Yaskawa SGDS Sigma III Servo Amplifier User Manual
Page 306
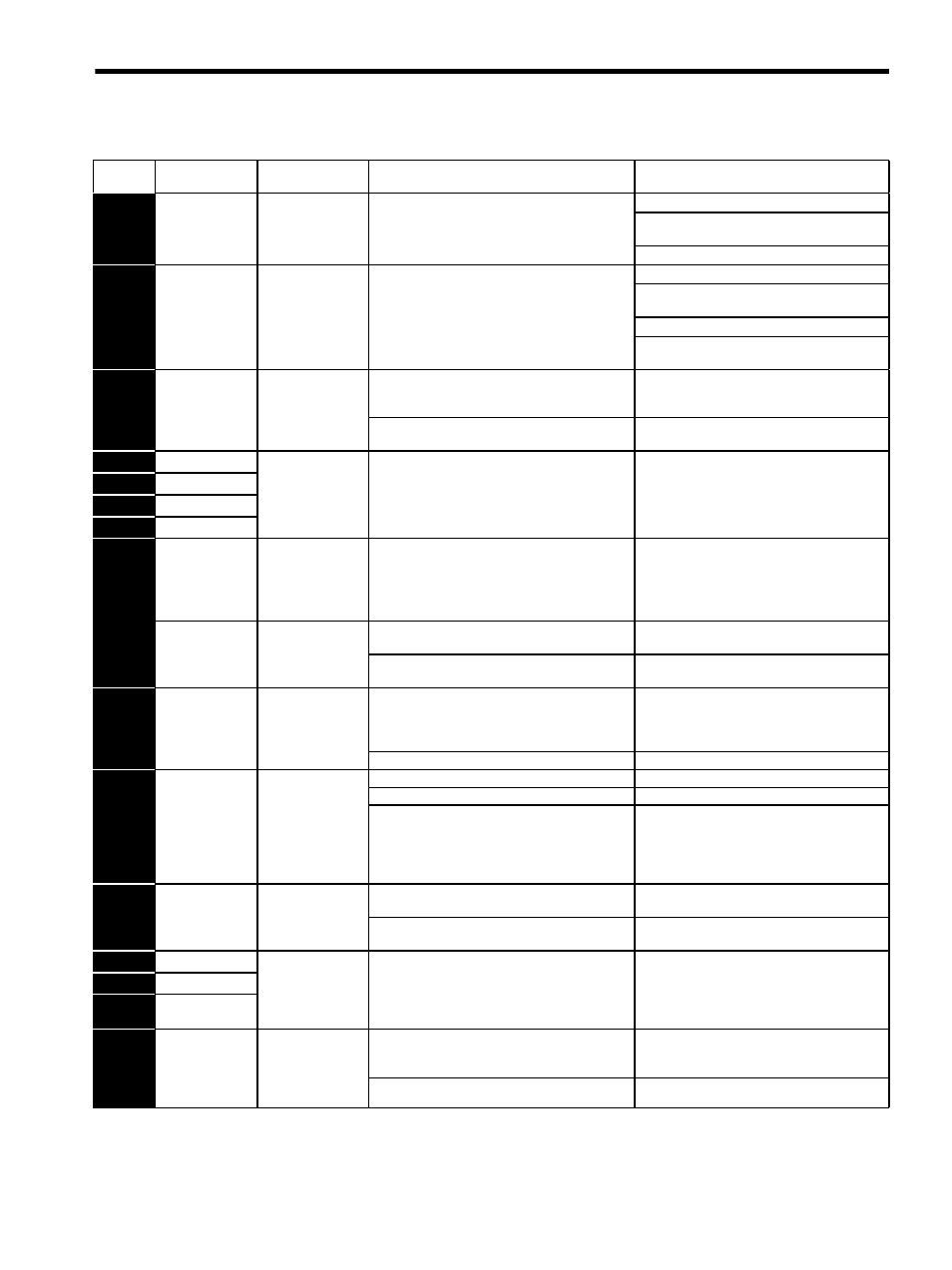
10.1 Troubleshooting
10-17
A.d01
Position Error
Pulse Overflow
Alarm at Servo
ON
Occurred when the
control power
supply was turned
ON.
• Excessive position errors accumulated while the
servo is OFF
• With the setting not to clear the errors while the
servo is OFF, the servomotor was running.
Do not run the servomotor in servo OFF status.
Make the setting so that the errors are cleared
while the servo is OFF.
Adjust the detection level.
A.d02
Position Error
Pulse Overflow
Alarm by
Speed Limit at
Servo ON
Occurred when the
servomotor was
running.
The servo turned ON with accumulated errors, and
reference pulse was input during operation at the
speed limit, therefore, the errors exceeded the
Position Error Pulse Overflow Alarm Level (Pn520).
Do not run the servomotor in servo OFF status.
Make the setting so that the errors are cleared
while the servo is OFF.
Correct the detection level.
Adjust the speed limit level (Pn529) when servo
turns ON.
A.d10
Motor-Load
Position Error
Pulse Overflow
Occurred when
servo was ON or
during operation.
Motor rotation direction and scale installation
direction is opposite.
Install the scale in the opposite direction, or
reverse the setting of fully-closed encoder usage
method (Pn002.3).
Position of the load such as stage and scale joint
installation are incorrect.
Check the mechanical joint.
A.E00
COM Alarm 0
Occurred when the
control power
supply was turned
ON.
A SERVOPACK fault occurred.
Replace the SERVOPACK.
A.E01
COM Alarm 1
A.E02
COM Alarm 2
A.E07
COM Alarm 7
A.E40
MECHATROLI
NK II
Transmission
Cycle Setting
Error
Occurred at
MECHATROLINK
II communications
start.
Setting of MECHATROLINK II transmission cycle
is out of specifications range.
Set the transmission cycle to proper value.
A.E50
MECHATROLI
NK II
Synchronizatio
n Error
Occurred during
MECHATROLINK
II communications.
WDT data of host controller was not updated
correctly.
Update the WDT data at the host controller
correctly.
A SERVOPACK fault occurred.
Replace the SERVOPACK.
A.E51
MECHATROLI
NK II
Synchronizatio
n Failed
Occurred at
MECHATROLINK
II synchronization
communications
start.
WDT data of host controller was not updated
correctly at the synchronization communications
start, and synchronization communications could not
start.
Update the WDT data at the host controller
correctly.
A SERVOPACK fault occurred.
Replace the SERVOPACK.
A.E60
MECHATROLI
NK II
Communicatio
ns Error
Occurred during
MECHATROLINK
II communications.
MECHATROLINK II wiring is incorrect.
Correct the MECHATROLINK II wiring.
A SERVOPACK fault occurred.
Replace the SERVOPACK.
MECHATROLINK II data reception error occurred
due to noise interference.
Take measures against noise. Check the
MECHATROLINK II communications cable and
FG wiring and take measures such as adding
ferrite core on the MECHATROLINK II
communications cable.
A.E61
MECHATROLI
NK II
Transmission
Cycle Error
Occurred during
MECHATROLINK
II
communications.
MECHATROLINK II transmission cycle fluctuated.
Remove the cause of transmission cycle
fluctuation at host controller.
A SERVOPACK fault occurred.
Replace the SERVOPACK.
A.EA0
DRV Alarm 0
Occurred when the
control power
supply was turned
ON or during
operation.
A SERVOPACK fault occurred.
Replace the SERVOPACK.
A.EA1
DRV Alarm 1
A.EA2
DRV Alarm 2
A.ED0
Internal
Command
Error
Occurred at
MECHATROLINK
II communications
start or during
operation.
Parameter was changed by the digital operator or the
personal computer during MECHATROLINK II
communications.
Stop changing parameter using digital operator
and do not connect the personal computer during
MECHATROLINK II communications.
A SERVOPACK fault occurred.
Replace the SERVOPACK.
Table 10.3 Alarm Display and Troubleshooting (Cont’d)
Alarm
Display
Alarm Name
Situation at Alarm
Occurrence
Cause
Corrective Actions