Watson-Marlow MM440 User Manual
Page 262
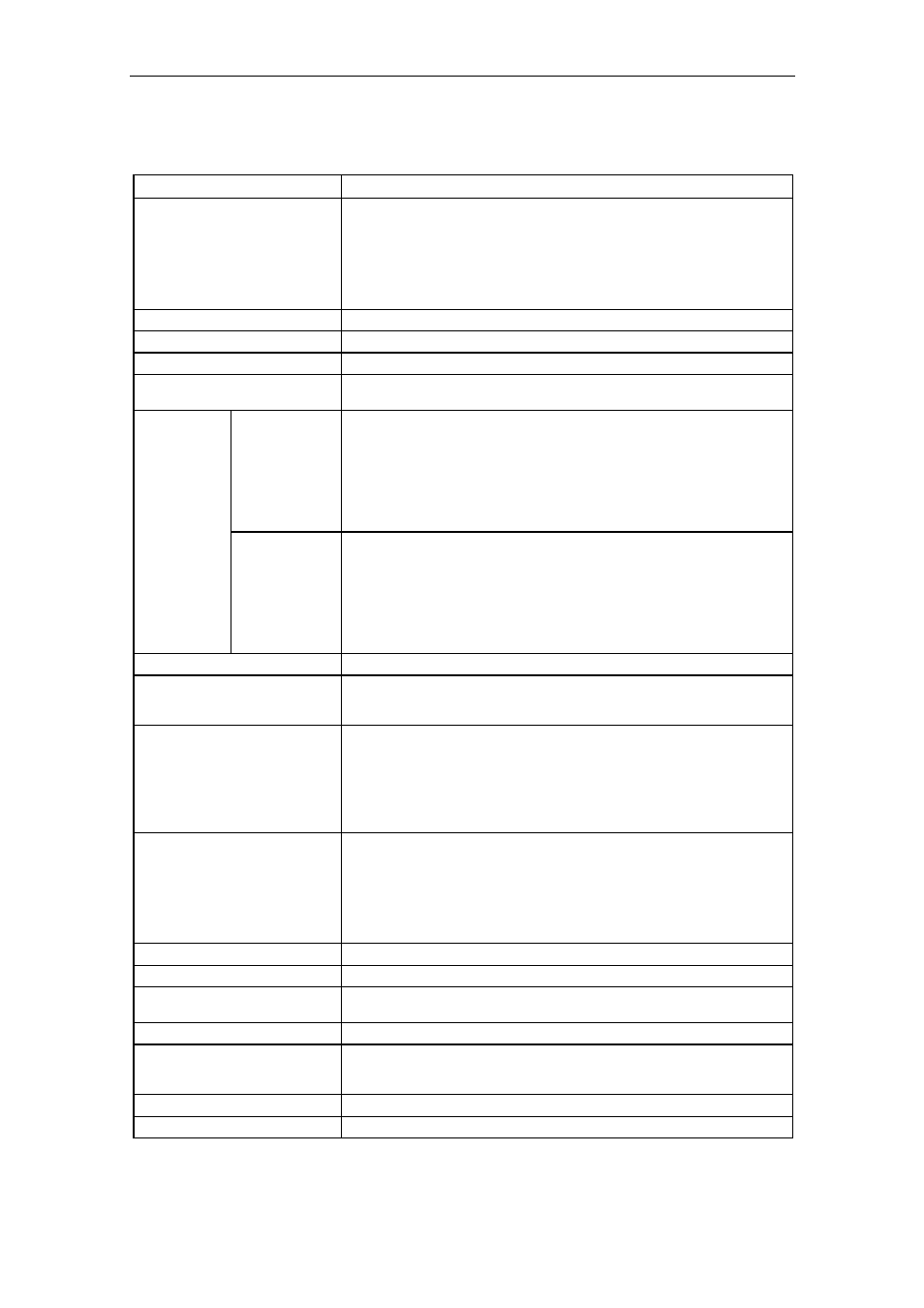
5 MICROMASTER 440 specifications
Issue 10/06
MICROMASTER 440 Operating Instructions
262
6SE6400-5AW00-0BP0
Table 5-1
MICROMASTER 440 Performance Ratings
Feature Specification
Mains Operating Voltage
& Power Ranges
1 AC 200 to 240 V
± 10 %
CT: 0,12 kW – 3,0 kW
(0,16 hp – 4,0 hp)
3 AC 200 to 240 V
± 10 %
CT: 0,12 kW – 45,0 kW
(0,16 hp – 60,0 hp)
VT: 5,50 kW – 45,0 kW
(7,50 hp – 60,0 hp)
3 AC 380 to 480 V
± 10 %
CT: 0,37 kW – 200 kW
(0,50 hp – 268 hp)
VT: 7,50 kW – 250 kW
(10,0 hp – 335 hp)
3 AC 500 to 600 V
± 10 %
CT: 0,75 kW – 75,0 kW
(1,00 hp – 100 hp)
VT: 1,50 kW – 90,0 kW
(2,00 hp – 120 hp)
Input Frequency
47 to 63 Hz
Output frequency
0 Hz to 650 Hz
Power Factor
0.95
Inverter Efficiency
Frame Sizes A to F:
96 % to 97 %
Frame Sizes FX and GX: 97 % to 98 %
Constant Torque
(CT)
Frame Sizes A to F:
1.5 x Nominal output current (i.e. 150 % overload)
for 60 s every 300 s and
2 x Nominal output current (i.e 200 % overload) for
3 s every 300 s
Frame Sizes FX and GX: 1.36 x Nominal output current (i.e 136 % overload)
for 57 s every 300 s and
1.6 x Nominal output current (i.e 160 % overload) for
3 s every 300 s
Overload
Capability
Variable Torque
(VT)
Frame Sizes A to F:
1.1 x Nominal output current (i.e. 110 % overload)
for 60 s every 300 s and
1.4 x Nominal output current (i.e 140 % overload) for
3 s every 300 s
Frame Sizes FX and GX: 1.1 x Nominal output current (i.e. 110% overload) for
59 s every 300 s and
1.5 x Nominal output current (i.e 150% overload) for
1 s every 300s
Inrush Current
Less than rated input current
Power-ON-OFF cycle time
Frame Sizes A to E:
every 30 s
Frame Size F:
every 150 s
Frame Sizes FX and GX: every 300 s
Control Method
V/f control, output frequency between 0 Hz and 650 Hz:
Linear V/f control, Linear V/f control with FCC, Parabolic V/f control, Multi-point
V/f control, V/f control for textile applications, V/f control with FCC for textile
applications, V/f control with independent voltage setpoint,
Vector control, output frequency between 0 Hz and 200 Hz:
Sensorless Vector Control, Sensorless Vector Torque Control, Speed control
with Encoder Feedback, Torque control with Encoder Feedback
Pulse Frequency
Frame Sizes A to C:
1/3AC 200 V to 5,5 kW (Standard 16 kHz)
Frame Sizes A to F:
other powers and voltages
2 kHz to 16 kHz (2 kHz steps) (Standard 4 kHz)
power reduction see Table 5-3
Frame Sizes FX and GX: 2 kHz to 4 kHz (2 kHz steps)
(Standard 2 kHz (VT), 4 kHz (CT))
power reduction see Table 5-3
Fixed Frequencies
15, programmable
Skip Frequencies
4, programmable
Setpoint Resolution
0.01 Hz Digital, 0.01 Hz Serial, 10 bit Analogue
(motor potentiometer 0.1 Hz [0.1% (in PID mode)
Digital Inputs
6, programmable (isolated), switchable active high / active low (PNP/NPN)
Analog Inputs
2, programmable, both are parameterizable as 7th and 8th digital inputs
0 V to 10 V, 0 mA to 20 mA and –10 V to +10 V (ADC1)
0 V to 10 V and 0 mA to 20 mA (ADC2)
Relay Outputs
3, programmable 30 V DC / 5 A (resistive), 250 V AC 2 A (inductive)
Analogue Output
2, programmable (0 to 20 mA)