Yaskawa iQpump Controller User Manual User Manual
Page 82
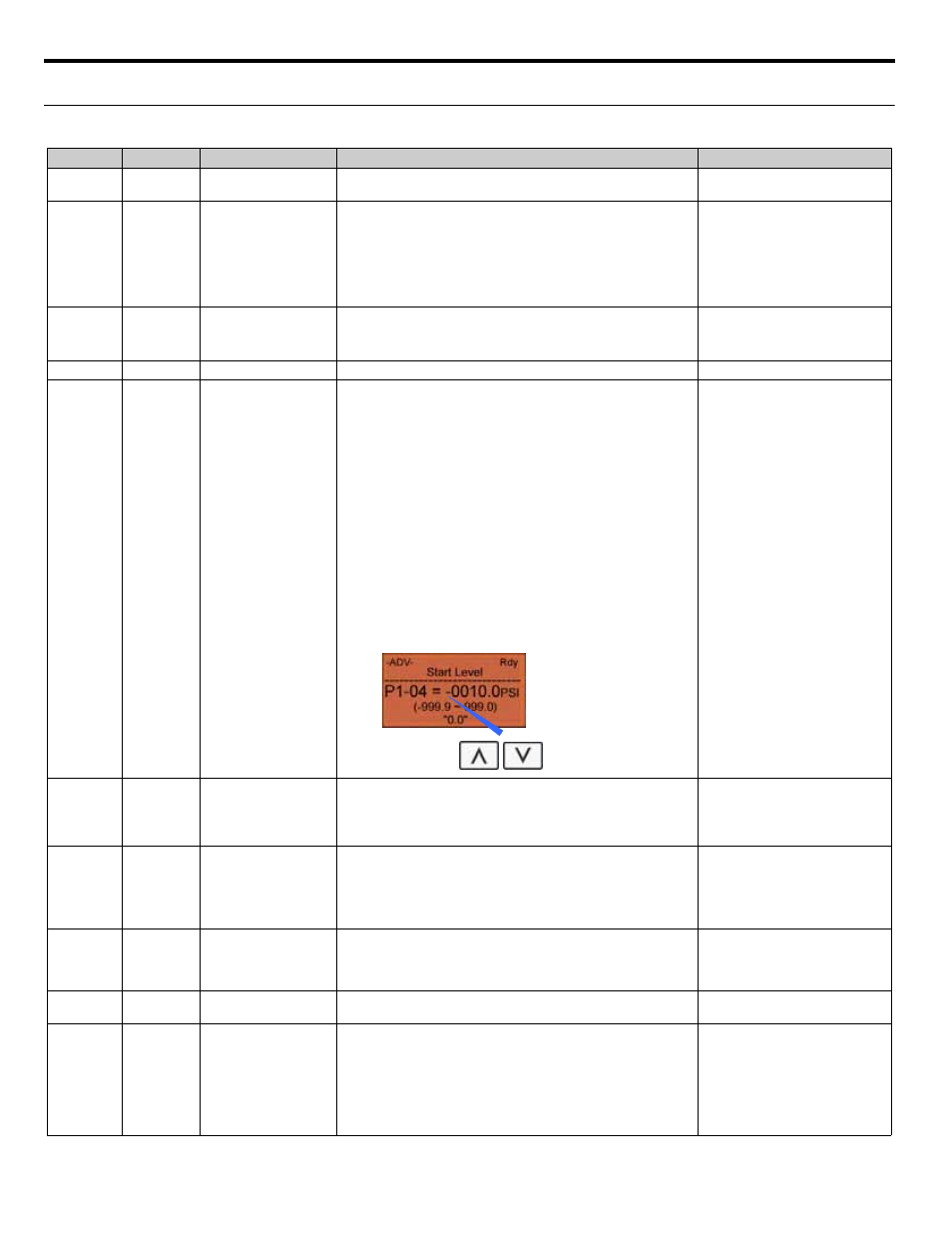
4.2 iQpump Drive Quick Start-Up Procedures
82
YASKAWA TM.iQp.06 iQpump Controller User Manual
◆ Step # 5 - iQpump Drive Quick Setup Parameter Overview (Simplex)
Parameter
Value
Description
Reference
Comments
E2-01
Drive Size
Dependent
Motor Rated Current
Set to the motor nameplate full load amps.
For submersible motors use service
factor amps (SFA).
E2-04
2
Number of Motor Poles
Number of motor poles is used to show the correct motor RPM on the
display. Enter “4” for an 1800 RPM motor and “2” for a 3600 RPM
motor.
Confirm number of poles:
2 pole motor - 3600 RPM
4 pole motor - 1800 RPM
6 pole motor - 1200 RPM
8 pole motor - 900 RPM
P1-03
145
Feedback Device Scaling
System Scaling: Enter feedback device maximum.
Example: Enter 200 for pressure transducer with a maximum of 200 psi
at 20 mA.
Confirm feedback device scaling.
)
d1-01
0
Setpoint 1
Set System Setpoint
Set to system pressure.
P1-04
0.0 psi
Start Level
When the iQpump is turned On and the feedback signal level
(transducer) falls below this level, the pump system will start after the
time specified in P1-05 (default 1 sec).
Programming the Start Level as an Absolute Value
Start Level has to programmed to a positive value in order for the Start
Level to be an absolute value. Example: Start Level P1-04 set to 50 PSI
and delay time P1-05 set to 5 sec. Pump system will start when the
pressure drops below 50 PSI for 5 sec.
Programming the Start Level as a Delta Level from the System
Setpoint
Start Level has to programmed to a negative value in order for the Start
Level to be a delta value from the setpoint.
Example: Start Level P1-04 set to –10 PSI with a system setpoint of 50
PSI and a delay time P1-05 set to 5 sec. Pump system will start when the
pressure drops below 40 PSI (50 - 10) for 5 sec.
It is mandatory to program the Start
Level in order to use the sleep
function.
)
P1-06
40.0 Hz
Minimum Pump
Frequency
Minimum speed (Hz) the pump motor has to operate at.
Example: Base pump motor speed is 3600 RPM, minimum speed is
2400 RPM. Set the minimum pump frequency to 40.0 Hz
(2400 ÷ 3600 x 60 Hz = 40 Hz)
Minimum pump frequency should be
set to a value where the pump enters
the no-flow condition.
P4-10
0
Disabled
Auto Mode Operator Run
Power Down Storage
Stores the run status in the Auto Mode when operating from digital
operator (b1-02 = 0)
0: Disabled
1: Enabled
Recommended for use when Start /
Stop command is from keypad.
P5-04
1
Enabled
Hand Key
Enable / Disable
Enables or disables the Hand Key on the digital operator.
0: Disabled
1: Enabled
Hand Key on keypad.
)
b5-03
3.0 s
PI Integral Time
Decrease integral time to make iQpump more responsive.
NOTICE: May cause system
instability if this value is too low.
b5-12
2
(Fault)
PI Feedback Reference
Missing Detection
Selection
Select what to do when the feedback device (transducer) fails or gets
disconnected.
0: Disabled, continue running no message is displayed.
1: Alarm, show warning on the keypad when the feedback device fails
or is disconnected.
2: Fault, stop pump system when the feedback fails or is disconnected.
Note: Disable parameter b5-12 if no
transducer is installed.
Use to change the sign.