3 one-parameter tuning example – Yaskawa Sigma-5 User Manual: Design and Maintenance - Rotary Motors - MECHATROLINK-II Communications Reference User Manual
Page 196
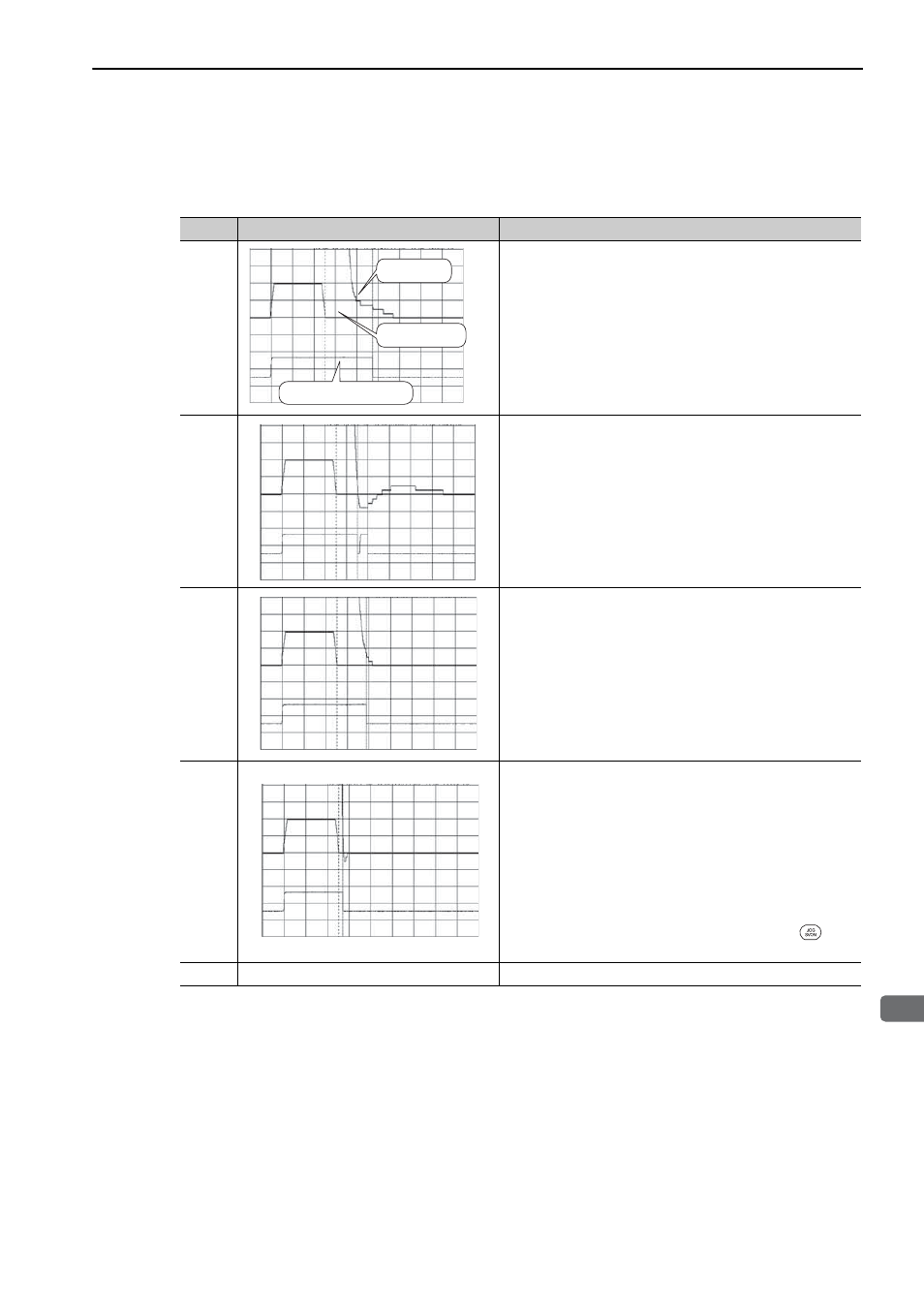
5.5 One-parameter Tuning (Fn203)
5-43
5
Adjustm
e
nts
5.5.3 One-parameter Tuning Example
The following procedure is used for one-parameter tuning on the condition that the tuning mode is set to 2 or
3. This mode is used to reduce positioning time.
Step
Measuring Instrument Display Example
Operation
1
Measure the positioning time after setting the moment of iner-
tia ratio (Pn103) correctly. Tuning will be completed if the
specifications are met here. The tuning results will be saved in
the SERVOPACK.
2
The positioning time will become shorter if the FF level is
increased. The tuning will be completed if the specifications
are met. The tuning results will be saved in the SERVOPACK.
If overshooting occurs before the specifications are met, go to
step 3.
3
Overshooting will be reduced if the FB level is increased. If the
overshooting is eliminated, go to step 4.
4
The graph shows overshooting generated with the FF level
increased after step 3. In this state, the overshooting occurs, but
the positioning settling time is shorter. The tuning will be com-
pleted if the specifications are met. The adjustment results are
saved in the SERVOPACK. If overshooting occurs before the
specifications are met, repeat steps 3 and 4.
If vibration occurs before the overshooting is eliminated, the
vibration will be suppressed by the automatic notch filter and
anti-resonance control.
Note: The vibration frequencies may not be detected if the
vibration is too small. If that occurs, press the
Key
to forcibly detect the vibration frequencies.
5
The adjustment results are saved in the SERVOPACK.
Position error
Reference speed
Positioning completed signal
M
E
C
H
A