3 advanced autotuning, 1 advanced autotuning, 3 advanced autotuning -13 – Yaskawa SGDS Sigma III Servo Amplifier User Manual
Page 240: 1 advanced autotuning -13
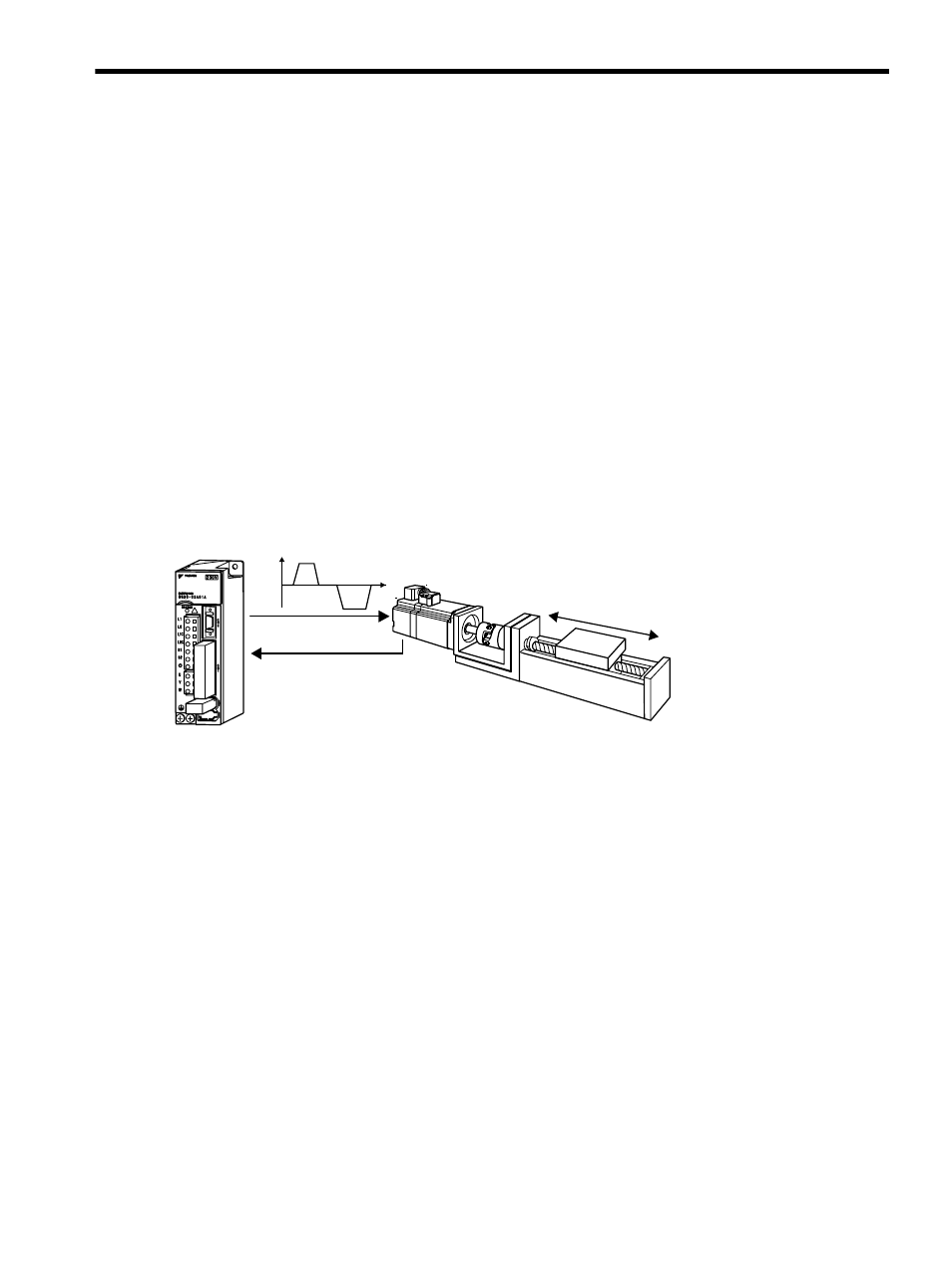
8.3 Advanced Autotuning
8-13
8.3 Advanced Autotuning
8.3.1 Advanced Autotuning
Advanced autotuning calculate the load moment of inertia and set the servo gain suitable for the machine
charateristics. The gain is set as high as possible to avoid the vibration. Advanced autotuning is performing
using utility function Fn017 (Advanced Autotuning). If vibration occurs during advanced autotuning, either set a
notch filter or lower the servo gains, depending on circumstances.
The following parameter settings are changed by the advanced autotuning.
• Speed loop gain (Pn100)
• Speed loop integral time constant (Pn101)
• Position loop gain (Pn102)
• 1st Step 1st torque reference filter time constant (Pn401)
• Moment of inertia ratio (Pn103)
The following parameter settings are changed if required.
• Torque related function switch (Pn408.0 or Pn408.2)
• 1st step notch filter frequency (Pn409)
• 2nd step notch filter frequency (Pn40C)
Advanced Autotuning Operation Example
Advanced autotuning may not be effective in the following cases.
• The load moment of inertia varies in less than 200 ms.
• The rotational speed is higher than 100 RPM or the speed uses a stepwise reference.
• Load rigidity is low and mechanical vibration occurs easily or viscous friction is high.
• The movement range is too narrow, e.g., only a few rotations.
• There is movement in only one direction.
• When P control operation (proportional control) is used.
If the desired operation is not achieved for advanced autotuning in the above conditions, calculate values from
machine specifications and set the load moment of inertia ratio in Pn103 and then perform one-parameter
autotuning or manual adjustment.
Movement distance
SERVOPACK
Movement
speed
Reference
Response