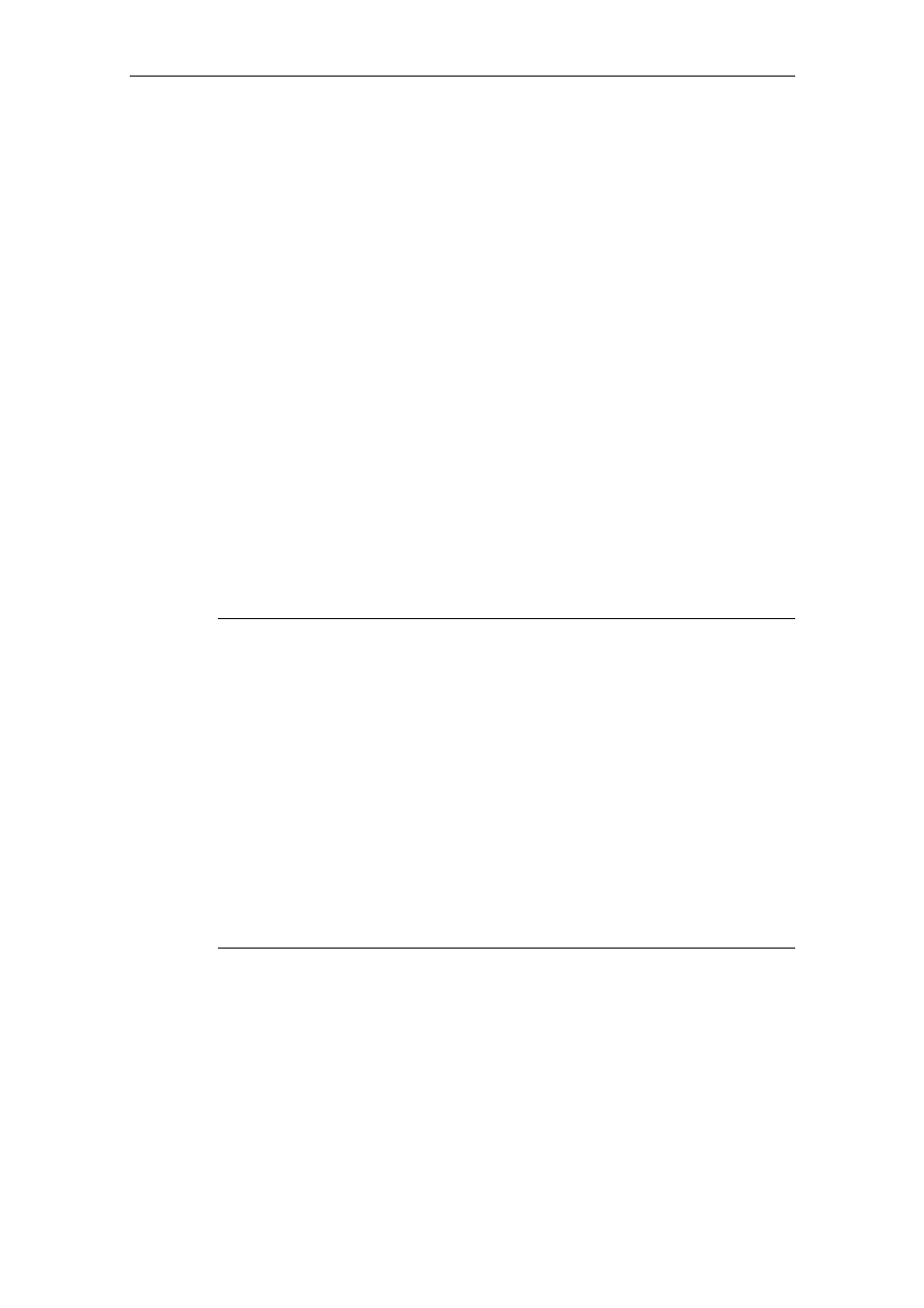
Issue 10/06
3 Functions
MICROMASTER 440 Operating Instructions
6SE6400-5AW00-0BP0
229
3.21.1
Thermal motor model
The data, required for the thermal motor model, is estimated from the rating plate
data entered during the quick commissioning (refer to Section 3.5.3). This data
permits reliable, stable operation for standard Siemens motors. If required,
parameter changes must be made for motors from third-party manufacturers. We
always recommend that an automatic motor data identification run is made after
quick commissioning so that the electrical equivalent circuit diagram data can be
determined. This allows a more precise calculation of the losses which occur in the
motor which has a positive impact on the accuracy of the thermal motor model.
Example:
A stator resistance, which is parameterized to be too high, would result, in the
model, to higher losses than in a real motor and an excessively high calculated
motor temperature would be displayed.
If changes are required in order to optimize the thermal model, then as a first step,
the motor weight (P0344) should be checked for plausibility. Generally, the motor
weight is taken from the Catalog data of the motor manufacturer. The thermal
model can be further optimized by adapting the standard overtemperatures for the
stator iron P0626, the stator winding P0627 and the rotor P0628. The standard
overtemperatures represent the steady-state temperatures to be expected in rated
operation with respect to the environment and are used to estimate the thermal
resistances. Generally, these overtemperatures are not listed in the Catalog.
The ambient temperature P0625 is another important parameter which influences
the precision of the thermal model.
NOTE
¾
In addition to the thermal motor protection, the motor temperature is also
included in the adaptation of the motor equivalent circuit diagram data. This
adaptation has a significant influence on the degree of stability of the closed-
loop vector control – especially for a high thermal motor load.
¾
When switching-in the line supply voltage (i.e. powering-up), depending on
whether a KTY sensor is being used or not, the motor temperature model is
either initialized with the ambient temperature P0625 – saved in the frequency
inverter – or with the actual motor temperature.
¾
If the frequency inverter is continually supplied with an external 24 V voltage,
then the motor temperature is tracked/corrected using the motor temperature
time constant – even when the line supply voltage is shutdown (powered-down).
¾
For closed-loop vector control, a high thermal motor load and if the line supply
voltage is frequently switched-out/switched-in, then the following is required
♦ a KTY84 sensor should be used, or
♦ an external 24 V power supply should be connected