Yaskawa Sigma-5 User Manual: Design and Maintenance - Rotary Motors User Manual
Page 273
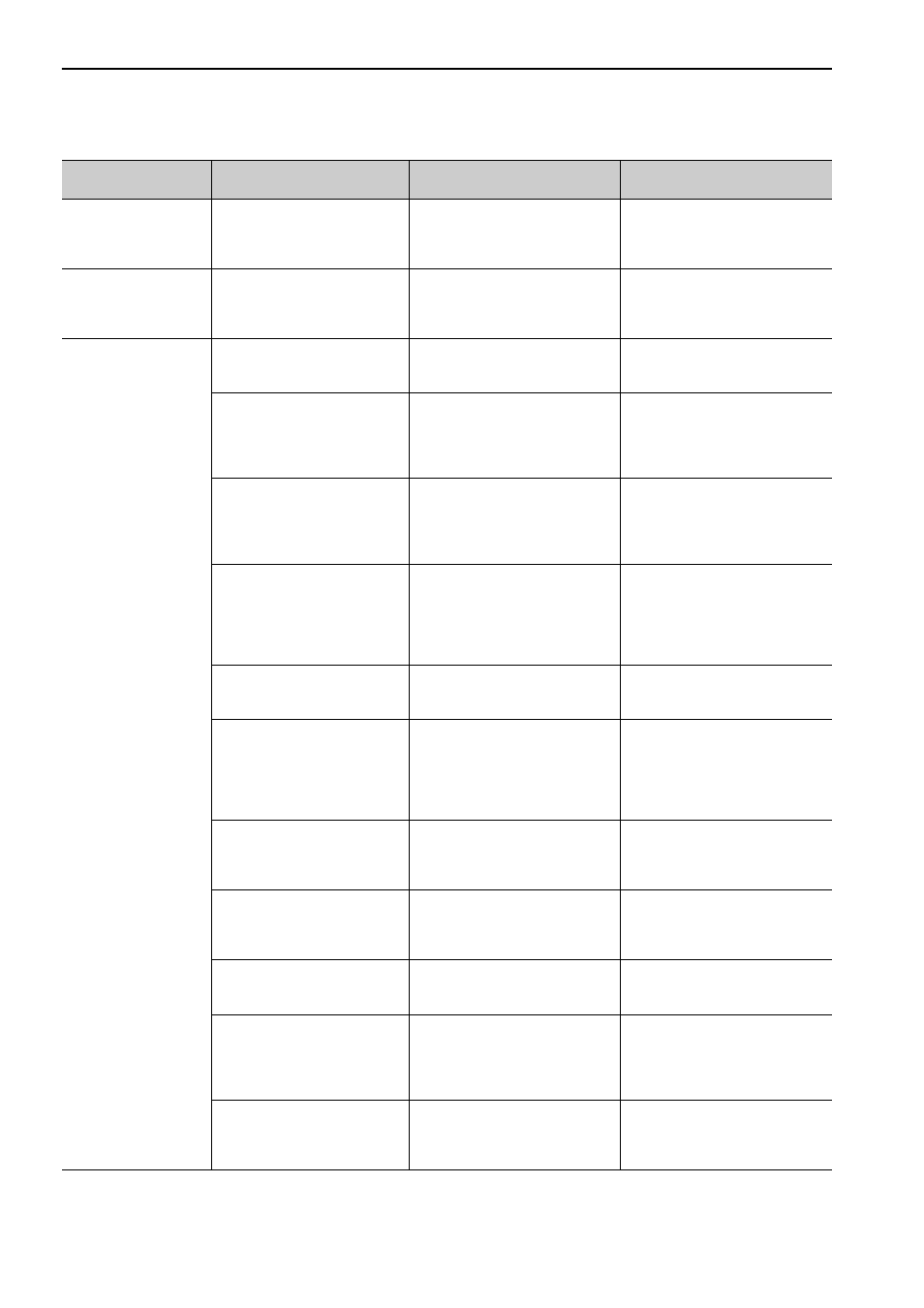
9 Troubleshooting
9.1.2 Troubleshooting of Alarms
9-8
A.051:
Unsupported Device
Alarm
An unsupported serial converter
unit, serial encoder, or external
encoder is connected to the SER-
VOPACK.
Check the product specifications.
Select the correct combination of
units.
A.0b0:
Cancelled Servo ON
Command Alarm
After executing the utility func-
tion to turn ON the power to the
motor, the Servo ON command
was sent from the host controller.
−
Turn the SERVOPACK power sup-
ply OFF and then ON again or per-
form a software reset.
A.100:
Overcurrent or Heat
Sink Overheated
(An overcurrent flowed
through the IGBT or
heat sink of SERVO-
PACK overheated.)
Incorrect wiring or contact fault
of main circuit cable or motor
main circuit cable.
Check the wiring. Refer to 3.1
Main Circuit Wiring.
Correct the wiring.
Short-circuit or ground fault of
main circuit cable or motor main
circuit cable.
Check for short-circuits across the
servomotor terminal phase-U, -V,
and -W, or between the grounding
and servomotor terminal U, V, or W.
Refer to 3.1 Main Circuit Wiring.
Some cables may be damaged.
Replace damaged cables.
Short-circuit or ground fault
inside the servomotor.
Check for short-circuits across the
servomotor terminal phase-U, -V,
and -W, or between the grounding
and servomotor terminal U, V, or W.
Refer to 3.1 Main Circuit Wiring.
The servomotor may be faulty.
Replace the servomotor.
Short-circuit or ground fault
inside the SERVOPACK.
Check for short-circuits across the
servomotor connection terminals U,
V, and W on the SERVOPACK, or
between the grounding and terminal
U, V, or W. Refer to 3.1 Main Cir-
cuit Wiring.
The SERVOPACK may be faulty.
Replace the SERVOPACK.
Incorrect wiring or contact fault
of the regenerative resistor.
Check the wiring. Refer to 3.7
Regenerative Resistors Connec-
tions.
Correct the wiring.
The dynamic brake (DB: Emer-
gency stop executed from the
SERVOPACK) was frequently
activated, or the DB overload
alarm occurred.
Check the resistor power consump-
tion monitor Un00B to see how
many times the DB has been used.
Or, check the alarm trace back mon-
itor Fn000 to see if the DB overload
alarm A.730 or A.731 was reported.
Change the SERVOPACK model,
operation conditions, or the mecha-
nism so that the DB does not need
to be used so frequently.
The generated regenerative
energy exceeded the SERVO-
PACK regenerative energy pro-
cessing capacity.
Check the regenerative load ratio
monitor Un00A to see how many
times the regenerative resistor has
been used.
Check the operation condition
including overload, and reconsider
the regenerative resistor value.
The SERVOPACK regenerative
resistance is too small.
Check the regenerative load ratio
monitor Un00A to see how many
times the regenerative resistor has
been used.
Change the regenerative resistance
value to a value larger than the
SERVOPACK minimum allowable
resistance value.
A heavy load was applied while
the servomotor was stopped or
running at low-speed.
Check to see if the operating condi-
tions are outside servo drive specifi-
cations.
Reduce the load applied to the ser-
vomotor or increase the operation
speed.
Malfunction caused by noise
interference.
Improve the wiring or installation
environment, such as by reducing
noise, and check to see if the alarm
recurs.
Take countermeasures for noise,
such as correct wiring of the FG.
Use an FG wire size equivalent to
the SERVOPACK main circuit wire
size.
A SERVOPACK fault occurred.
−
Turn the power supply OFF and
then ON again. If the alarm still
occurs, the SERVOPACK may be
faulty. Replace the SERVOPACK.
(cont’d)
Alarm:
Alarm Name
Cause
Investigative Actions
Corrective Actions