Related parameters – Yaskawa iQpump Controller User Manual User Manual
Page 216
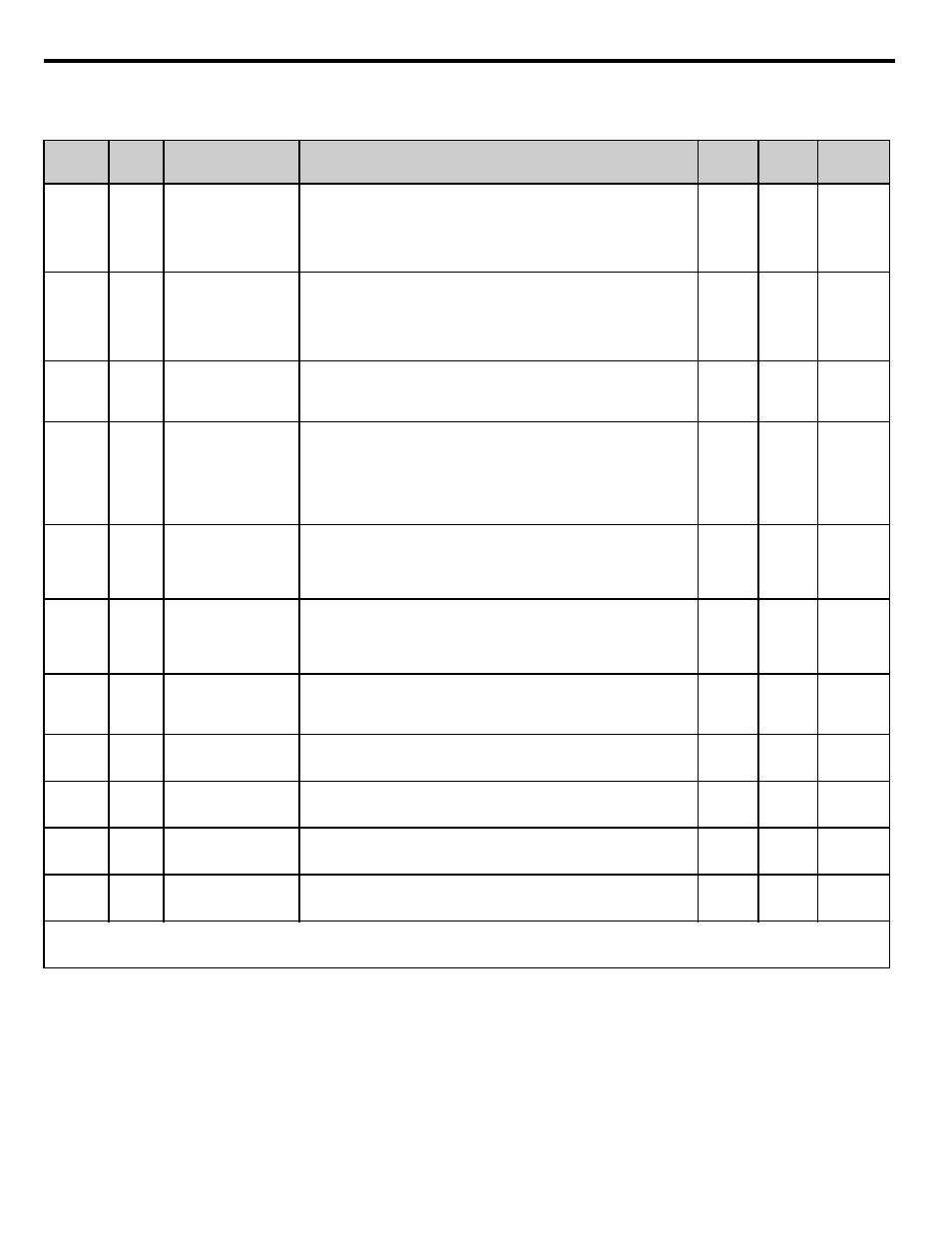
216
YASKAWA
TM.iQp.06 iQpump Controller User Manual
D.1 Using Modbus Communication
■
Related Parameters
Table D.2 Serial Communication Related Parameters
Modbus communication can perform the following operations regardless of the settings in b1-01 and b1-02:
1. Monitoring operation status of the iQpump drive.
2. Setting and reading iQpump drive parameters.
3. Resetting faults.
4. Input multi-function commands.
IMPORTANT: An OR operation is performed between the multi-function command input from the DDC and the command input from
multi-function digital input terminals S3 to S7.
Parameter
No.
Modbus
Address
Parameter Name
Digital Operator
Display
Description
Setting
Range
Factory
Setting
Menu
Location
b1-01
0180H
Frequency Reference
Selection
Reference Source
Selects the speed command (frequency reference) input source.
0: Operator - Digital preset speed d1-01
1: Terminals - Analog Input Terminal A1 (or Terminal A2 see parameter H3-
13)
2: Serial Com - RS-485 terminals R+, R-, S+ and S-
3: Option PCB - Option board connected at 2CN
0 ~ 3
0
Programming
b1-02
0181H
Run Command Selection
Run Source
Selects the run command input source.
0: Operator - “Hand” and “Off” keys on digital operator
1: Terminals - Contact Closure on Terminal S1
2: Serial Com - RS-485 terminals R+, R-, S+ and S-
3: Option PCB - Option board connected at 2CN
5: Timed Run
<0034>
0 to 3, 5
0
Programming
H5-01
0425
Drive Node Address
Serial Com Adr
Selects drive station node number (address) for Terminals R+, R-, S+, S-.
Note: An address of “0” disables serial com.
Drive power must be cycled before the changes will take effect.
*Range is dependent on P9-25, if P1-01 = 3.
<0034>
0 ~ 20*
1F
Programming
H5-02
0426
Communication Speed
Selection
Serial Baud Rate
Selects the baud rate for Terminals R+, R-, S+ and S-.
0: 1200 Baud
1: 2400 Baud
2: 4800 Baud (APOGEE FLN)
3: 9600 Baud (Metasys N2)
4: 19200 Baud
Note: Drive power must be cycled before the changes will take effect.
<0034>
0 ~ 4
3
Programming
H5-03
0427
Communication Parity
Selection
Serial Com Sel
Selects the communication parity for Terminals R+, R-, S+ and S-.
0: No Parity
1: Even Parity
2: Odd Parity
Note: Drive power must be cycled before the changes will take effect.
<0034>
0 ~ 2
0
Programming
H5-04
0428
Stopping Method after
Communication Error
Serial Fault Sel
Selects the stopping method when a communication error is detected.
0: Ramp to Stop
1: Coast to Stop
2: Fast-Stop
3: Alarm Only
0 ~ 3
3
Programming
H5-05
0429
Communication Error
Detection Selection
Serial Flt Dtct
Enables or disables the communications timeout detection function.
0: Disabled - A communications loss will NOT cause a communications fault.
1: Enabled - If communications are lost for more than the time specified in
parameter H5-09, a communications fault will occur.
0 ~ 1
1
Programming
H5-06
042A
Drive Transmit Wait
Time
Transmit WaitTIM
Sets the time from when the drive receives data to when the drive sends data.
5 ~ 65
5 ms
Programming
H5-07
042B
RTS Control Selection
RTS Control Sel
Enables or disables “request to send” (RTS) control:
0: Disabled (RTS is always on)
1: Enabled (RTS turns on only when sending)
0 ~ 1
1
Programming
H5-08
042C
Communication Protocol
Selection
Com Protocol Sel
0: MEMOBUS / Modbus
1: N2 (Metasys)
2: FLN (APOGEE)
0 ~ 2
0
Programming
H5-09
0435
Communication Error
Detection Time
CE Detect Time
Determines how long communications must be lost before a fault is
annunciated. Works in conjunction with parameters H5-05 and H5-04.
0.0 ~ 10.0
2.0 s
Programming
Denotes that parameter can be changed when the iQpump drive is running.
* After these parameters are changed, iQpump drive power must be cycled before the changes will take effect.
# Hex