Yaskawa YASNAC PC NC Maintenance Manual User Manual
Page 179
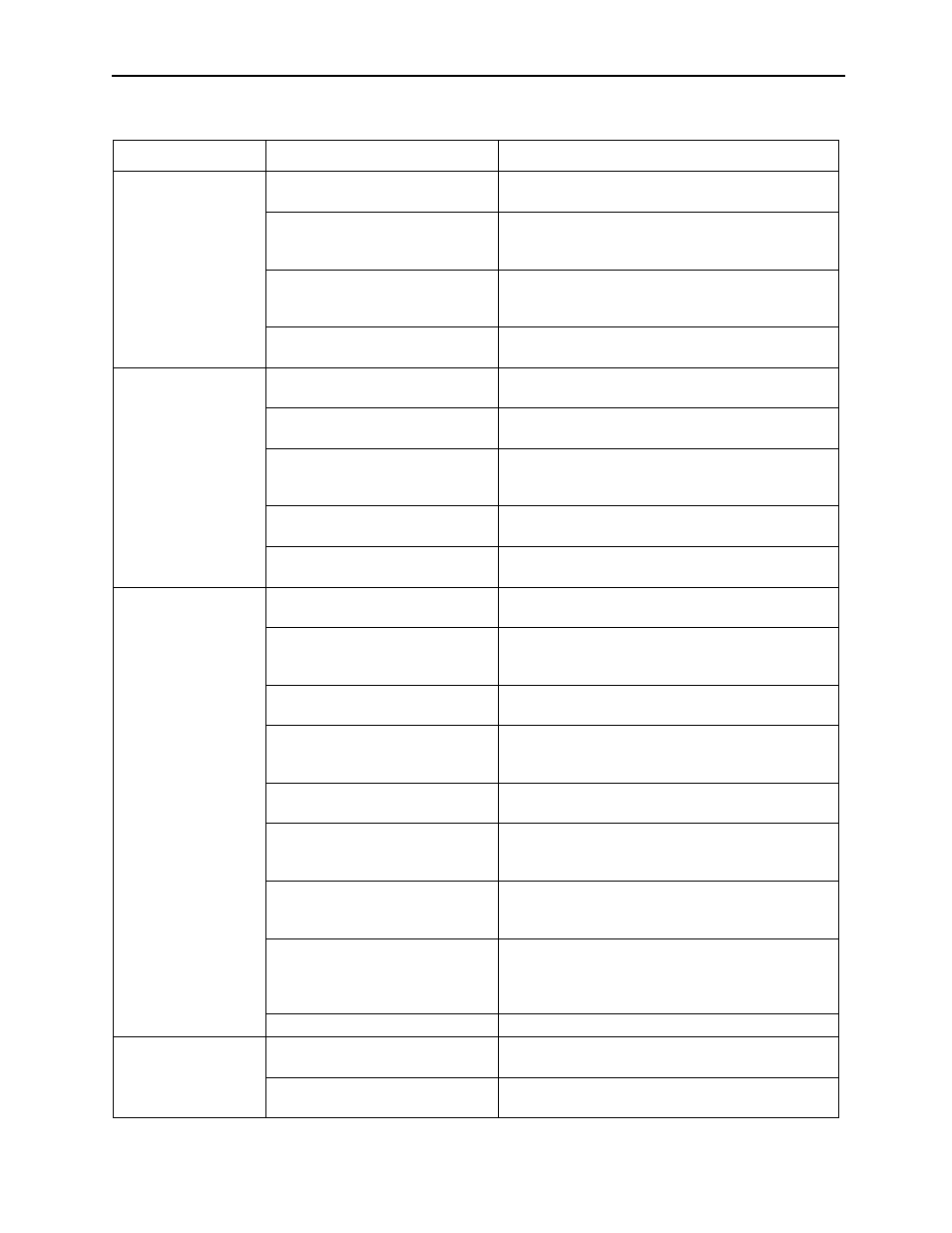
PC NC Maintenance Manual
The VS-626M5
4-158
Motor does not stop at
orientation.
(encoder method ori-
entation)
Orientation signal ORT is not input.
Check that orientation signal ORT is closed on opera-
tion status display (U1-09).
Encoder signal line disconnection,
improper connection, loose connec-
tor
Check the wiring of encoder signal lines.
Encoder fault
Check for abnormal changes in motor speed on the
speedometer or operation status display (U1-01).
Replace the encoder or the motor.
Fault of orientation card or control
PC board
Replace the orientation card or the control PC board.
Motor does not stop at
orientation. (magnetic
sensor method orienta-
tion)
Orientation signal ORT is not input.
Check that orientation signal ORT is closed on opera-
tion status display (U1-09).
Incorrect transmission ratio setting
Verify the machine data for transmission ratio values
(C1-27 to 29).
Magnetic sensor signal line discon-
nection, improper connection, loose
connector
Check the wiring of magnetic sensor signal lines.
Fault of magnetic sensor or magne-
tizer
Rotate the load shaft and verify that ORG signal lights
once per rotation on operation status display (U1-10).
Fault of orientation card or control
PC board
Replace the orientation card or the control PC board.
Stop position differs
from commanded posi-
tion. (encoder method
orientation)
Incorrect setting of stop position ref-
erence
Check whether the position reference is correct on
operation status display (U2-04).
Incorrect selection of binary/BCD
reference or incorrect setting of
BCD reference resolution
Check the setting of control constants C2-22 bit 3 and
C2-12.
Incorrect selection of reference
point at incremental positioning
Check the setting of control constant C2-22 bit 5.
Improper setting of load shaft zero-
point position
Perform positioning at zero-point to measure position
accuracy.
Perform tune-up again to set the load shaft zero-point.
Incorrect selection of reference
point at incremental positioning
Check the setting of control constant C2-22 bit 5.
Improper setting of load shaft zero-
point •/“à•¶24
position
Perform positioning at zero-point to measure position
accuracy.
Perform tune-up again to set the load shaft zero-point.
Encoder signal line disconnection,
improper connection, loose connec-
tor
Check the wiring of encoder signal lines.
Malfunction due to noise (Poor
encoder characteristics)
Check that encoder signal lines are separated from
inverter output wiring or other power lines.
Check encoder cable specifications (whether the
cable is a twisted pair shielded wire).
Control PC board fault
Replace the control PC board.
Stop position differs
from commanded posi-
tion. (magnetic sensor
method orientation)
Magnetic sensor signal line discon-
nection, loose connector
Check the wiring of magnetic sensor signal lines.
Fault of orientation card or control
PC board
Replace the orientation card or the control PC board.
Table 4.38: Motor Faults and Corrective Actions (Continued)
Fault
Cause
Corrective Action