7 ) bit 9: excessive deviation – Yaskawa JAPMC-MC2300 User Manual
Page 350
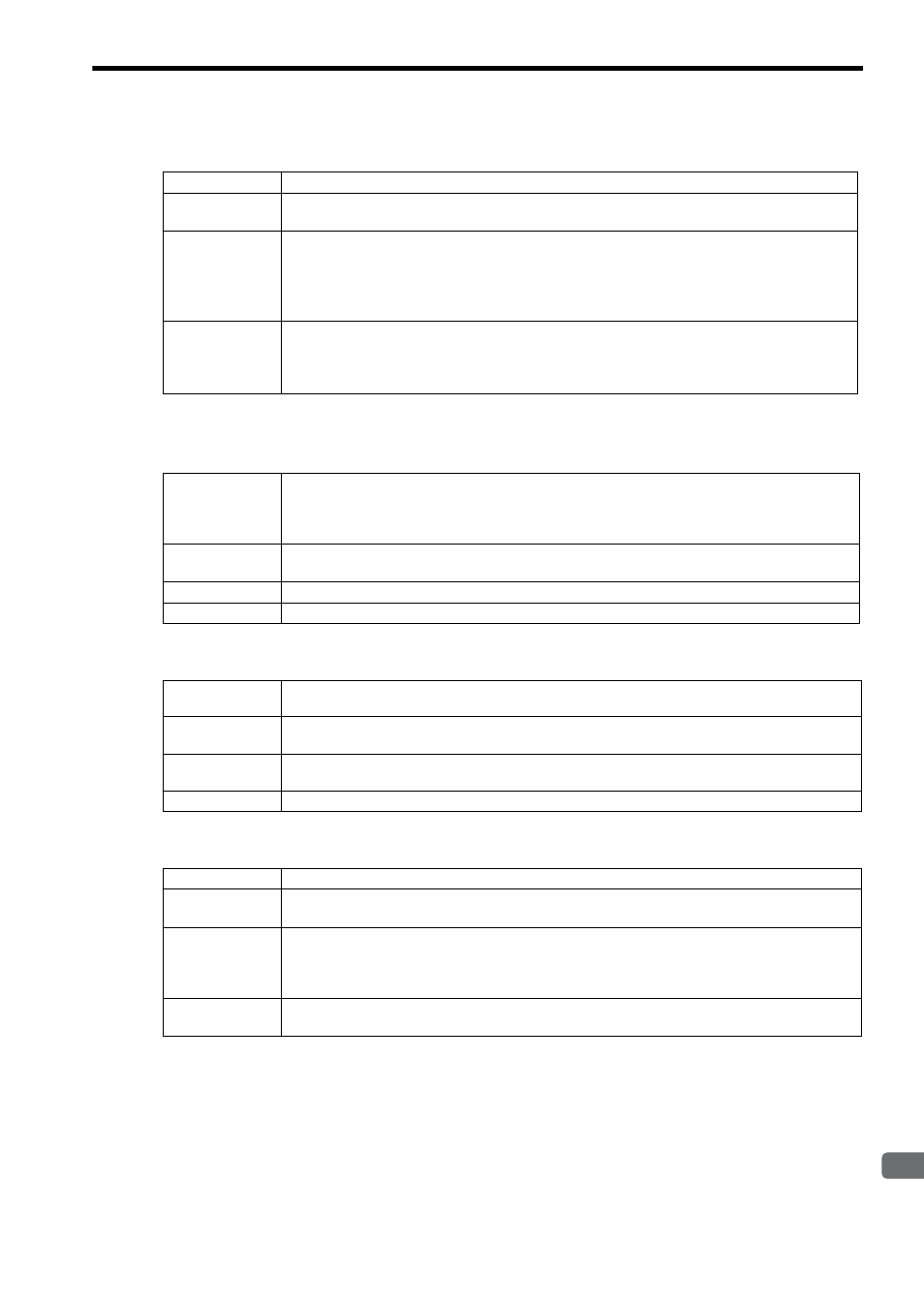
12.4 Troubleshooting Motion Errors
12.4.2 Axis Alarm Details and Corrections
12-31
12
Troubleshooting
( 7 ) Bit 9: Excessive Deviation
The above check is not performed if the Error Count Alarm Detection (OL
22) is set to 0.
( 8 ) Bit D: Zero Point Unsetting
( 9 ) Bit 13: Excessive ABS (Absolute) Encoder Rotations
( 10 ) Bit 14: PG Disconnection Error
Detection Timing
• Always, except during speed control and torque control
Processing when
Alarm Occurs
• The move command is not executed.
• The Command Error Completed Status in the Motion Command Status (IW
09, bit 3) will turn ON.
Error and Cause
One of the following is possible.
• The position loop gain and speed loop gain are not set correctly, creating poor response.
• The Error Count Alarm Detection (OL
22) is too small.
• The capacity of the motor is insufficient for the machine load.
• SERVOPACK failure
Correction
Check the following and correct the problem. If the problem persists, contact the maintenance department.
• Check the position loop gain and speed loop gain.
• Check the Error Count Alarm Detection (OL
22).
• Check the motor capacity.
Detection Timing
• Enabled only when an absolute encoder is used for an infinite length axis and detected when the next com-
mand is set in the Motion Command (OW
08).
Commands: Positioning, External Positioning, Interpolation, Interpolation with position detection
function, Phase reference
Processing when
Alarm Occurs
• The set command will not be executed.
• The Command Error Completed Status in the Motion Command Status (IW
09, bit 3) will turn ON.
Error and Cause
• A move command was set without executing the ZSET command (IW
0C, bit 5 is OFF).
Correction
• After clearing the motion command and resetting the alarm, execute a Zero Point Setting operation.
Detection Timing
• Enabled only when an absolute encoder is used for a finite length axis, and the electronic gear is used.
Detected by the position management section when power is turned ON.
Processing when
Alarm Occurs
• The absolute position information read from the absolute encoder when the SEN signal turned ON is
ignored.
Error and Cause
• An operation error occurred when the absolute position information read from the absolute encoder is con-
verted from pulses to reference units at power ON.
Correction
• Check the gear ratio, number of encoder pulses for other motion fixed parameters.
Detection Timing
• Any time
Processing when
Alarm Occurs
• The command in execution is forcibly terminated.
• The Command Error Completed Status in the Motion Command Status (IW
09, bit 3) will turn ON.
Error and Cause
One of the following is possible.
• Any of the following pulse input signals are incorrectly connected or disconnected.
PA (pin No. 3), PAL (pin No. 4), PB (pin No. 23), PBL (pin No. 24)
• The SERVOPACK control power supply is OFF.
Correction
• Check the pulse input signal connections to see if they are correctly connected.
• Check the SERVOPACK control power supply.