2 troubleshooting of warnings – Yaskawa Sigma-5 User Manual: Design and Maintenance - Rotary Motors User Manual
Page 289
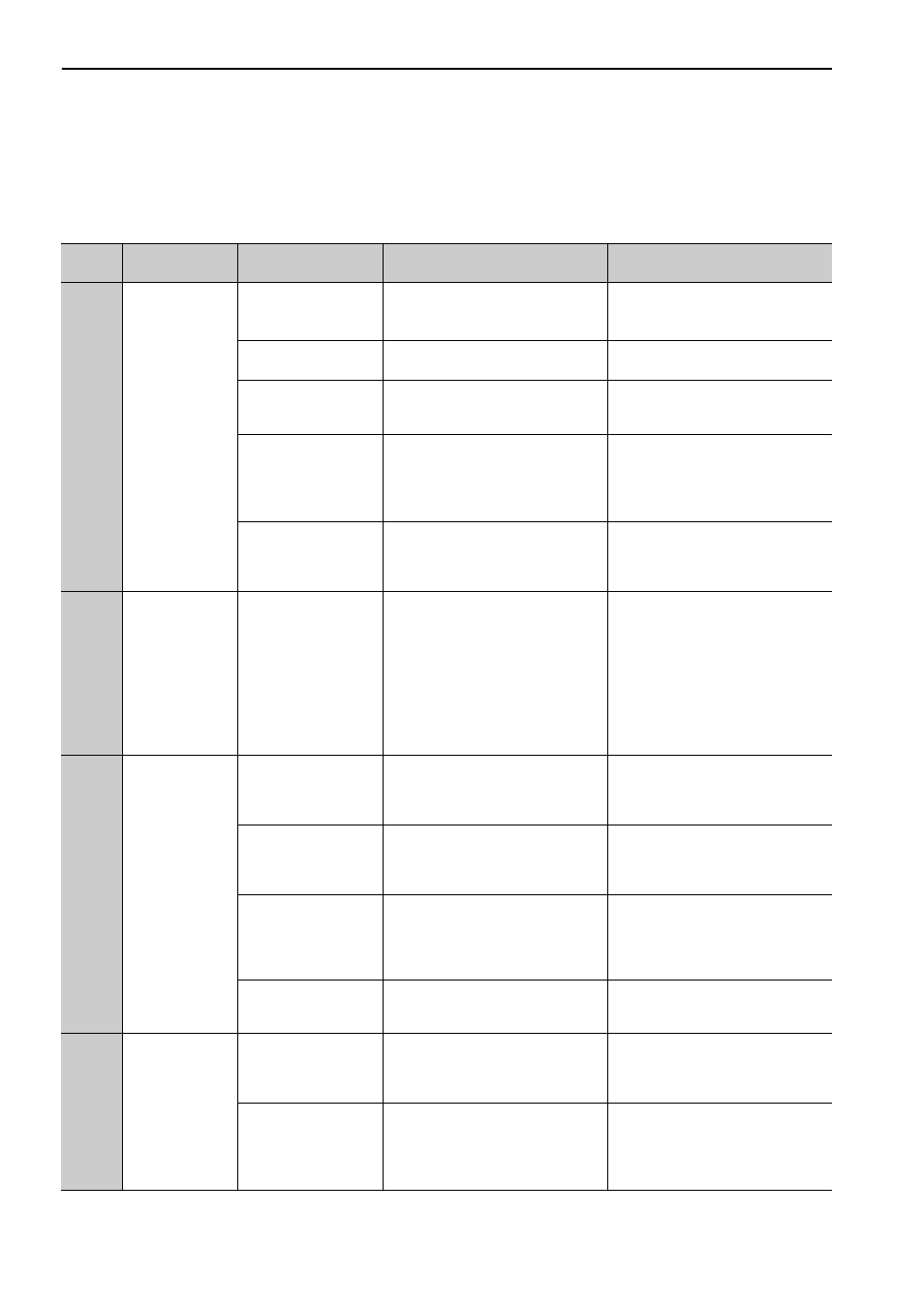
9 Troubleshooting
9.2.2 Troubleshooting of Warnings
9-24
9.2.2 Troubleshooting of Warnings
Refer to the following table to identity the cause of a warning and the action to be taken. Contact your
Yaskawa representative if the problem cannot be solved by the described corrective action.
Warning
Display
Warning Name
Situation at Warning
Occurrence
Cause
Corrective Actions
A.900
Position Error
Pulse Overflow
Wiring of the servomo-
tor U, V, or W line is
incorrect.
Check the wiring of the cable for
motor main circuit.
Check whether there is any loose con-
nection in motor wiring or encoder
wiring.
The SERVOPACK gain
is too low.
Check the SERVOPACK gain.
Increase the servo gain by using the
function such as advanced autotuning.
The position reference
acceleration is too high.
Lower the position reference accelera-
tion.
Apply a smoothing function, such as a
position reference acceleration/decel-
eration time constant (Pn216).
The excessive position
error alarm level
(Pn520) is too low for
the operating condi-
tions.
Check the excessive position error
alarm level (Pn520).
Set an appropriate value for the
Pn520.
A SERVOPACK fault
occurred.
−
Turn the power supply OFF and then
ON again. If the alarm still occurs, the
SERVOPACK may be faulty. Replace
the SERVOPACK.
A.901
Position Error
Pulse Overflow
Alarm at Servo
ON
When the servomotor
power was OFF, the ser-
vomotor moved with-
out clearing the counter
for position error
pulses. The number of
position error pulses
exceeded the maximum
number of pulses
allowed.
–
Make the setting so that the position
error pulse is cleared when the servo is
OFF.
Or, set an appropriate value for the
excessive position error warning level
at servo ON (Pn528).
A.910
Overload:
Warning before
alarm A.710 or
A.720 occurs
The servomotor or
encoder wiring is incor-
rect or the connection is
faulty.
Check the wiring.
Correct the servomotor and encoder
wiring if they are wrong.
The servomotor is in
excess of the overload
protective characteris-
tics.
Check the overload characteristics of
the servomotor and reference input.
Reconsider the load and operation
conditions.
Or, check the servomotor capacity.
The servomotor is not
driven due to a mechan-
ical factor and the oper-
ating load has become
excessive.
Check the reference input and motor
speed.
Improve the mechanical factor.
A SERVOPACK fault
occurred.
−
The SERVOPACK may be faulty.
Replace the SERVOPACK.
A.911
Vibration
Abnormal vibration was
detected while the
motor was rotating.
Check whether unusual sound is gen-
erated from the motor, and check the
speed and torque waveform of the
motor.
Lower the motor rotation speed or the
lower the servo gain by using the
function such as one-parameter tun-
ing.
The moment of inertia
ratio (Pn103) is larger
than the actual value or
greatly changes.
Check the moment of inertia ratio.
Set an appropriate value for the
moment of inertia (Pn103).