Setting group selection, Output contact seal-in, Setting group selection -64 – Basler Electric BE1-851 User Manual
Page 220: Output contact seal-in -64
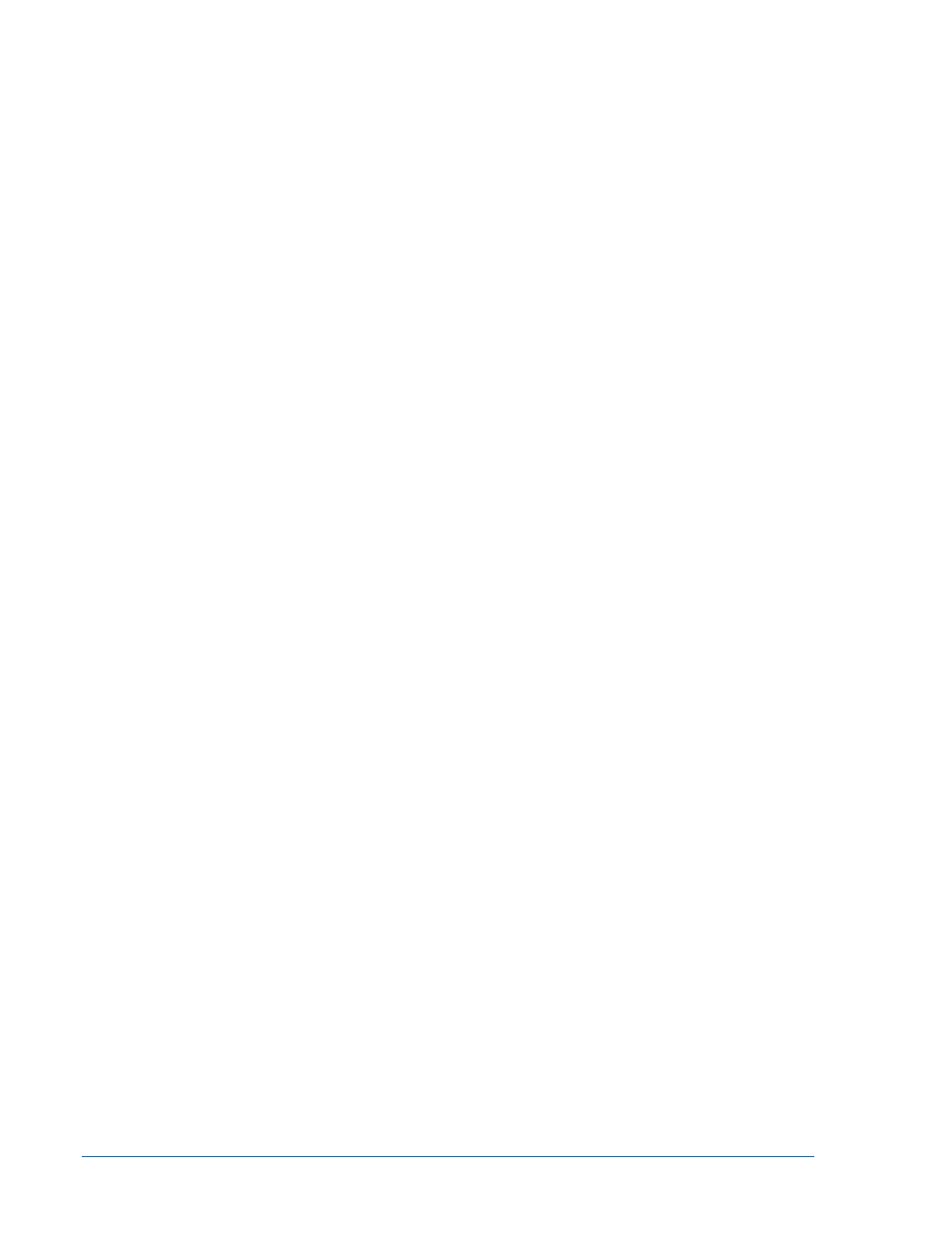
However, distribution systems with single pole fault clearing and switching devices or long single-phase
laterals may have mis-operations during switching activities.
The preprogrammed logic schemes provide for the use of a cutoff switch to block the ground and
negative-sequence 50T (used for low set instantaneous) and the 51 (inverse time) function blocks during
switching activities. This is the most conservative approach. The protection engineer may wish to
evaluate this strategy based on his/her system, operating practices, and setting practices. For instance,
on systems with wye-connected loads, the ground units are most sensitive to this situation. It may not be
necessary to block the instantaneous units if their settings prevent them from tripping for a switching
imbalance. To maintain proper coordination, the logic of the feeder relays may be interconnected with the
upstream bus relay to block the equivalent ground and/or negative-sequence function blocks in the
upstream relay.
Setting Group Selection
The BE1-851 Overcurrent Protection System provides multiple settings groups for adaptive relaying. The
preprogrammed logic schemes barely tap the flexibility that is available. The following examples illustrate
how the settings groups can be adapted for different conditions and how different setting groups can be
used to vary the system logic.
Example 1. Adapting the relay settings for different conditions.
In overcurrent protection systems, the source conditions can have a major impact on sensitivity,
coordination intervals, and clearing times. Generally, the pickup and time dial settings are a compromise
between a normal condition and a worst-case condition. Contact logic from the position of the source
breakers can select which settings group is active. To do this, assign input D0 or D1 to a contact sensing
input. Set the Setting Group Selection Mode at 2 for binary coded selection. If D0 is set, Group 0 will be
selected when the input is off (binary code 00). Group 1 will be selected when the input is on (binary code
01). Similarly, if D1 is set, Group 2 will be selected when the input is on (binary coded 10).
This logic is useful in a situation where two transformers feed a single bus or two busses have a bus tie
between them. The feeder and bus relays must be coordinated for the situation where only one source is
in service (bus tie open or one transformer out of service). However, when both sources are in service,
such as when the bus tie is closed, each bus relay sees only half of the current for a fault. This results in
poor sensitivity and slow clearing time for the bus relays.
Example 2. Adapting the logic in different setting groups.
The logic in most of the preprogrammed logic schemes can be varied in each of the different setting
groups. This is accomplished by disabling functions by setting their primary settings at zero. It is also
possible to do more sophisticated modification of the logic in each of the different setting groups by using
the active setting group logic variables SG0, SG1, SG2, and SG3 in the BESTlogic expressions.
Output Contact Seal-In
Trip contact seal-in circuits have historically been provided with electromechanical relays. These seal-in
circuits consisted of a dc coil in series with the relay trip contact and a seal-in contact in parallel with the
trip contact. The seal-in feature serves several purposes for the electromechanical relays. One is to
provide mechanical energy to drop the target. Second is to carry the dc tripping current from the induction
disk contact that may not have significant closing torque for a low resistance connection. The third is to
prevent the relay contact from dropping out until the current has been interrupted by the 52a contacts in
series with the trip coil. If the tripping contact opens before the dc current in interrupted, the contact may
be damaged. The first two of these items are not an issue for solid-state relays but the third item is an
issue.
To prevent the output relay contacts from opening prematurely, a 200 millisecond hold timer can be
selected with the SG-HOLDn=1 command. Refer to Section 3, Input and Output Functions, for more
information on this feature. If the protection engineer desires seal-in logic with feed back from the breaker
position logic, he/she can provide this logic by modifying the BESTlogic expression for the tripping output.
To do this, use one of the general purpose timers 62 or 162 and set it for Mode 1 (Pickup/Dropout Timer).
Set the timer logic so that it is initiated by the breaker position input and set the timer for two cycles
pickup and two cycles dropout. Then AND the timer output with the tripping output and OR it into the
expression for the tripping output. The same can be done for the closing output. Figure 8-19 provides a
seal-in logic diagram.
8-64
BE1-851 Application
9289900990 Rev R