2 iqpump keypad messages, Iqpump keypad messages, Pump fault and alarm messages – Yaskawa iQpump Controller User Manual User Manual
Page 143
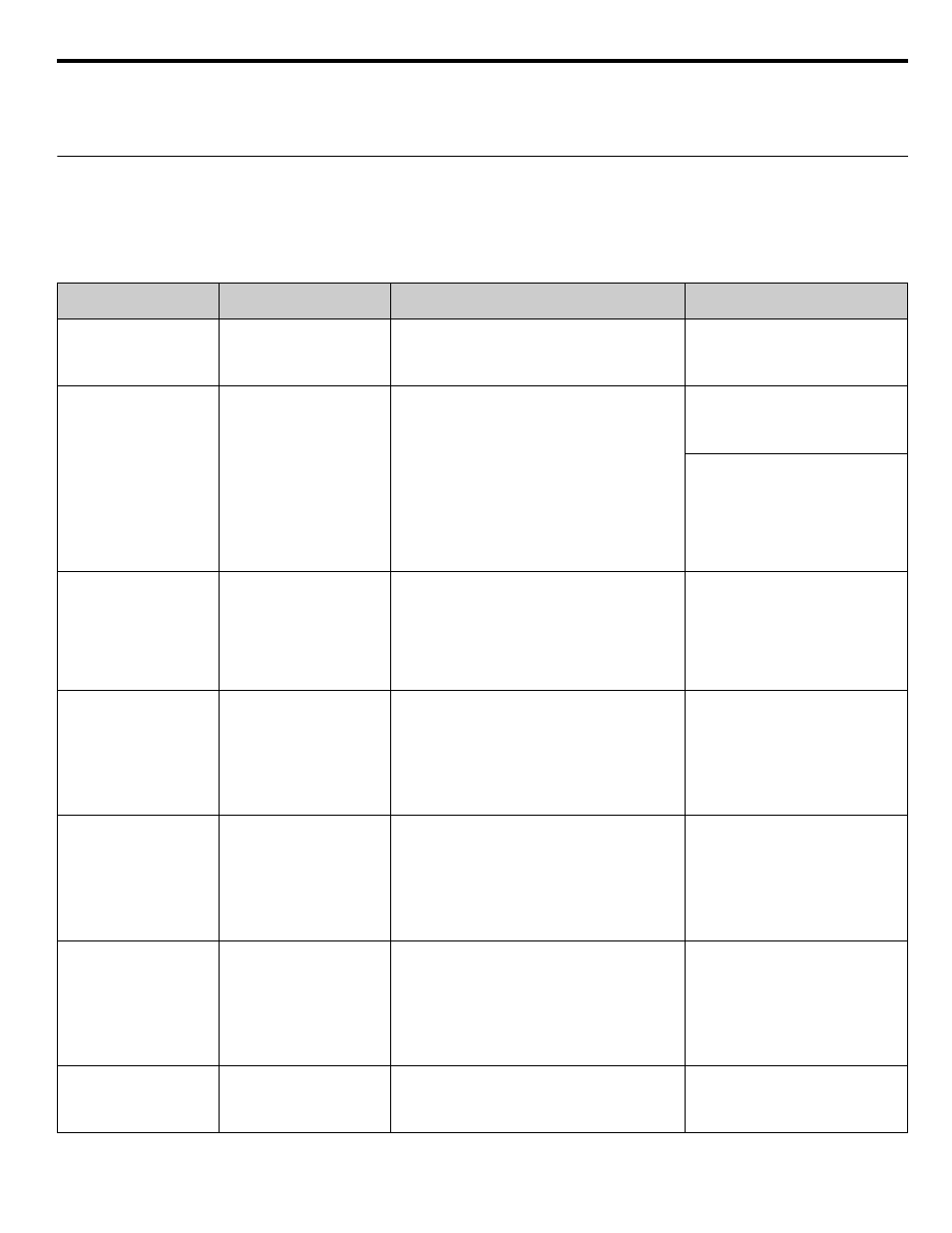
6.2 iQpump Keypad Messages
YASKAWA TM.iQp.06 iQpump Controller User Manual
143
6.2
iQpump Keypad Messages
◆ Pump Fault and Alarm Messages
The iQpump has a comprehensive set of dedicated pump alarms and faults that will alert the operator when the pump system has
experienced any problems. A warning or fault message on the operator display indicates abnormal iQpump drive status.
■
Pump Fault Messages Generated
Table 6.2 Pump Fault Messages Generated
Digital Operator
Display
Description
Cause
Corrective Action
EF1-7
Pump Fault S#
External Pump Fault
Digital input is closed.
Check incoming digital signal from
external device.
FbL
Feedback Loss
<0032>
PI Feedback Loss
This fault occurs when PI
Feedback Loss Detection is
programmed to fault (b5-12
= 2) and the PI Feedback <
PI Feedback Loss Detection
Level (b5-13) for the PI
Feedback Loss Detection
Time (b5-14).
PI Feedback source (e.g. transducer, sensor,
building automation signal) is not installed
correctly or is not working.
Verify iQpump is programmed to
receive the PI Feedback source signal.
Check to ensure the PI Feedback
source is installed and working
properly.
HFb
High Feedback
High Feedback Fault
Feedback signal is too high.
The feedback level has risen above P1-09 level for
the time specified in P1-10. High feedback fault is
active in Hand Mode, Auto Mode, Pre-charge and
Thrust Mode when the drive is running.
Feedback level lower than the high
feedback level (P1-09).
LFb / LW
Low FB / Water
Low Feedback Level Fault
Feedback signal is too low or
water low input closed.
The feedback level has dropped below P1-07 for
the time specified in P1-08 or water low input is
active. Low feedback fault is active in Auto Mode
when the iQpump is running. Digital input is
closed.
Feedback level greater than the low
feedback level (P1-07). Check
incoming digital signal from external
device.
LoP
Loss of Prime
<0032>
Loss of Prime Fault
Pump has lost its prime.
If the output current drops below the P1-14 Prime
Loss Level for the time specified in P1-16 and the
output frequency is at fmax, a “Loss of Prime
(LOP)” fault occurs
Possible cause: Dry Well, Air in System, No Water
Allow system to pump water again
(must have resistance in pump).
nMS
Set Point Not Met
<0032>
Not Maintaining Set Point
Fault
Set Point cannot be
maintained.
When the setpoint cannot be maintained for a time
specified in P1-12, a “Not Maintaining Setpoint
(NMS)” fault occurs. The function is disabled
when the drive is not running and the PID is not
active.
Possible cause: Blocked Impeller, Over-Cycling,
Broken Pipe
Reduce the difference between the
setpoint and the feedback smaller than
the Maximum Setpoint Difference
(P1-11).
oPE12
<0032>
Thermostat Fault Selection
Fault
Both Normally Open (H1-xx = 83) and the
Normally Closed (H1-xx = 87) Thermostat Fault
inputs have been programmed
Only use one of the two fault inputs.