7) setting force limit – Yaskawa SGDH Linear Sigma Series User Manual
Page 255
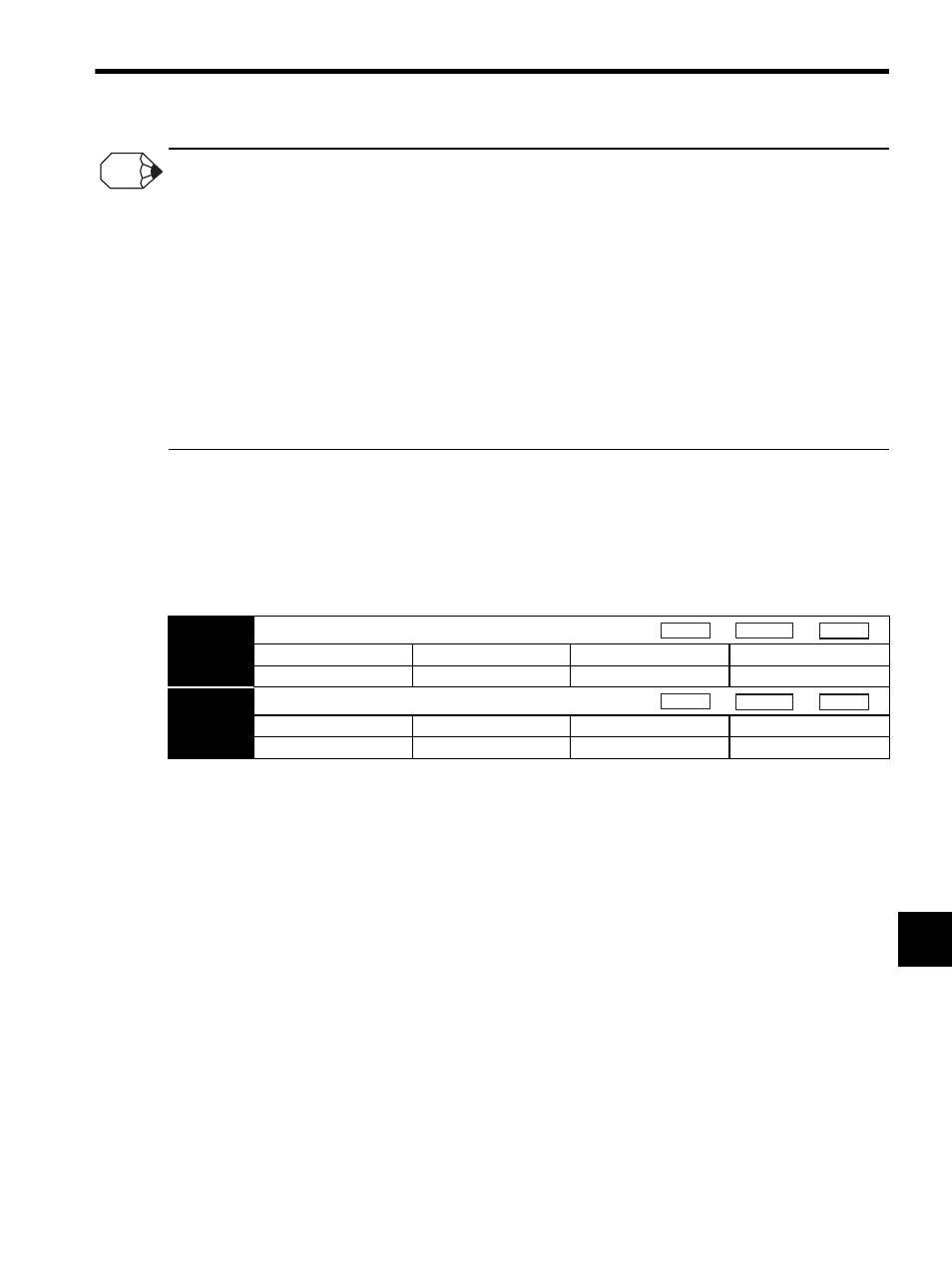
9.2 Trial Operation Using SERVOPACK Internal References
9-11
9
Unsuccessful Trial Operations
An unsuccessful trial operation could be attributed to the following conditions. Check the conditions and take appropriate
measures.
• The load is too heavy, or the jog speed is too fast, resulting in force reference saturation.
Set the force limit referring to (7) Setting Force Limit. If the force reference remains saturated, lighten the load or lower
the jog speed.
• The linear servomotor is moving slightly and then stops.
The linear servomotor, hall sensor, and linear scale are out of alignment. Check the wiring, scale pitch setting, linear
scale count, and whether the motor forward direction matches the scale countup direction.
• The alarm A.C2 (phase error detection) occurs when the linear servomotor moves.
The count direction of the linear scale signal is not correct, or the count may not be normal. Perform (5) Checking the
Feedback Signal again.
• If the count is normal, the malfunction may be caused by noise. Check the wiring and ground conditions of the SERVO-
PACK, serial converter unit, and linear servomotor.
(7) Setting Force Limit
To prevent danger during setup of the linear servomotor, the factory settings for the forward force limit
(Pn483) and reverse force limit (Pn484) parameters are set to small value (factory setting: 30%).
When the linear servomotor moves normally in jog operation mode, increase the value set for parameters
Pn483 and Pn484 to the force required. Set the value to the maximum value if no particular restricting condi-
tions apply.
INFO
Pn483
Forward Force Limit
Setting Range
Setting Unit
Factory Setting
Setting Validation
0 to 800 %
1 %
30 %
Immediately
Pn484
Reverse Force Limit
Setting Range
Setting Unit
Factory Setting
Setting Validation
0 to 800 %
1 %
30 %
Immediately
Speed
Position
Force
Speed
Position
Force