Yaskawa Sigma II Series DC Power Input SGMAJ User Manual
Page 288
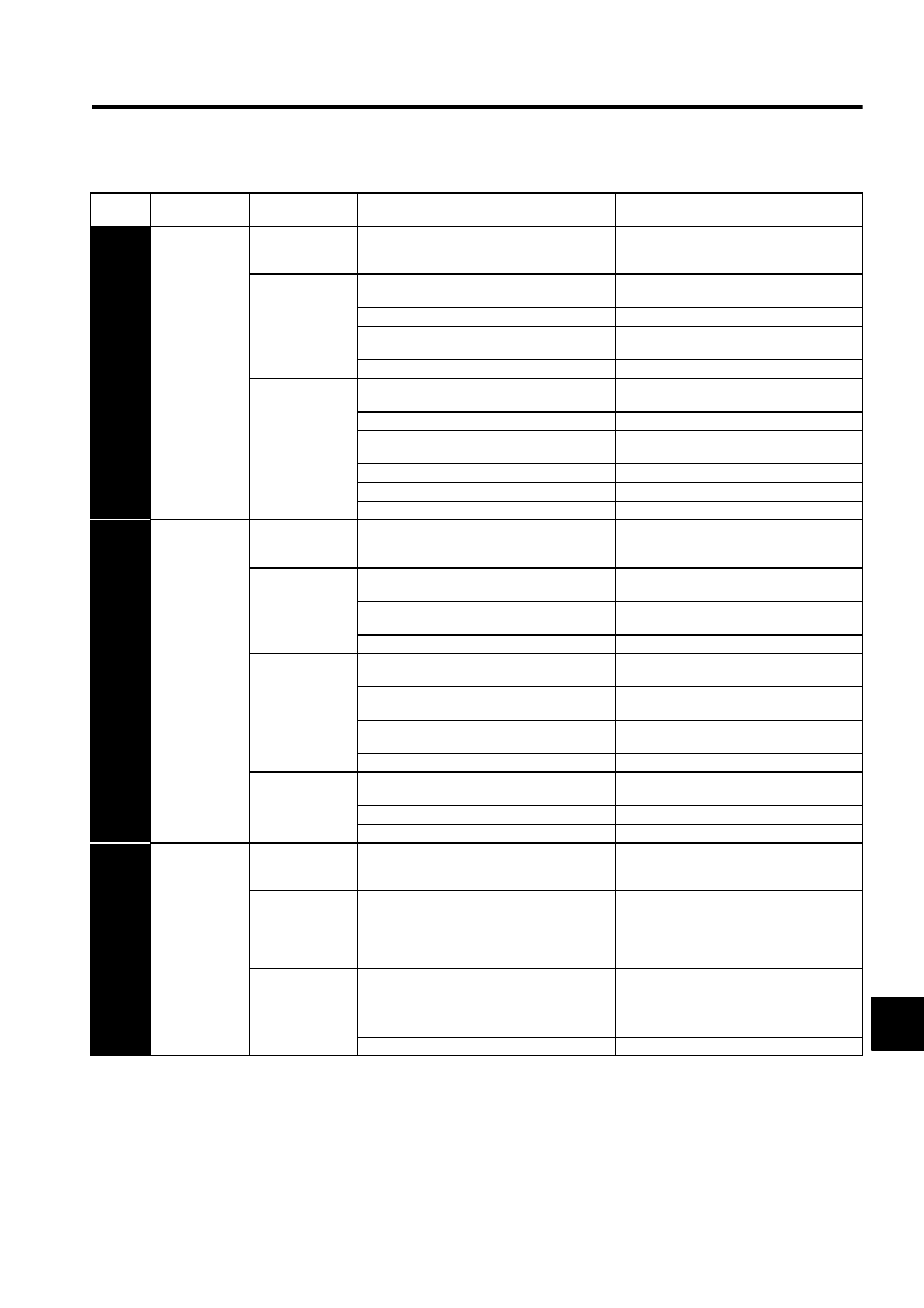
10.1 Troubleshooting
10-7
10
A.51
Overspeed
(Detected when
the feedback
speed is the max-
imum motor
speed
Occurred when the
control power sup-
ply was turned ON.
A SERVOPACK board fault occurred.
Replace the SERVOPACK.
Occurred when
servo was ON.
The order of phases U, V, and W in the servomotor
wiring is incorrect.
Correct the servomotor wiring.
The encoder wiring is incorrect.
Correct the encoder wiring.
Malfunction occurred due to noise interference in
the encoder wiring.
Take measures against noise for the encoder wir-
ing.
A SERVOPACK fault occurred.
Replace the SERVOPACK.
Occurred when the
servomotor started
running or in a
high-speed rotation.
The order of phases U, V, and W in the servomotor
wiring is incorrect.
Correct the servomotor wiring.
The encoder wiring is incorrect.
Correct the encoder wiring.
Malfunction occurred due to noise interference in
the encoder wiring.
Take measures against noise for the encoder wir-
ing.
The position or speed reference input is too large.
Reduce the reference value.
The setting of the reference input gain is incorrect.
Correct the reference input gain setting.
A SERVOPACK board fault occurred.
Replace the SERVOPACK.
A.71
A.72
A.71: High Load
A.72: Low Load
Occurred when the
control power sup-
ply was turned ON.
A SERVOPACK board fault occurred.
Replace the SERVOPACK.
Occurred when the
servo was ON.
The servomotor wiring is incorrect or the connection
is faulty.
Correct the servomotor wiring.
The encoder wiring is incorrect or the connection is
faulty.
Correct the encoder wiring.
A SERVOPACK fault occurred.
Replace the SERVOPACK.
Occurred when the
servomotor did not
run by the refer-
ence input.
The servomotor wiring is incorrect or the connection
is faulty.
Correct the servomotor wiring.
The encoder wiring is incorrect or the connection is
faulty.
Correct the encoder wiring.
The starting torque exceeds the maximum torque.
Reconsider the load and operation conditions, or
reconsider the servomotor capacity.
A SERVOPACK fault occurred.
Replace the SERVOPACK.
Occurred during
normal operation.
The actual torque exceeds the rated torque or the
starting torque largely exceeds the rated torque.
Reconsider the load and operation conditions, or
reconsider the servomotor capacity.
Temperature in the SERVOPACK panel is high.
Reduce the in-panel temperature to 40
°C or less.
A SERVOPACK fault occurred.
Replace the SERVOPACK.
A.73
Dynamic Brake
Overload
Occurred when the
control power sup-
ply was turned ON.
A SERVOPACK board fault occurred.
Replace the SERVOPACK.
Occurred when the
servomotor was
running and in a sta-
tus other than servo
OFF.
A SERVOPACK board fault occurred.
Replace the SERVOPACK.
Occurred when the
servomotor was
running in servo
OFF status.
The rotating energy at a DB stop exceeds the DB
resistance capacity.
cReduce the motor speed,
dReduce the load moment of inertia, or
eReduce the number of times of the DB stop
operation.
A SERVOPACK fault occurred.
Replace the SERVOPACK.
Table 10.3 Alarm Display and Troubleshooting (cont’d)
Alarm
Display
Alarm Name
Situation at Alarm
Occurrence
Cause
Corrective Actions