5 using the mode switch (p/pi switching), 5 using the mode switch (p/pi switching) -19, 1) selecting the mode switch setting – Yaskawa SGDH Linear Sigma Series User Manual
Page 341
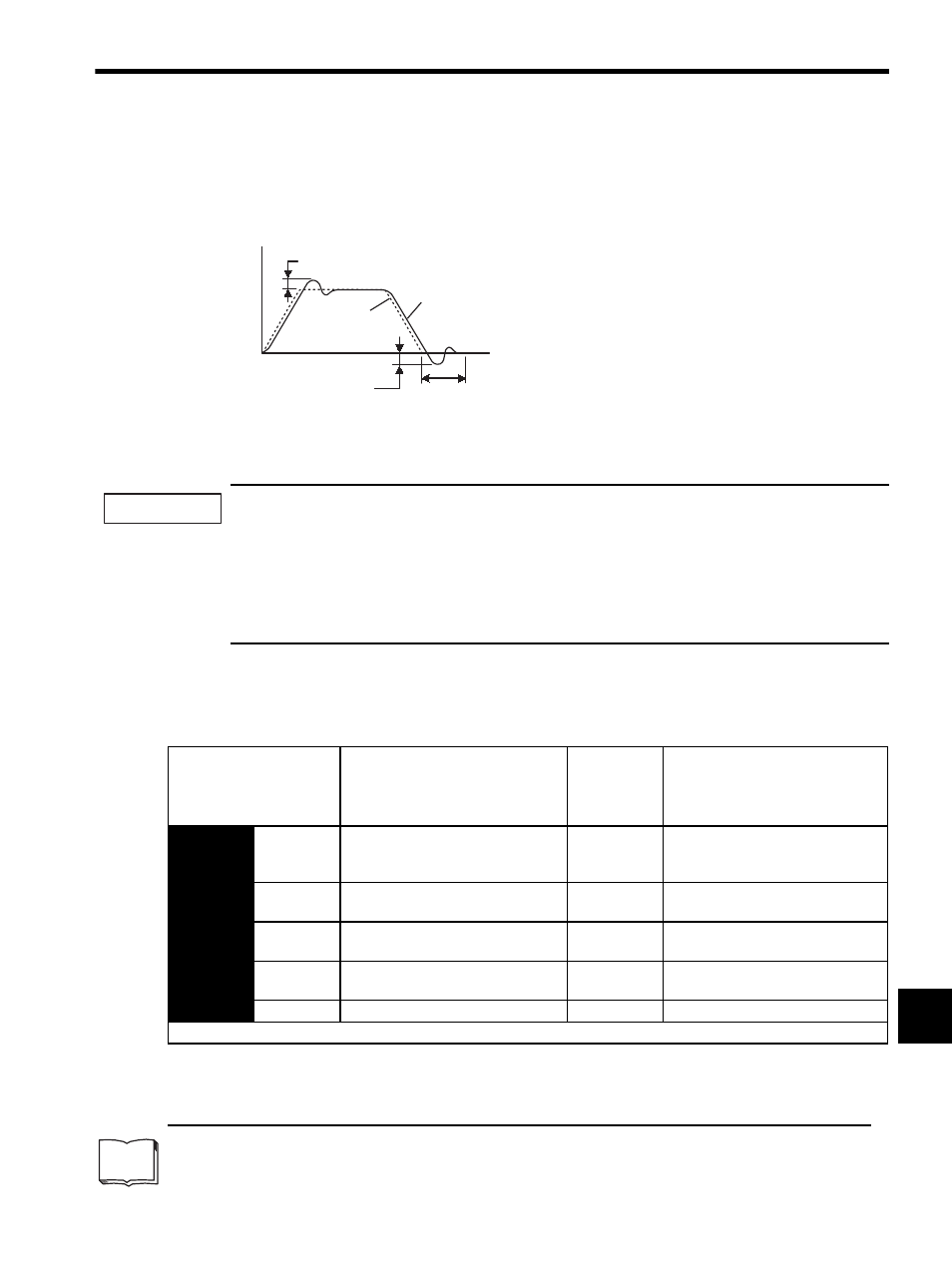
10.4 Servo Gain Adjustment Functions
10-19
10
10.4.5 Using the Mode Switch (P/PI Switching)
Use the mode switch (P/PI switching) function in the following cases:
• To suppress overshooting during acceleration or deceleration (for speed control)
• To suppress undershooting during positioning and reduce the settling time (for position control)
The mode switch function automatically switches the speed control mode from PI control mode to P control
1
mode based on a comparison between the servo’s internal value and a user-set detection level.
1. The mode switch function is used in very high-speed positioning when it is necessary to use the servo-
drive near the limits of its capabilities. The speed response waveform must be observed to adjust the
mode switch.
2. For normal use, the speed loop gain and position loop gain set by autotuning provide sufficient speed/
position control. Even if overshooting or undershooting occur, they can be suppressed by setting the host
controller’s acceleration/deceleration time constant, the SERVOPACK’s Soft Start Acceleration/Deceler-
ation Time (Pn305, Pn306), or Position Reference Acceleration/Deceleration Time Constant (Pn204).
(1) Selecting the Mode Switch Setting
The SERVOPACK provides the following four mode switch settings (0 to 3). Select the appropriate mode switch
setting with parameter Pn10B.0.
1
From PI control to P control
PI control means proportional/integral control and P control means proportional control. In short, switching “from PI
control to P control” reduces effective servo gain, making the SERVOPACK more stable.
Actual motor operation
Overshoot
Speed
Reference
Settling time
Time
Undershoot
TERMS
IMPORTANT
Parameter
Mode Switch Selection
Parameter
Containing
Detection
Point Setting
Setting Unit
Pn10B
n.0
Use a force reference level for detec-
tion point.
(Factory Setting)
Pn10C
Percentage to the rated force
n.1
Use a speed reference level for
detection point.
Pn181
Servomotor speed: mm/s
n.2
Use an acceleration level for detec-
tion point.
Pn182
Servomotor acceleration: 10 mm/s
2
n.3
Use a position error pulse for detec-
tion point.
Pn10F
Reference unit
n.4
Do not use the mode switch function.
−
−
Select a condition to execute the mode switch (P/PI switching). (Setting is validated immediately.)