Yaskawa Sigma Mini User Manual
Page 141
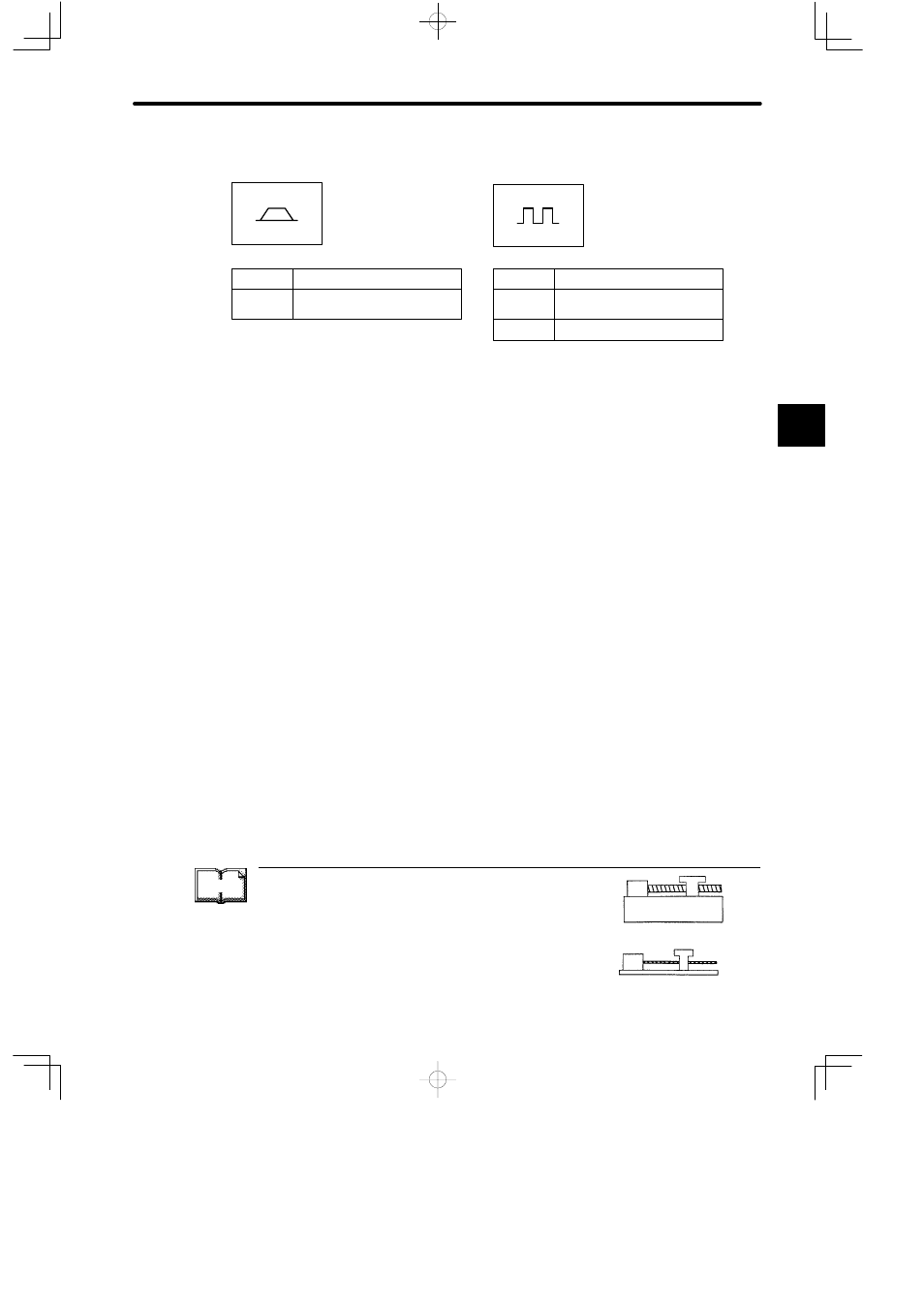
3.2Applications
— 3-17 —
Automatically Settable Parameters
Speed/Torque
Positions
Speed/torque control
Position control
Cn-04
Speed loop gain
Speed loop integration time
constant
Position loop gain
Cn-05
Cn-1A
Cn-04
Speed loop gain
Speed loop integration time
constant
Cn-05
Once autotuning has been completed, the autotuning procedure can be omitted for sub-
sequent machines, providing the machine specifications remain unchanged.
It is sufficient to directly set the parameters for subsequent machines.
The machine rigidity can be selected from one of seven levels.
Note
(1) Conduct autotuning with the motor attached to the machine.
Make sure that the machine is ready for operation and take sufficient safety precau-
tions when operating the machine.
(2) Make sure that the /P-CON signal is OFF (PI control is selected) before starting auto-
tuning.
(3) Make sure that the speed control mode is set to PI control before starting autotuning.
If the mode switch is used, PI control automatically switches to P control above a set
operating level (PI control to P control switching level), even if the /P-CON signal is
OFF.
If the mode switch is used, perform one of the following operations before starting auto-
tuning.
• Set the parameters to disable the mode switch.
Speed control: Set both Cn-01 bit C and bit D to 1.
Position control: Set both Cn-01 bit B to 1.
• Increase the operating level (PI control to P control switching level), so that P control is
not selected.
In practice, set the operating level as shown in the following table.
Select the operating level using bit C and bit D of Cn-01.
TERMS
Machine Rigidity
The machine rigidity is one of the machine charac-
teristics related to servo control. Set the servo to
high response for a machine with high rigidity, such
as a machine tool, and to low response for a ma-
chine with low rigidity, such as a robot.
High rigidity
Motor
Low rigidity
Motor
3