B2-02 dc injection braking current, B2-09 motor pre-heat current – Yaskawa iQpump Controller User Manual User Manual
Page 99
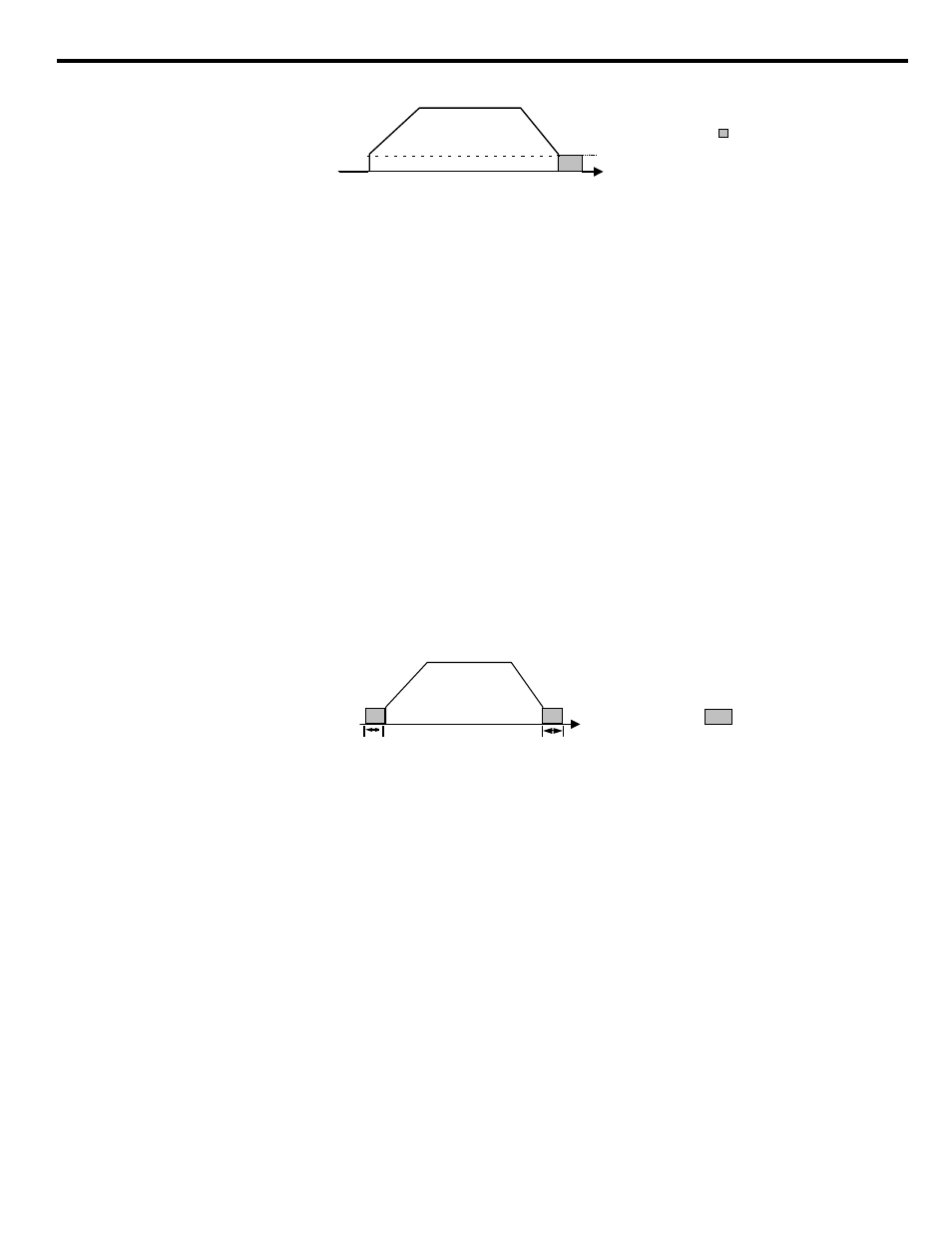
5.1 iQpump Drive Basic Programming Parameters
YASKAWA TM.iQp.06 iQpump Controller User Manual
99
Figure 5.10
Figure 5.13 DC Injection Braking During Stopping
■
b2-02 DC Injection Braking Current
Setting Range: 0 ~ 100 %
Factory Default: 50 %
The level of DC Injection Braking Current affects the strength of the magnetic field attempting to lock the motor shaft. Increasing the
level of current will increase the amount of heat generated by the motor windings and should only be increased to the level necessary to
hold the motor shaft. DC Injection current is set in percentage of iQpump drive rated output current. The iQpump drive rated output
current is stated on the iQpump drive nameplate.
■
b2-03 DC Injection Braking Time at Start
b2-04 DC Injection Braking Time at Stop
Setting Range: 0.00 ~ 10.00 s
Factory Default: b2-03 = 0.00 s
Factory Defau lt:
b2-04 = 0.00 s
The iQpump drive can be programmed to automatically DC Inject for a predetermined amount of time prior to accelerating to speed (b2-
03) and / or at the end of a Ramp to stop (b2-04). Parameter b2-03 can be used to stop a rotating motor prior to attempting acceleration
(i.e. a wind milling fan). If DC Injection braking at start or Speed Search is not enabled, attempting to iQpump drive a spinning motor
may cause nuisance tripping.
Parameter b2-04 can be used to resist any residual motion of the load after the deceleration has finished.
Figure 5.11
Figure 5.14 DC Injection Braking During Starting and Stopping
Parameter b2-04 also affects the length of time DC Injection to Stop (b1-03 = “2: DC Injection to Stop”) will occur.
■
b2-09 Motor Pre-Heat Current
Setting Range: 0 ~ 100 %
Factory Default: 0 %
A DC current can be circulated within the motor windings while the motor is stopped. The current will produce heat within the motor and
prevent condensation. Parameter b2-09 determines the percentage of iQpump drive rated output current that will be used for the motor
pre-heat function. This function can be useful in applications where the motor sits for extended periods of time in humid conditions.
Motor pre-heating can only be initiated by closing a digital input programmed as a Motor Pre-heat Input (H1-0x = 60). Check with the
motor manufacturer to determine the maximum acceptable current level the motor can withstand when stopped. Be sure not to exceed the
motor manufacturers recommended level.
Output Frequency
t
b2-01
DC injection
|
|
b2-04
ime
Output Frequency
DC injection
b2-03 b2-04