2 advanced autotuning procedure, Caution, 1) operating procedure – Yaskawa Sigma-5 User Manual: Design and Maintenance - Rotary Motors User Manual
Page 154
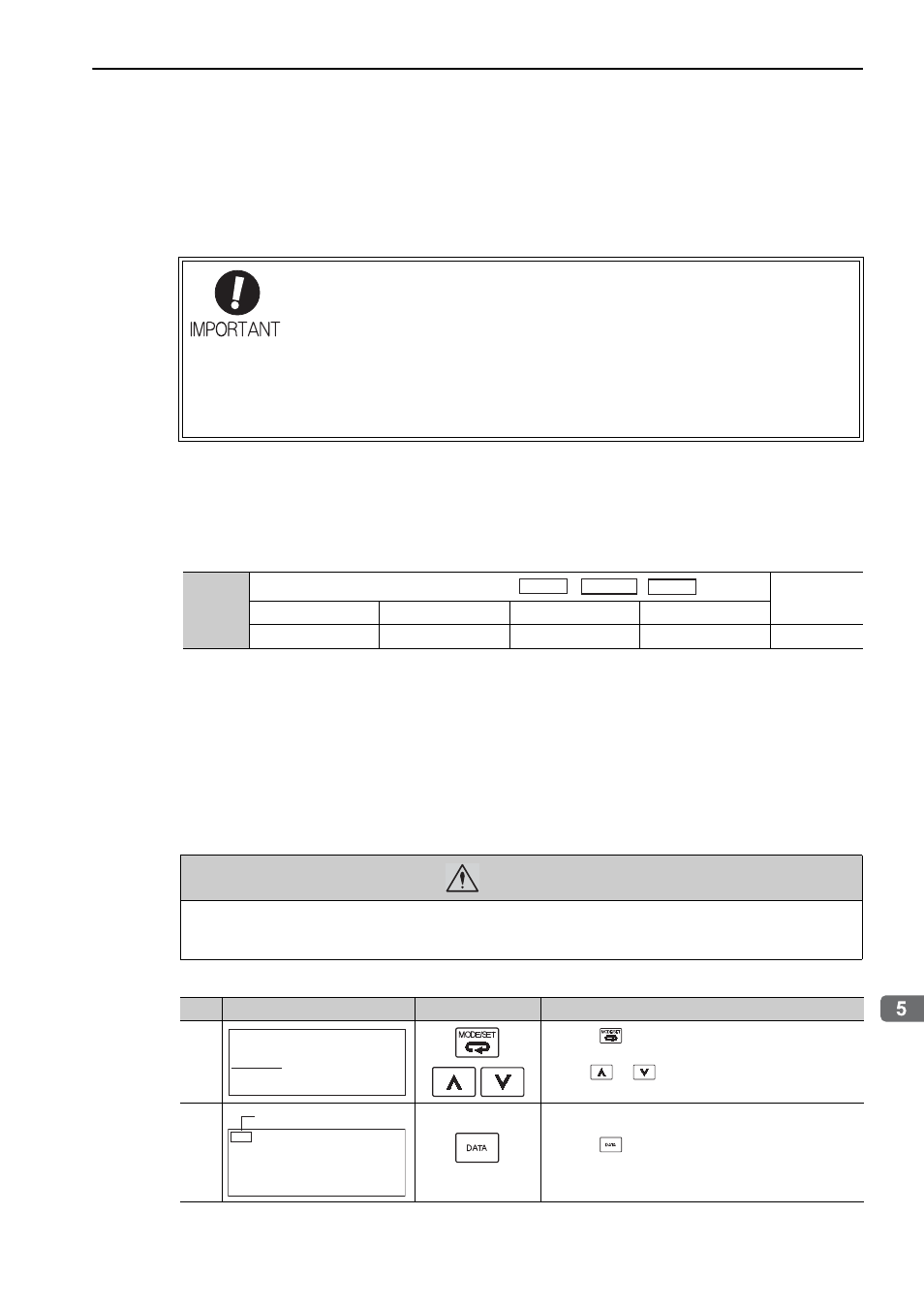
5.3 Advanced Autotuning (Fn201)
5-17
Adjustments
• The mode switch is used.
Note:If a setting is made for calculating the moment of inertia, the mode switch function will be disabled while the
moment of inertia is being calculated. At that time, PI control will be used. The mode switch function will be
enabled after calculating the moment of inertia.
• Speed feedforward or torque feedforward is input.
• The positioning completed width (Pn522) is too small.
Change only the overshoot detection level (Pn561) to finely adjust the without changing the positioning com-
pleted width (Pn522). Because Pn561 is set by default to 100%, the allowable amount of overshooting is the
same amount as that for the positioning completed width.
When Pn561 is set to 0%, the amount of overshooting can be adjusted to prevent any overshooting in the posi-
tioning completed width. If the setting of Pn561 is changed, however, the positioning time may be extended.
5.3.2 Advanced Autotuning Procedure
The following procedure is used for advanced autotuning.
Advanced autotuning is performed from the Digital Operator (option) or SigmaWin+.
The operating procedure from the Digital Operator is described here.
For the basic operations of the Digital Operator, refer to the
Σ
-V series User’s Manual, Operation of Digital
Operator (SIEP S800000 55).
(1) Operating Procedure
• Advanced autotuning makes adjustments based on the positioning completed width
(Pn522). If the SERVOPACK is operated in position control, set the electronic gear
ratio (Pn20E/Pn210) and positioning completed width (Pn522) to the actual value dur-
ing operation. If the SERVOPACK is operated in speed control, use the factory set-
tings.
• Unless the positioning completed signal (/COIN) is turned ON within approximately 3
seconds after positioning has been completed, “WAITING” will blink. Furthermore,
unless the positioning completed signal (/COIN) is turned ON within approximately 10
seconds, “Error” will blink for 2 seconds and tuning will be aborted.
Pn561
Overshoot Detection Level
Classification
Setting Range
Setting Unit
Factory Setting
When Enabled
0 to 100
1%
100
Immediately
Setup
Speed
Position
Torque
CAUTION
• When using the SERVOPACK with Jcalc = OFF (load moment of inertia is not calculated), be sure to set a
suitable value for the moment of inertia ratio (Pn103). If the setting greatly differs from the actual moment
of inertia ratio, normal control of the SERVOPACK may not be possible, and vibration may result.
Step
Display after Operation
Keys
Operation
1
Press the
Key to view the main menu for the utility
function mode.
Use the
or
Key to move through the list, select
Fn201.
2
Press the
Key to display the initial setting screen
for advanced autotuning.
㧮㧮 ޓ̆㧲㨁㧺㧯㨀㧵㧻㧺̆
㧲㨚㧞㧜㧜㧦㨀㨡㨚㨑㧸㨢㨘ޓ㧿㨑㨠
㧲㨚㧞㧜㧝㧦㧭㧭㨀
㧲㨚㧞㧜㧞㧦㧾㨑㨒㧭㧭㨀
㧲㨚㧞㧜㧟㧦㧻㨚㨑㧼㨞㨙㨀㨡㨚
㧮㧮 㧭㨐㨢㨍㨚㨏㨑㨐ޓ㧭㨀
ޓ㧶㨏㨍㨘㨏㧩㧻㧺
ޓ㧹 㨛 㨐 㨑㧩㧞ޓ㨀㨥㨜㨑㧩㧞
ޓ㧿㨠㨞㨛㨗㨑㧩㧗㧜㧜㧤㧜㧜㧜㧜㧜
ޓޓޓޓޓޓ㧔㧜㧜㧜㧟㧚㧜㧕㨞㨑㨢
Status Display