Yaskawa Sigma-5 User Manual: Design and Maintenance - Linear Motors User Manual
Page 262
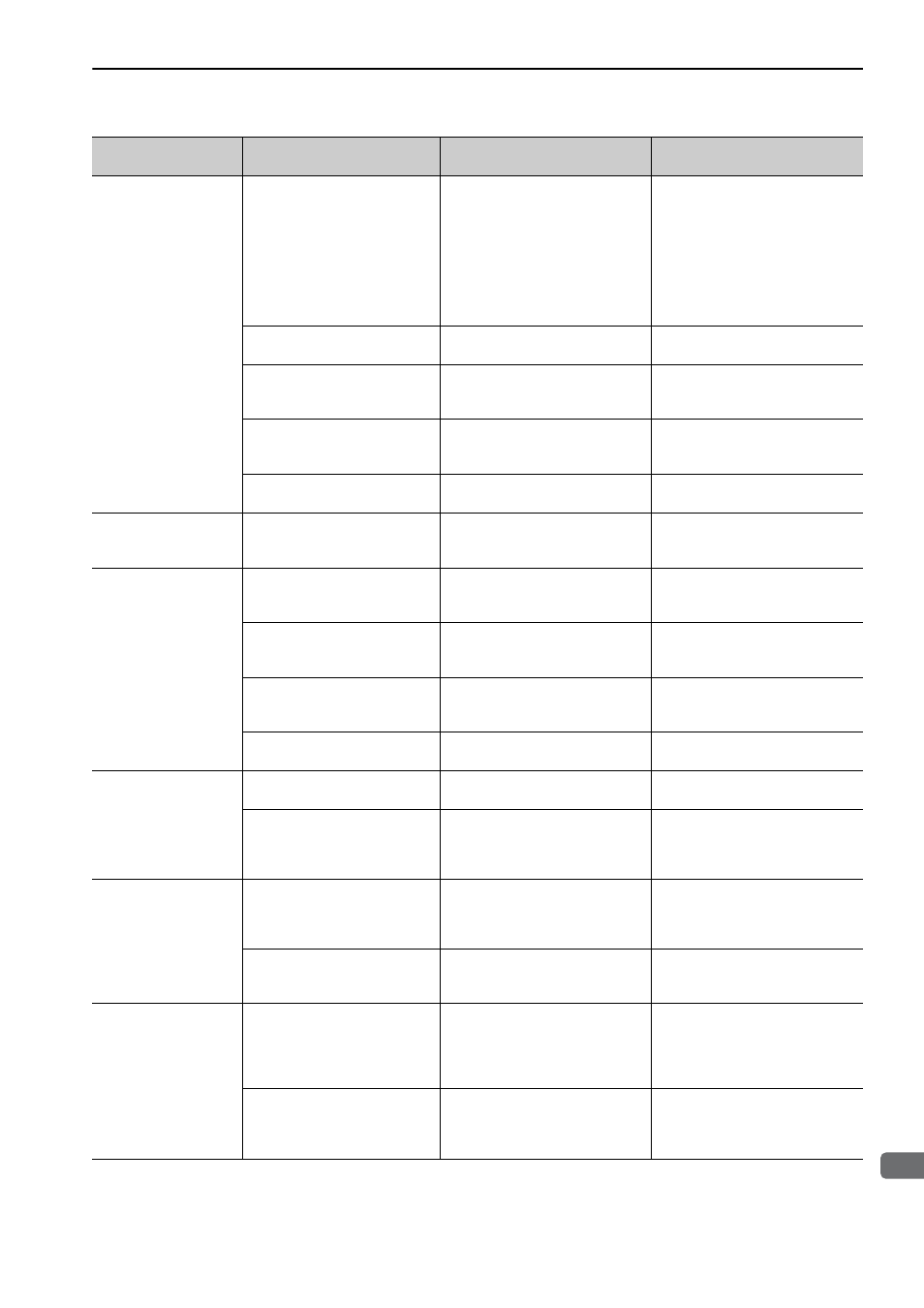
8.1 Troubleshooting
8-11
8
T
roubleshooting
A.410:
Undervoltage
(Detected in the SER-
VOPACK main circuit
power supply section.)
• For 100 VAC SERVOPACKs:
The power supply voltage is
49 V or less.
• For 200 VAC SERVOPACKs:
The power supply voltage is
120 V or less.
• For 400 VAC SERVOPACKs:
The power supply voltage is
240 V or less.
Measure the power supply voltage. Set the power supply voltage within
the specified range.
The power supply voltage
dropped during operation.
Measure the power supply voltage.
Increase the power supply capacity.
Occurrence of instantaneous
power interruption.
Measure the power supply voltage.
When the instantaneous power cut
hold time Pn509 is set, decrease the
setting.
The SERVOPACK fuse is blown
out.
−
Replace the SERVOPACK, con-
nect an AC/DC reactor, and run the
SERVOPACK.
A SERVOPACK fault occurred.
−
The SERVOPACK may be faulty.
Replace the SERVOPACK.
A.450:
Main-Circuit
Capacitor Overvoltage
A SERVOPACK fault occurred.
−
Replace the SERVOPACK.
A.510:
Overspeed
(The servomotor speed
exceeds the maximum.)
The order of phases U, V, and W
in the linear servomotor wiring is
incorrect.
Check the linear servomotor wiring. Confirm that the linear servomotor
is correctly wired.
A reference value exceeding the
overspeed detection level was
input.
Check the input value.
Reduce the reference value or adjust
the gain.
The motor speed exceeded the
maximum.
Check the linear servomotor speed
waveform.
Reduce the speed reference input
gain, adjust the servo gain, or recon-
sider the operation conditions.
A SERVOPACK fault occurred.
−
The SERVOPACK may be faulty.
Replace the SERVOPACK.
A.511:
Overspeed of Encoder
Output Pulse Rate
The encoder output pulse output
frequency exceeded the limit.
Check the encoder output pulse out-
put setting.
Decrease the setting of the encoder
output resolution (Pn281).
The encoder output pulse output
frequency exceeded the limit
because the motor speed was too
high.
Check the encoder output pulse out-
put setting and the motor speed.
Decrease the motor speed.
A.520:
Vibration Alarm
Abnormal vibration was detected
at the motor speed.
Check for abnormal noise from the
linear servomotor, and check the
speed and force waveform during
operation.
Reduce the motor speed or reduce
the speed loop gain (Pn100).
The mass ratio (Pn103) value is
greater than the actual value or is
greatly changed.
Check the mass ratio.
Set the mass ratio (Pn103) to an
appropriate value.
A.521:
Autotuning Alarm
(Vibration was detected
while executing the
advanced autotuning,
one-parameter tuning,
EasyFFT, or tuning-less
function.)
The linear servomotor vibrated
considerably while performing
tuning-less function (factory set-
ting).
Check the motor speed waveform.
Reduce the load so that the mass
ratio falls within the allowable
value, or raise the tuning level or
reduce the gain level using the tun-
ing-less function (Fn200).
The linear servomotor vibrated
considerably during advanced
autotuning, one-parameter tun-
ing, or EasyFFT.
Check the motor speed waveform.
Check the operation procedure of
corresponding function and take a
corrective action.
Alarm:
Alarm Name
Cause
Investigative Actions
Corrective Actions