Function: aux reference (setting: 2), Function: pi feedback (setting: b), Function: frequency bias 2 (setting: d) – Yaskawa iQpump Controller Programming Manual User Manual
Page 89: Function: motor temperature (setting: e)
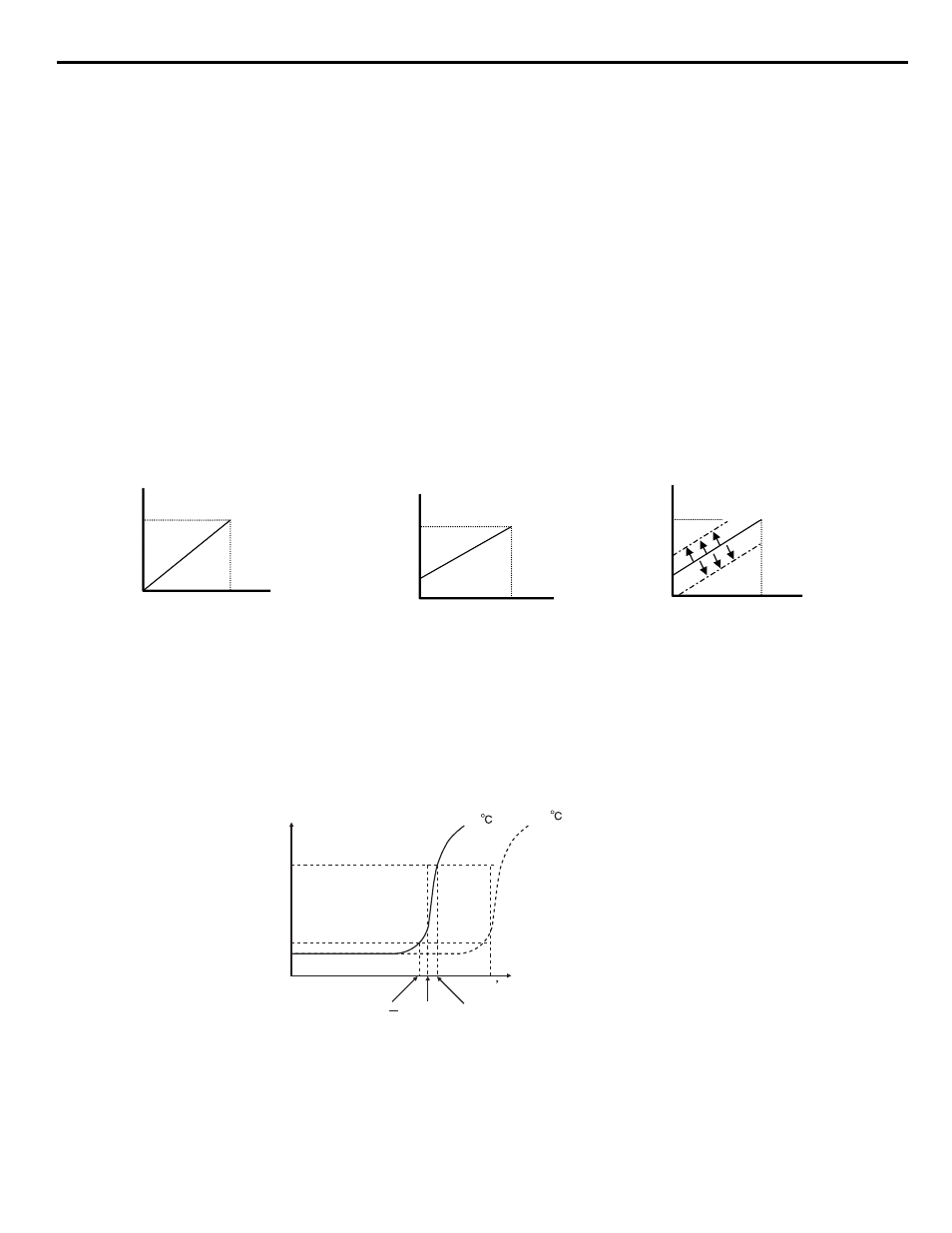
YASKAWA TM.iQp.07 iQpump Controller Programming Manual
89
■
Function: Aux Reference (Setting: 2)
In order for the A2 analog input to be used as the master Speed Command, parameter H3-09 must be set for Aux Reference (H3-09 = “2:
Aux Reference”). Once A2 is configured as an auxiliary reference, it can be selected as the master Speed Command by setting H3-13 =
“1: Main Fref TA2”. If H3-09 = 2, terminal A2 analog input will become the speed command when a digital input programmed for Multi-
Step Ref 1 (H1-0x = 3) is selected by a contact closure.
■
Function: PI Feedback (Setting: B)
Configuring the A2 analog input as PI Feedback (H3-09 = “B: PI Feedback”) is a requirement of setting the iQpump drive up for PI
operation. The A2 analog input is the only source for feedback for PI operation though the setpoint can come from a number of different
sources (refer to the section covering the PI parameters for more information regarding specifying the setpoint source. PI parameters are
listed in “b5 PI Function” on page 32).
Parameters H3-10 (Terminal A2 Gain) and H3-11 (Terminal A2 Bias) can be used to configure the A2 analog input to match the signal
from the Feedback Transmitter.
The U1-24 monitor (PI Feedback) can be used to check the PI Feedback level with the digital operator.
■
Function: Frequency Bias 2 (Setting: D)
By setting H3-09 = “D: Frequency Bias 2,” the A2 analog input will serve as a bias signal to the A1 Speed Command. This setting
functions the same as a setting of H3-09 = 0: Frequency Bias.
Figure 1.80
Figure 79. Frequency Bias 2 Applied to Analog Speed Command
■
Function: Motor Temperature (Setting: E)
In addition to or in place of the OL1 (Motor Overload) fault of the drive, it is possible to use a PTC (Positive Temperature Coefficient)
thermistor for motor insulation protection. The PTC thermistors are built into the windings of some motors and will vary their resistance
based on temperature. An example PTC characteristic is show below.
Figure 1.81
Figure 80. PTC Thermistor Temperature-Resistance Value Characteristics
Connection of the thermistor to the iQpump drive is shown below, in addition make sure Dip Switch S1-2 is in the OFF position, see
Factory Default
S
peed
C
o
mmand
10V
A1 Voltage
S
peed
C
o
mmand
A1 Voltage
10V
H3-03
H3-02
With H3-03 applied
S
peed
A1 Voltage
10V
With both H3-03 and analog input bias
(H3-09=0) applied
H3-02
H3-03
Sp
e
e
d
C
o
m
m
and
Sp
e
e
d
C
o
mma
n
d
Sp
e
e
d
C
o
m
m
and
(H3-09 = D) applied
Tr: Temperature threshold value
Tr
Tr+5
Tr
Tr
5
550
1330
Resistance (ohms)
Class F
150
Class H
180
Temperature