Yaskawa SGDS Sigma III Servo Amplifier User Manual
Page 312
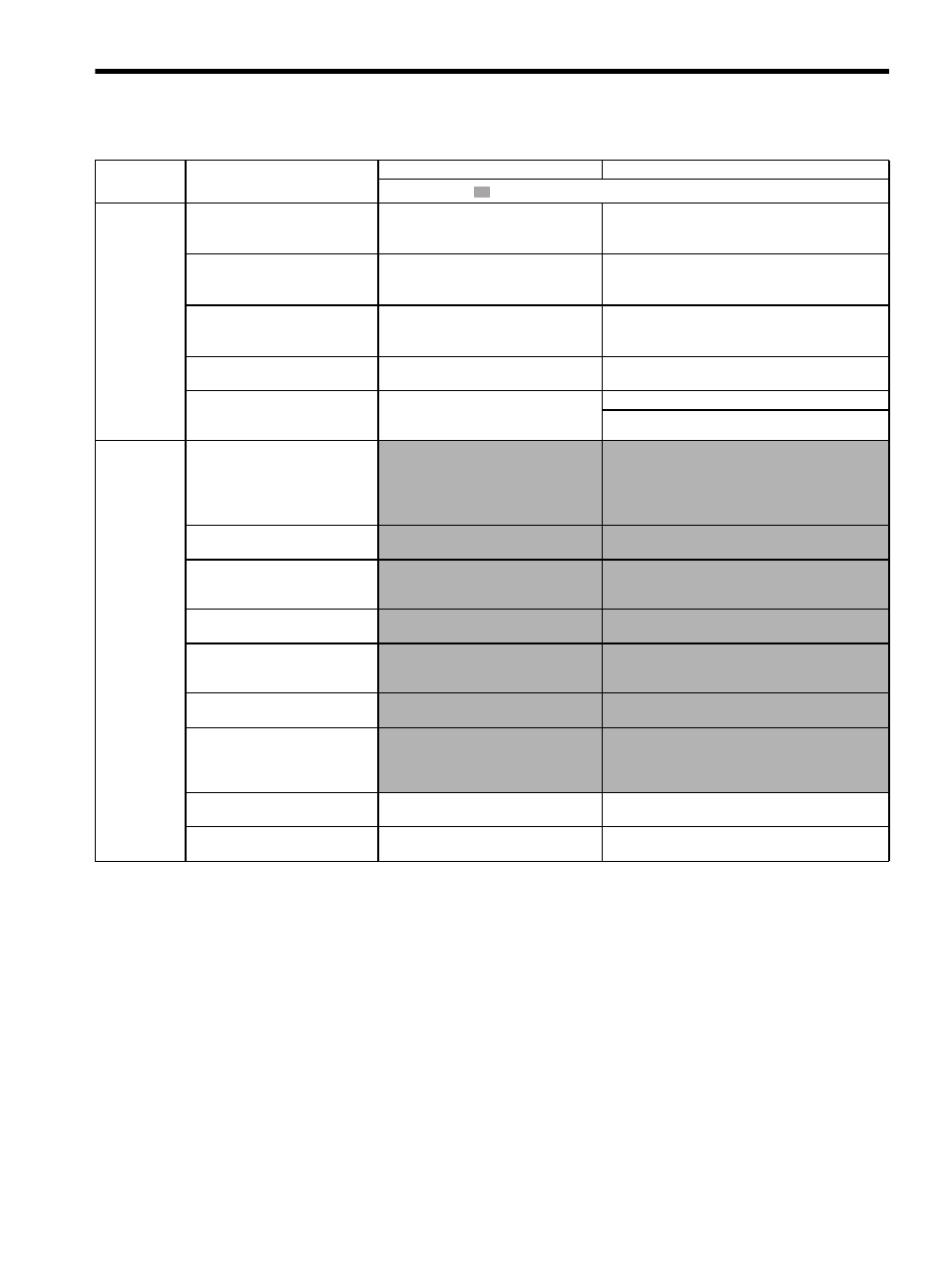
10.1 Troubleshooting
10-23
High Rota-
tion Speed
Overshoot on
Starting and
Stopping.
Speed loop gain value too high
Factory setting: Kv=40.0 Hz,
Refer to the gain adjustment in User’s
Manual.
Reduce the speed loop gain Pn100 preset value.
Position loop gain Pn102 value too
big
Factory setting: Kp=40.0/s
Refer to the gain adjustment in User’s
Manual.
Reduce the position loop gain Pn102 preset value.
Incorrect speed loop integral time
constant Pn101 setting
Factory setting: Ti=20.00 ms
Refer to the gain adjustment in User’s
Manual.
Correct the speed loop integral time constant Pn101
setting.
When the autotuning is used:
Incorrect machine rigidity setting
Check the machine rigidity setting Fn001.
Select a proper machine rigidity setting Fn001.
When the autotuning is not used:
Incorrect rotational moment of
inertia ratio
Check the rotational moment of inertia ratio
Pn103.
Correct the moment of inertia ratio Pn103.
Use the mode switch setting function.
ABS (abso-
lute) Position
Difference Er-
ror (The po-
sition saved
in Host con-
troller when
the power
turned OFF is
different from
the position
when the
power turned
ON.)
Noise interference due to improper
encoder cable specifications
The specifications of encoder cable must
be:
Tinned annealed copper twisted-pair or
twisted-pair shielded wires with core 0.12
mm
2
(0.0002 in
2
) min.
Use encoder cable with the specified specifications.
Noise interference because the
encoder cable distance is too long.
The wiring distance must be 20 m (65.6 ft)
max.
The encoder cable distance must be within the specified
range.
Noise interference due to damaged
encoder cable
Noise interference occurred to the signal
line because the encoder cable is bent or its
sheath damaged.
Correct the encoder cable layout.
Excessive noise to the encoder cable
Check if the encoder cable is bundled with a
high-current line or near high-current line.
Change the encoder cable layout so that no surge is
applied.
FG affected by noise from machines
such as welder installed on
servomotor side
Check if the grounding for the machine is
properly made.
Ground the machine separately from PG side FG.
SERVOPACK pulse counting error
due to noise interference
Check if the signal line from the encoder
receives influence from noise interference.
Take measures against noise for encoder wiring.
Excessive vibration and shock to the
encoder
Vibration from machine occurred or
servomotor mounting such as mounting
surface precision, fixing, and alignment is
incorrect.
Reduce vibration from machine or mount securely the
servomotor.
Encoder fault
An encoder fault occurred. (no change in
pulse count)
Replace the servomotor.
SERVOPACK fault
Check the multi-turn data from
SERVOPACK.
Replace the SERVOPACK.
Table 10.5 Troubleshooting for Malfunction without Alarm Display (Cont’d)
Symptom
Cause
Inspection
Corrective Actions
: Turn OFF the servo system before executing operations.