15 ) bit 12: servo driver command timeout error – Yaskawa MP2000 Series: Built-in SVB or SVB-01 Motion Module User Manual
Page 481
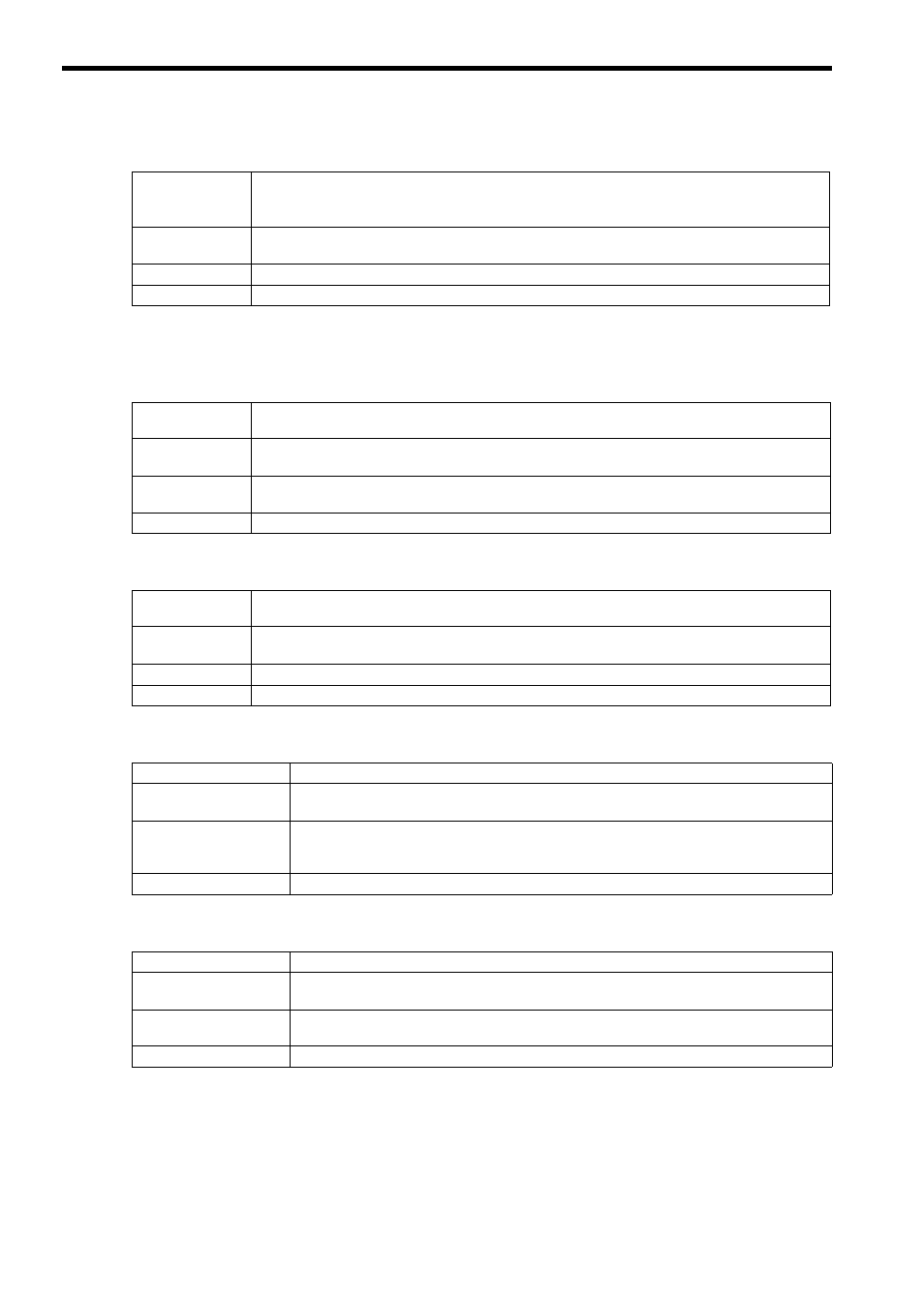
12.5 Troubleshooting Motion Errors
12.5.2 Motion Error Details and Corrections
12-38
( 15 ) Bit 12: Servo Driver Command Timeout Error
The above error occurs when Module allocations of SERVOPACK for MECHATROLINK communication have been
completed and the power is not being supplied to the SERVOPACK.
( 16 ) Bit 13: Excessive ABS Encoder Rotations
( 17 ) Bit 1D: Detected Servo Driver Type Error
( 18 ) Bit 1E: Motor Type Set Error
( 19 ) Bit 1F: Connected Encoder Type Error
Detection Timing
• Detected during execution of each motion commands.
• Detected by the MECHATROLINK communication control section when the Servo command responses
are checked for each process.
Processing when
Alarm Occurs
• The current command will be aborted.
Error and Cause
• The MECHATROLINK Servo command did not complete within the specified time (5 s).
Correction
• Check for alarms in the SERVOPACK for MECHATROLINK communication.
Detection Timing
• Enabled only when an absolute encoder is used for a finite length axis, and the electronic gear used.
Detected by the position management section when power is turned ON.
Processing when
Alarm Occurs
• The absolute position information read from the absolute encoder when the SEN signal turned ON is
ignored.
Error and Cause
• An operation error occurred when the absolute position information read from the absolute encoder is con-
verted from pulses to reference units at power ON.
Correction
• Check the gear ratio, number of encoder pulses for other motion fixed parameters.
Detection Timing
• Detected by the communication control section when communications with the SERVOPACK are estab-
lished.
Processing when
Alarm Occurs
• None
Error and Cause
• The models set in link allocation do not match the models actually connected.
Correction
• Correct the allocation to agree with the models actually connected.
Detection Timing
• Detected when communications with the SERVOPACK are established.
Processing when Alarm
Occurs
• None
Error and Cause
• The motor type setting (rotary/linear) of the Machine Controller fixed parameter does not agree
with that of SERVOPACK parameter (Start Selection Pn000.3 for SGDH, Rotary/Linear for
SGDS).
Correction
• Check the setting and model of the SERVOPACK.
Detection Timing
• Detected when communications with the SERVOPACK are established.
Processing when Alarm
Occurs
• None
Error and Cause
• The motor type setting (rotary/linear) of the Machine Controller fixed parameter does not agree
with the motor type connected to the SERVOPACK.
Correction
• Check the motor.