Details of preprogrammed logic schemes, Factory default logic settings, Operation - protection – Basler Electric BE1-851 User Manual
Page 159: Operation - setting group selection, Operations - alarms, Details of preprogrammed logic schemes -3, Factory default logic settings -3, Operation - protection -3, Operation - setting group selection -3, Operations - alarms -3
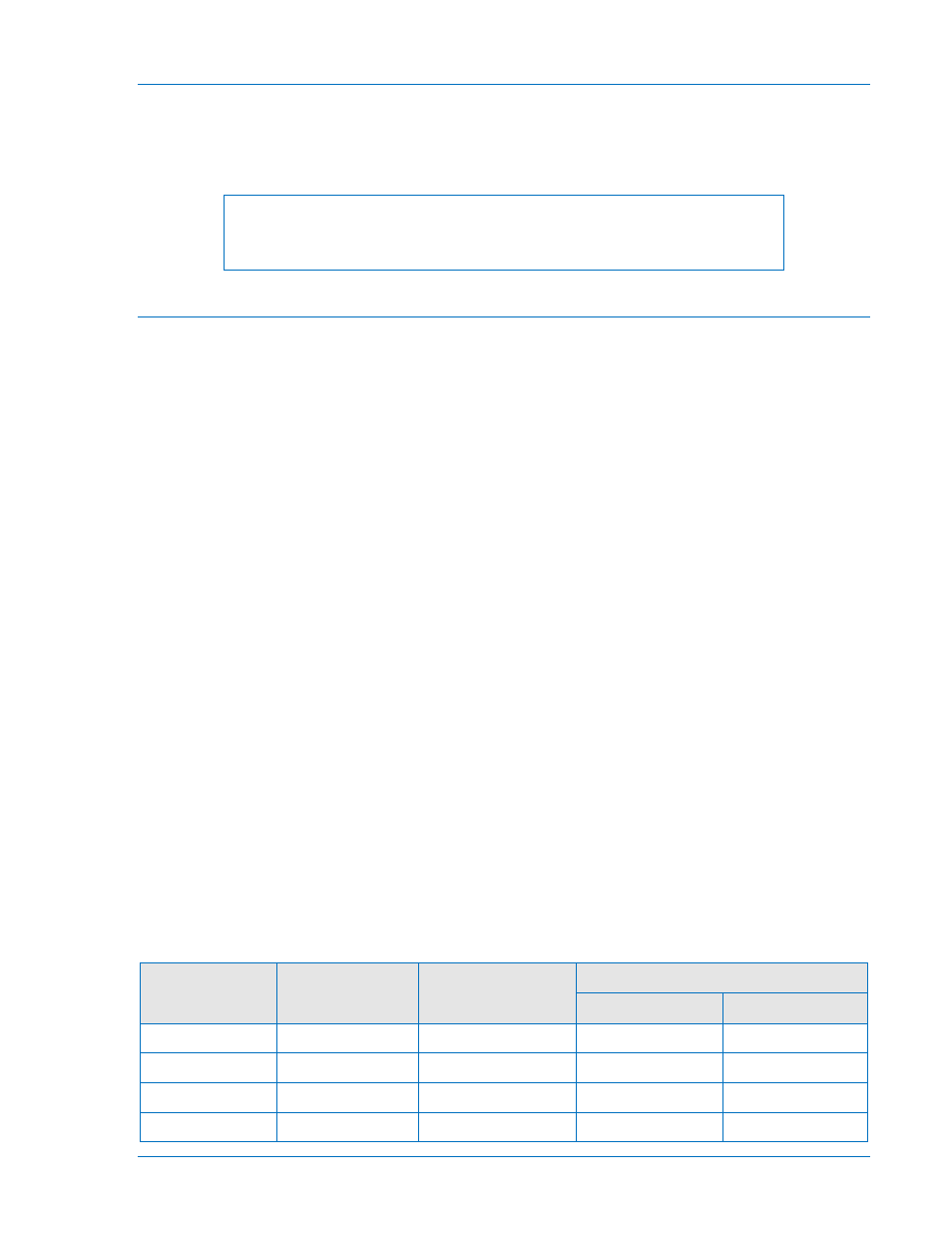
Details of Preprogrammed Logic Schemes
The following sub-sections describe each of the six preprogrammed logic schemes in detail. For each
scheme, the operation of the protection and control logic under normal conditions is described. The
features of each logic scheme are broken down into functional groupings and described in detail. This is
followed by a discussion of how various contingencies are covered by each logic scheme.
NOTE
Name Labels are limited to ten characters and State Labels are limited to
seven characters.
Factory Default Logic Settings
Logic scheme USER is intended for applications requiring three-phase and neutral non-directional
overcurrent protection. While not as elaborate as the other preprogrammed schemes, this logic scheme
provides an excellent base on which to create a custom scheme for a specific application.
The components of USER logic are summarized in Tables 8-1 through 8-4. Figure 8-1 is a one-line
diagram of USER logic and Figure 8-2 is a diagram representing the logic settings and equations of
USER logic.
Operation - Protection
The phase, neutral, or negative-sequence elements are activated to provide timed (51) and instantaneous
(50) overcurrent protection in this scheme. A function block is disabled by setting the pickup setpoint at
zero in each of the four setting groups. Virtual output VO11 is assigned for all protective trips. When
VO11 becomes TRUE, OUT1 will operate and trip the breaker. Contact outputs OUT2, OUT3, OUT4, and
OUT5 are designated to specific function blocks. OUT2 operates for instantaneous phase overcurrent
conditions, OUT3 trips for timed phase overcurrent situations, OUT4 operates for instantaneous neutral
and negative-sequence overcurrent conditions, and OUT5 operates for timed neutral and negative-
sequence overcurrent conditions.
All contact sensing inputs are unassigned, but IN1 is typically assigned to monitor breaker status (52b).
Inputs IN2, IN3, and IN4 are available for user specified functions.
Voltage protection, frequency protection, automatic reclosing, breaker failure, breaker control, and virtual
switches are not included in this logic scheme.
Operation - Setting Group Selection
A setting group can be selected automatically or by using the communication ports or the front panel HMI.
Automatic setting group changes are based on current level and duration. Automatic setting group
changes for cold load pickup and/or dynamic setting adjustments are enabled by the SP-GROUP#
command. Setting group changes initiated by contact sensing inputs are not accommodated in this
scheme, but IN2, IN3, or IN4 can be programmed to provide this function.
Operations - Alarms
If the continuous self-test diagnostics of the relay detect an error, failsafe output contact OUTA will
change states and the Relay Trouble LED of the HMI will light. OUTA will also change states if relay
operating power is lost. More information about alarms is provided in Section 6, Reporting and Alarms.
Table 8-1. Factory Default Contact Sensing Input Logic Settings
Input
Purpose
Name Label
State Labels
Energized
De-Energized
IN1
N/A
INPUT_1
TRUE
FALSE
IN2
N/A
INPUT_2
TRUE
FALSE
IN3
N/A
INPUT_3
TRUE
FALSE
IN4
N/A
INPUT_4
TRUE
FALSE
9289900990 Rev R
BE1-851 Application
8-3