Yaskawa SGDH Linear Sigma Series User Manual
Page 102
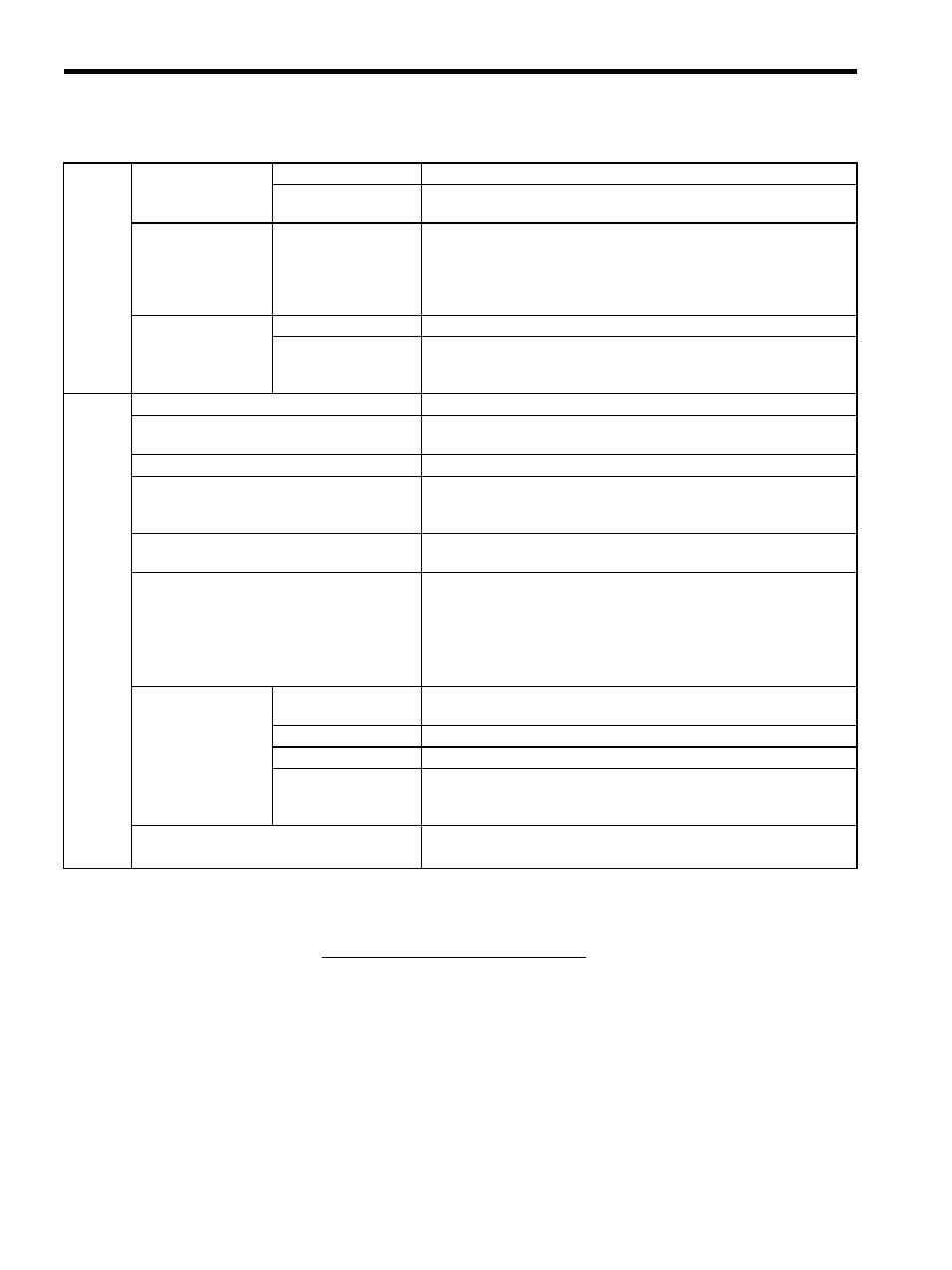
4 SERVOPACK Specifications and Dimensional Drawings
4.1.3 SERVOPACK Ratings and Specifications
4-4
* 1. Use the SERVOPACK within the ambient temperature range. When enclosed in a control panel,
internal temperatures must not exceed the ambient temperature range.
* 2. Speed regulation is defined as follows:
The motor speed may change due to voltage variations or amplifier drift and changes in processing
resistance due to temperature variation. The ratio of speed changes to the rated speed represent speed
regulation due to voltage and temperature variations.
* 3. The forward direction indicates the direction in which the linear scale counts up (Phase-A advance).
* 4. The built-in open collector power supply is not electrically insulated from the control circuit in the
SERVOPACK.
* 5. The DC reactor connection terminals for power supplies designed for minimum harmonics are not
included in SERVOPACKs with capacities of 7.5 kW.
I/O
Signals
Position Output
Form
Phase-A, -B, -C line driver
Frequency Dividing
Ratio
Any
Sequence Input
Signal allocation can
be modified.
Servo ON, P control (or Control mode switching, forward/reverse motor
movement by internal speed setting, zero clamping, reference pulse pro-
hibited), forward run prohibited (P-OT), reverse run prohibited (N-OT),
alarm reset, forward current limit, and reverse current limit (or internal
speed selection)
Sequence Output
Fixed Output
Servo alarm, 3-bit alarm codes
Signal allocation can
be modified.
Positioning completed (speed coincidence), during servomotor move-
ment, servo ready, during current limiting, during speed limiting, brake
released, warning, selecting three of the NEAR signals.
Internal
Func-
tions
Dynamic Brake
Operated at main power OFF, servo alarm, servo OFF or overtravel.
Overtravel Stop
Dynamic brake stop at P-OT or N-OT, deceleration to a stop, or coast to a
stop
Electronic Gear
0.01
≤ B/A ≤ 100
Protection
Overcurrent, overvoltage, low voltage, overload, regeneration error, main
circuit detection section error, heat sink overheated, no power supply,
overflow, overspeed, encoder error, overrun, CPU error, parameter error.
LED Display
Charge, Power, five 7-segment LEDs (built-in Digital Operator func-
tions)
CN5 Analog Monitoring
Analog monitor connector built in for monitoring speed, force and other
reference signals.
Speed: 1 V/1000 mm/s
Force: 1 V/100% of rated force
Position error pulses: 0.05 V/1 reference units or 0.05 V/100 reference
units
Communications
Connected Devices
Digital Operator (hand-held model), RS-422A port such as for a personal
computer (RS-232C ports under certain conditions)
1:N Communications
Up to N = 14 for RS-422A ports
Axis Address Setting
Set with parameters.
Functions
Status display, parameter setting, monitor display, alarm trace-back dis-
play, JOG and autotuning operations, speed, force reference signal and
other drawing functions.
Others
Reverse movement connection, zero-point search, automatic servomotor
ID, DC reactor connection terminal for harmonic suppressions.
∗5
(cont’d)
Speed reguration
=
No-load motor speed – Total load motor speed
Rated motor speed
× 100%