Yaskawa Sigma-5 User Manual: Design and Maintenance - Linear Motors MECHATROLINK-III Communications Reference User Manual
Page 288
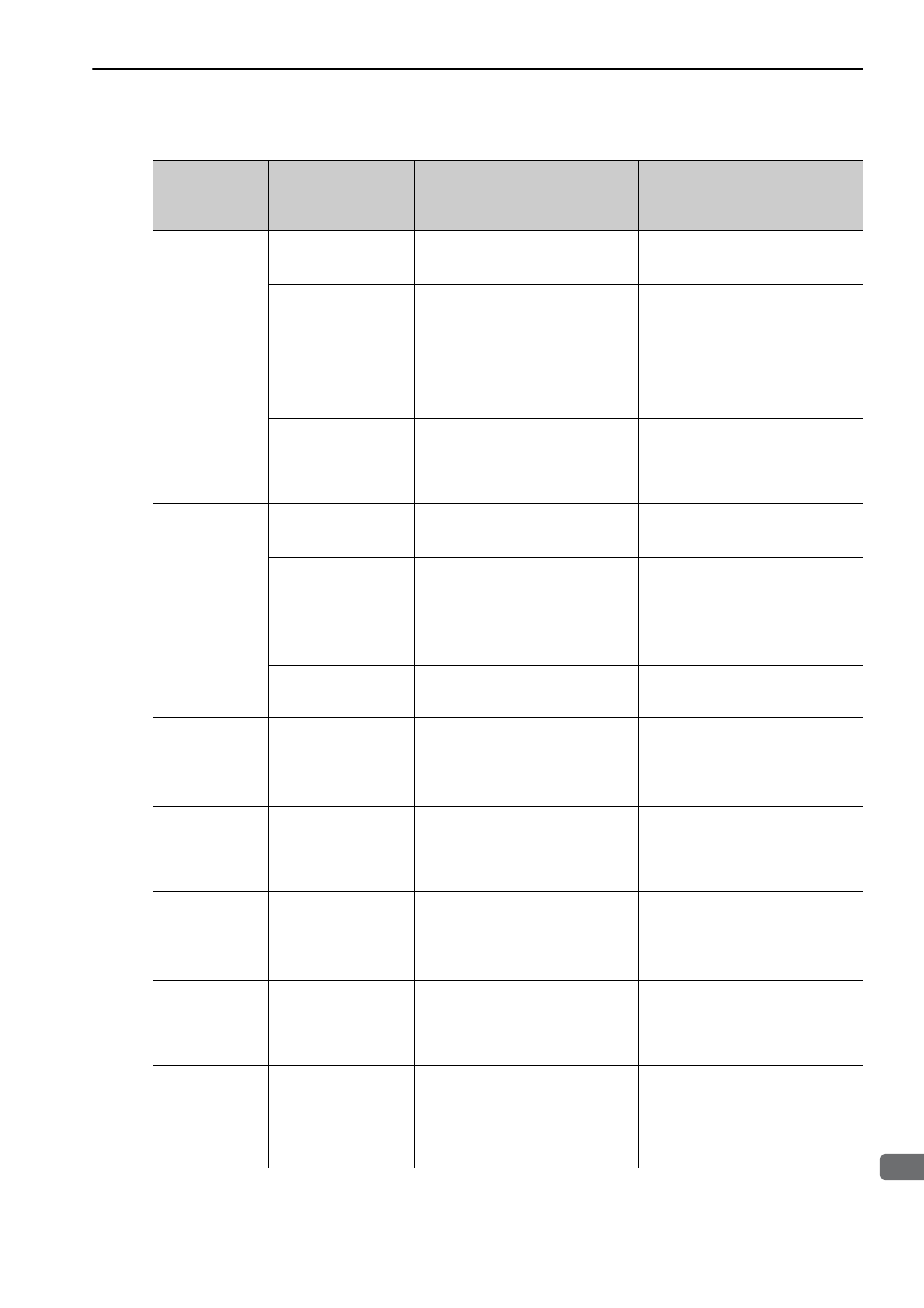
8.2 Warning Displays
8-27
8
Trou
blesh
ooting
A.920:
Regenerative
Overload
(Warning before
the alarm A.320
occurs)
The power supply volt-
age exceeds the speci-
fied limit.
Measure the power supply voltage.
Set the power supply voltage within
the specified range.
Insufficient external
regenerative resistance,
regenerative resistor
capacity, or SERVO-
PACK capacity.
Or, regenerative power
has been continuously
flowing back.
Check the operating condition or the
capacity using the capacity selection
Software SigmaJunmaSize+, etc.
Change the regenerative resistance,
regenerative resistor capacity, or SER-
VOPACK capacity. Reconsider the
operating conditions using the capac-
ity selection software SigmaJunma-
Size+, etc.
Regenerative power
continuously flowed
back because negative
load was continuously
applied.
Check the load to the servomotor dur-
ing operation.
Reconsider the system including servo
drives, machine, and operating condi-
tions.
A.921:
Dynamic Brake
Overload
(Warning before
the alarm A.731
occurs)
The servomotor moves
because of external
force.
Check the operation status.
Take measures to ensure the servomo-
tor will not move because of external
force.
The moving energy at a
DB stop exceeds the DB
resistance capacity.
Check the power consumed by DB
resistance (Un00B) to see how many
times the DB has been used.
Reconsider the following:
• Reduce the motor reference speed.
• Reduce the mass ratio.
• Reduce the number of times of the
DB stop operation.
A SERVOPACK fault
occurred.
−
The SERVOPACK may be faulty.
Replace the SERVOPACK.
A.94A
Data Setting
Warning 1
(Parameter Num-
ber Error)
Disabled parameter
number was used.
Refer to 8.3 Monitoring Communica-
tion Data on Occurrence of an Alarm
or Warning to determine which
command was the cause of the
warning.
Use the correct parameter number.
A.94B
Data Setting
Warning 2
(Out of Range)
Attempted to send val-
ues outside the range to
the command data.
Refer to 8.3 Monitoring Communica-
tion Data on Occurrence of an Alarm
or Warning to determine which
command was the cause of the
warning.
Set the value of the parameter within
the allowable range.
A.94C
Data Setting
Warning 3
(Calculation Er-
ror)
Calculation result of set
value is incorrect.
Refer to 8.3 Monitoring Communica-
tion Data on Occurrence of an Alarm
or Warning to determine which
command was the cause of the
warning.
Set the value of the parameter within
the allowable range.
A.94D
Data Setting
Warning 4
(Parameter Size)
Parameter size set in
command is incorrect.
Refer to 8.3 Monitoring Communica-
tion Data on Occurrence of an Alarm
or Warning to determine which
command was the cause of the
warning.
Use the correct parameter size.
A.94E
Data Setting
Warning 5
(Latch mode
error)
Latch mode error is
detected.
Refer to 8.3 Monitoring Communica-
tion Data on Occurrence of an Alarm
or Warning to determine which
command was the cause of the
warning.
Change the setting value of Pn850 or
the LT_MOD data for the
LTMOD_ON command sent by the
host controller to the proper value.
(When using the MECHATROLINK-
II-compatible profile.)
(cont’d)
Warning Num-
ber: Warning
Name (Warning
Description)
Cause
Investigative Actions
Corrective Actions