2 list of servo adjustment functions, 1) autotuning functions, 2 list of servo adjustment functions -4 – Yaskawa SGDS Sigma III Servo Amplifier User Manual
Page 231
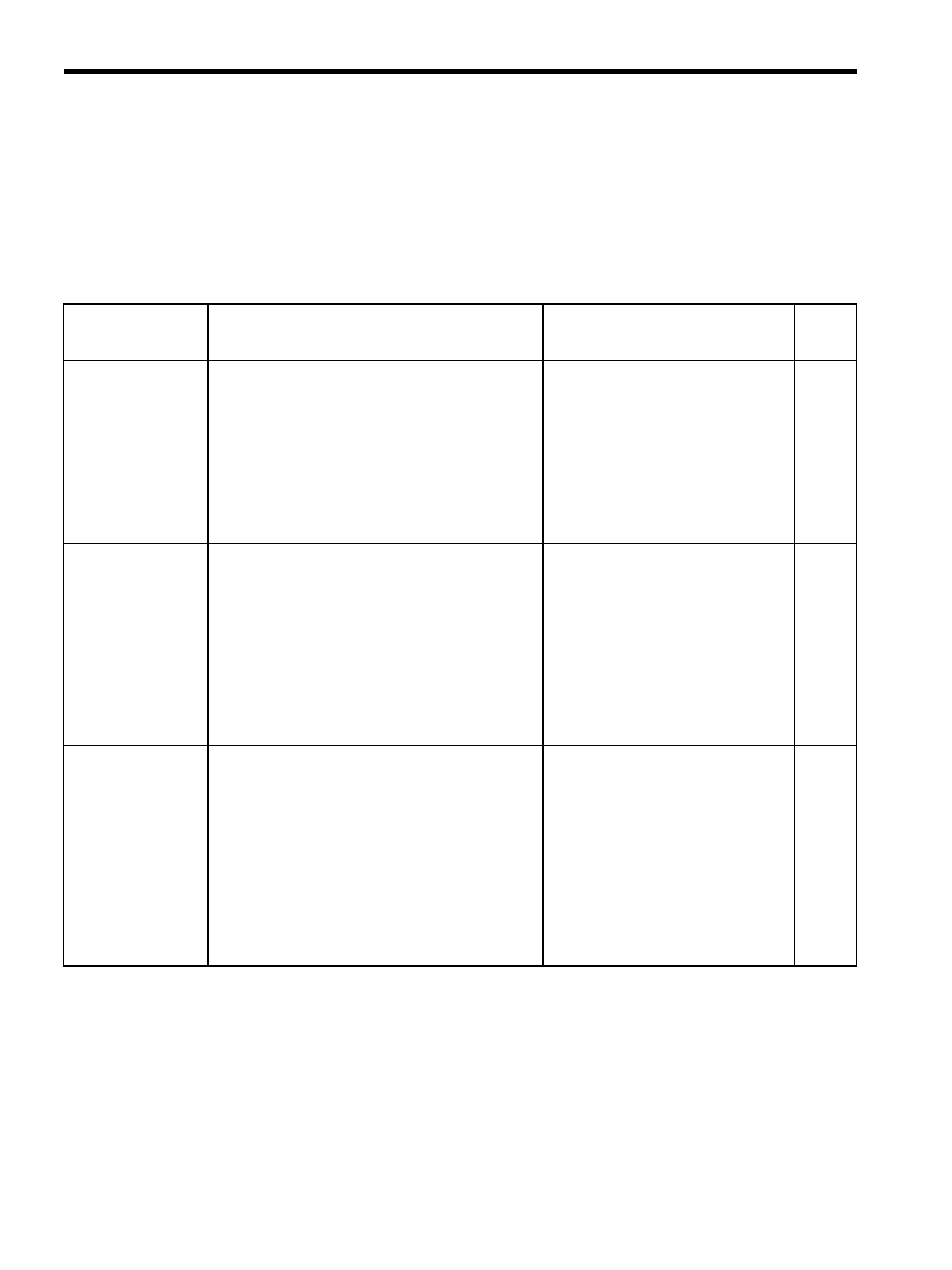
8 Adjustments
8.1.2 List of Servo Adjustment Functions
8-4
8.1.2 List of Servo Adjustment Functions
(1) Autotuning Functions
Autotuning calculates the load moment of inertia, which determines the servo drive responsiveness, and
automatically adjusts parameters, such as the Speed Loop Gain Kv (Pn100), Speed Loop Integral Time Constant
Ti (Pn101), Position Loop Gain Kp (Pn102), 1st Step 1st Torque Reference Filter Time Constant (Pn401). Refer
to the following table to select the appropriate autotuning function for your desired purpose and adjust the servo
gains.
Function Name and
Related Parameters
Description
Guidelines for Selection
Refer-
ence
Section
Normal Autotuning
Pn110.0
Fn001
Fn007
A new algorithm is used to increase the calculation
accuracy of
Σ II autotuning calculation accuracy for the
load moment of inertia, increase stability, and eliminate
restrictions. Setting methods for the Machine Rigidity
Setting (Fn001) have been reviewed to make the
settings easier to use and provide more stable settings.
The load moment of inertia is calculated during
operation for a user reference, and the servo gains (Kv,
Ti, Kp, and Tf) are set according to the Machine
Rigidity Setting (Fn001).
Only the minimum number of parameters
must be set for autotuning using a normal
operation reference.
This is the most basic autotuning
function.
Advanced
Autotuning
Fn017
With advanced autotuning, the amounts that the gains
can be increased for the SERVOPACK are determined
automatically and a notch filter is automatically
adjusted while detecting vibration to find servo gains
suitable for the machine characteristics. This autotuning
function is performed using utility function Fn017.
Automatic round-trip operation is performed for the
specified pattern and the load moment of inertia, servo
gains (Kv, Ti, Kp, and Tf), and notch filter frequency
are automatically set.
Advanced autotuning is used to improve
characteristics when the results of normal
autotuning are unsuitable.
A motion stroke for the number of
positioning reference units to perform the
automatic operation must be confirmed
and parameters, such as the speed, must
be set.
High-performance servo gain settings
can be achieved by setting only the
automatic operation.
One-parameter
Autotuning
Fn01A
For one-parameter autotuning, the load moment of
inertia is not calculated and the four servo gains (Kv, Ti,
Kp, Tf) can be adjusted using a single parameter. This
autotuning function is made to assist adjustments, and it
is performed using utility function Fn01A.
During operation with a user reference, by changing
one parameter change and set the four servo gains
simultaneously. The four gains are set from the one
parameter to satisfy a stable relationship between them.
One-parameter autotuning is used when
the user wants to adjust the servo gains
while confirming the response of the
servo or machine.
One-parameter autotuning can be used to
eliminate the need to manually adjust
parameters while quickly obtaining safe
adjustments.
The user must observe the response
waveform on an external measuring
instrument and determine the results of
autotuning.