Engaging/disengaging, Running – Yaskawa MotionWorks+ Windows Software User Manual
Page 198
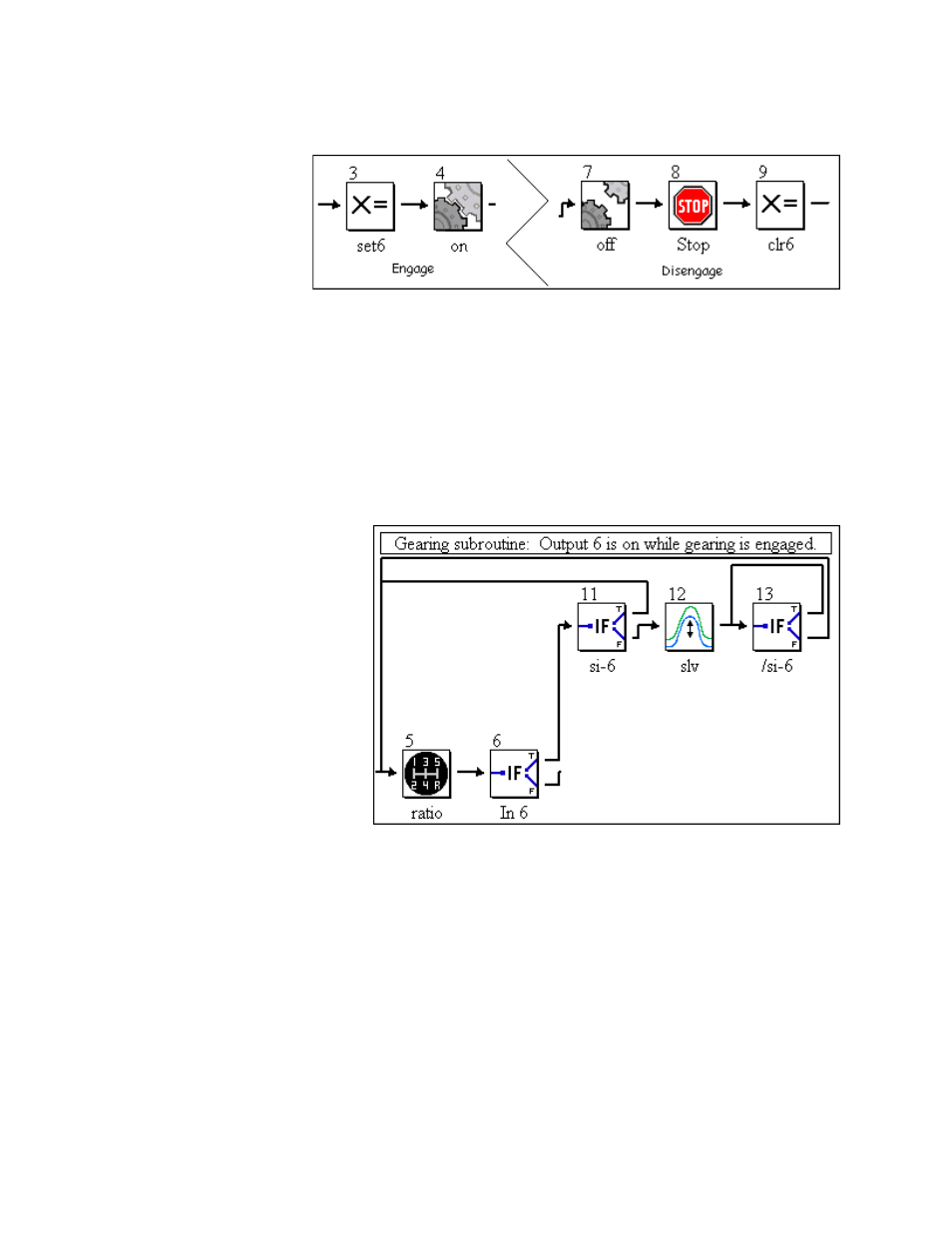
Standardized Template Project
MotionWorks+™
192
Engaging/Disengaging
Blocks 3 – 4 & 7
– 9 comprise
engaging and
disengaging of
gearing. Blocks
3 and 9 take care
of activating /
deactivating Output 6 while entering / leaving the gearing subroutine. The key element to
remember is to include a STOP block. If the STOP block is not included and the slave is
disengaged while the master is motion, the slave will continue to rotate at the last known
calculated speed of the master axis. Additionally, the STOP block will switch the axis to
position mode, providing a controlled deceleration to zero speed and will maintain posi-
tion once stopped.
Running
The rest of the blocks
are executed while the
system is engaged in
gearing (or running).
The user is able to adjust
the gearing ratio by
modifying the variables
(user variables [Gear-
Master] divided by
[GearSlave]) in the Gear
Ratio block (5). The
gear ratio is a fraction of
two integer numbers. Be
careful not to use float-
ing-point variables for
these. Doing so will truncate the values, resulting in lost motion. In addition, shifting of
the Slave position is possible by activating input SI-6. The amount of offset is relative (in
user units, based on the user variable [GearSlaveOffsetPosition]) to the current position of
the respective axis. The offset can be accomplished over a given amount of time or dis-
tance (in user units, based on user variable [GearSlaveOffsetDuration]). System variable
sSlaveOffset_Mode determines if the duration is time or position based.
(sSlaveOffset_Mode = 0, time based offset; sSlaveOffset_Mode = 1, master position
based offset)