2 advanced autotuning procedure, Caution, 1) operating procedure – Yaskawa Sigma-5 User Manual: Design and Maintenance - Linear Motors User Manual
Page 163
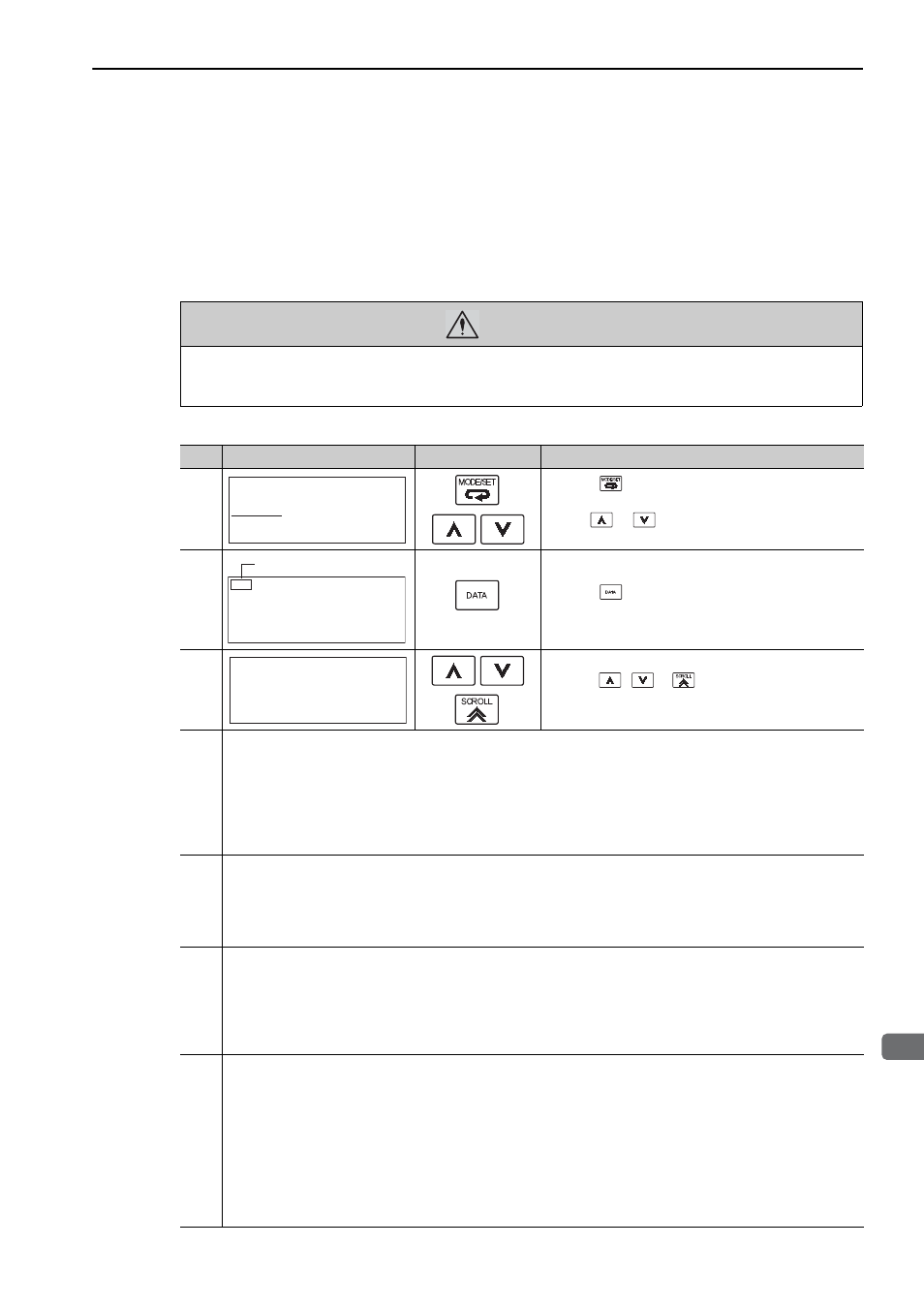
5.3 Advanced Autotuning (Fn201)
5-19
5
Adjustments
5.3.2 Advanced Autotuning Procedure
The following procedure is used for advanced autotuning.
Advanced autotuning is performed from the Digital Operator (option) or SigmaWin+.
The operating procedure from the Digital Operator is described here.
For the basic operations of the Digital Operator, refer to the
Σ
-V series User’s Manual, Operation of Digital
Operator (SIEP S800000 55).
(1) Operating Procedure
CAUTION
• When using the SERVOPACK with Jcalc = OFF (mass is not calculated), be sure to set a suitable value for
the mass ratio (Pn103). If the setting greatly differs from the actual mass ratio, normal control of the SER-
VOPACK may not be possible, and vibration may result.
Step
Display after Operation
Keys
Operation
1
Press the
Key to view the main menu for the utility
function mode.
Use the
or
Key to move through the list, select
Fn201.
2
Press the
Key to display the initial setting screen
for advanced autotuning.
3
Press the
,
or
Key and set the items in
steps 3-1 to 3-4.
3-1
Calculating Mass
Select the mode to be used.
Usually, set Jcalc to ON.
Jcalc = ON: Calculates the mass. [Factory setting]
Jcalc = OFF: Does not calculate the mass.
Note:
If the mass is already known from the machine specifications, set the value in Pn103 and set Jcalc to OFF.
3-2
Mode Selection
Select the mode.
Mode = 1: Makes adjustments considering responsiveness and stability. (Standard level)
Mode = 2: Makes adjustments for positioning. [Factory setting]
Mode = 3: Makes adjustments for positioning, giving priority to overshooting suppression.
3-3
Type Selection
Select the type according to the machine element to be driven. If there is noise or the gain does not increase, better
results may be obtained by changing rigid type.
Type = 1: For belt drive mechanisms.
Type = 2: For ball screw drive mechanisms [Factory setting].
Type = 3: For rigid systems, such as a gear.
3-4
STROKE (Travel Distance) Setting
Travel distance setting range:
The travel distance setting range is from -99990000 to +99990000. Specify the STROKE (travel distance)
in increments of 1000 reference units. The negative (-) direction is for reverse movement, and the positive
(+) direction is for forward movement.
Initial value: 90 mm
Notes:
• Set the travel distance of the linear servomotor to at least 5 mm; otherwise, “Error” will be displayed and the
advanced autotuning cannot be performed.
• To calculate the mass ratio and ensure precise tuning, it is recommended to set the travel distance to 90 mm.
㧮㧮 ޓ̆㧲㨁㧺㧯㨀㧵㧻㧺̆
㧲㨚㧞㧜㧜㧦㨀㨡㨚㨑㧸㨢㨘ޓ㧿㨑㨠
㧲㨚㧞㧜㧝㧦㧭㧭㨀
㧲㨚㧞㧜㧞㧦㧾㨑㨒㧭㧭㨀
㧲㨚㧞㧜㧟㧦㧻㨚㨑㧼㨞㨙㨀㨡㨚
㧮㧮 㧭㨐㨢㨍㨚㨏㨑㨐ޓ㧭㨀
ޓ㧶㨏㨍㨘㨏㧩㧻㧺
ޓ㧹 㨛 㨐 㨑㧩㧞ޓ㨀㨥㨜㨑㧩㧞
ޓ㧿㨠㨞㨛㨗㨑㧩㧗㧜㧜㧤㧜㧜㧜㧜㧜
ޓޓޓޓޓޓ㧔㧜㧜㧜㧟㧚㧜㧕㨞㨑㨢
Status Display
㧮㧮 㧭㨐㨢㨍㨚㨏㨑㨐ޓ㧭㨀
ޓ㧶㨏㨍㨘㨏㧩㧻㧺
ޓ㧹 㨛 㨐 㨑㧩㧞ޓ㨀㨥㨜㨑㧩㧞
ޓ㧿㨠㨞㨛㨗㨑㧩㧗㧜㧜㧤㧜㧜㧜㧜㧜
ޓޓޓޓޓޓ㧔㧜㧜㧜㧟㧚㧜㧕㨞㨑㨢