10 ) position information 1 – Yaskawa JAPMC-MC2300 User Manual
Page 120
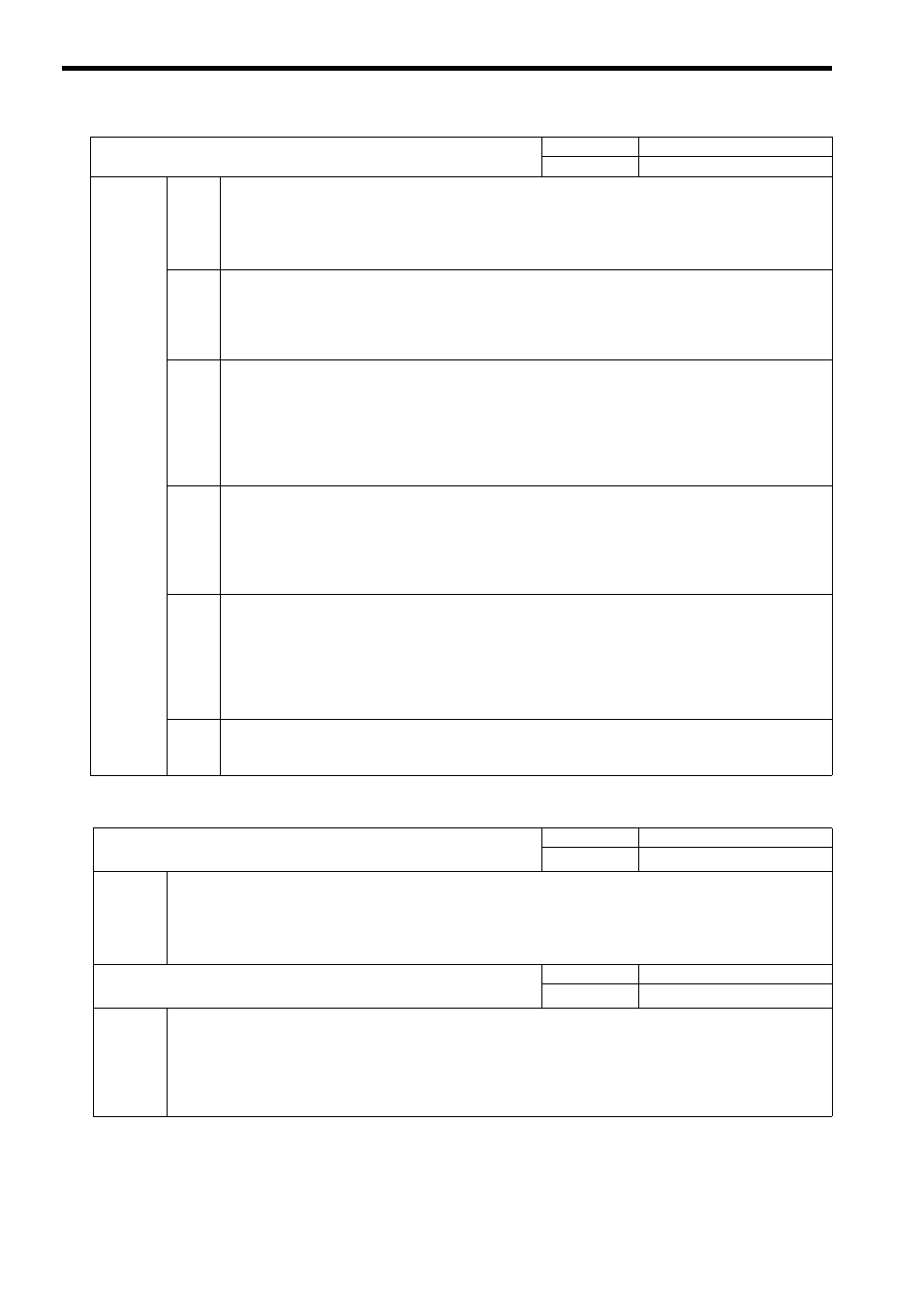
5.4 MP2000 Series Machine Controller Parameter Details
5.4.3 Motion Monitoring Parameter Details
5-48
( 10 ) Position Information 1
Description
Bit 5
Zero Point Return (Setting) Completed (ZRNC)
0: Zero point return (setting) not completed.
1: Zero point return (setting) completed.
This bit turns ON when a zero point return (setting) has been completed.
This bit turns OFF when a new zero point return (setting) operation is started.
Bit 6
During Machine Lock (MLKL)
0: Machine lock mode released.
1: Machine lock mode.
This bit turns ON when the Machine Lock bit is set to 1 in the Run Command Setting (setting parameter
OW
00, bit 1) and the axis has actually entered machine lock mode.
Bit 7
Absolute Position Read-out Completed
0: OFF
1: ON (Reading completed)
This bit turns ON when reading the absolute data by setting the setting parameter Absolute Position Reading
Demand (OW
00, bit 5) to 1 (reading ON) has been completed.
This bit stays OFF when the setting parameter Absolute Position Reading Demand (OW
00, bit 5) is set to 0
(reading OFF).
Bit 8
ABS Rotary Pos. LOAD Complete (ABSLDE)
0: LOAD not completed.
1: LOAD completed.
This bit turns ON when the Request ABS Rotary Pos. Load bit is set to 1 in the Run Command Setting (setting
parameter OW
00, bit 7) and loading of the information has been completed.
Invalid for linear type.
Bit 9
POSMAX Turn Preset Complete (TPRSE)
0: Preset not completed.
1: Preset completed.
This bit turns ON when the POSMAX Turn Number Presetting Demand bit in the Run Command Setting (set-
ting parameter OW
00, bit 6) is set to 1 and the POSMAX Number of Turns has been preset with the Num-
ber of POSMAX Turns Presetting Data (setting parameter OL
4C).
Invalid for linear type.
Bit A
ABS Encoder Rotating Direction
0: Forward rotation
1: Reverse rotation
IL
0E
Target Position in Machine Coordinate System (TPOS)
Range
Unit
−2
31
to 2
31
−1
Reference unit
Description
Stores the target position in the machine coordinate system managed by the Motion Module.
This is the target position per scan for INTERPOLATE or LATCH commands.
• This parameter will be set to 0 when the power supply is turned ON.
• The data is refreshed even when the machine lock mode is enabled.
• This parameter will not be reset even when an infinite length axis type is selected.
IL
10
Calculated Position in Machine Coordinate System (CPOS)
Range
Unit
−2
31
to 2
31
−1
Reference unit
Description
Stores the calculated position in the machine coordinate system managed by the Motion Module.
The position data stored in this parameter is the target position for each scan.
• This parameter will be set to 0 when the power supply is turned ON.
• The data is updated even when the machine lock mode is enabled.
• When an infinite length axis type is selected, a range of 0 to (Maximum Value of Rotary Counter (POSMAX)
− 1) is
stored.
IW
0C
Position Management Status (cont’d)
Range
Unit
−
−