Yaskawa VS-626 MC5 User Manual
Page 189
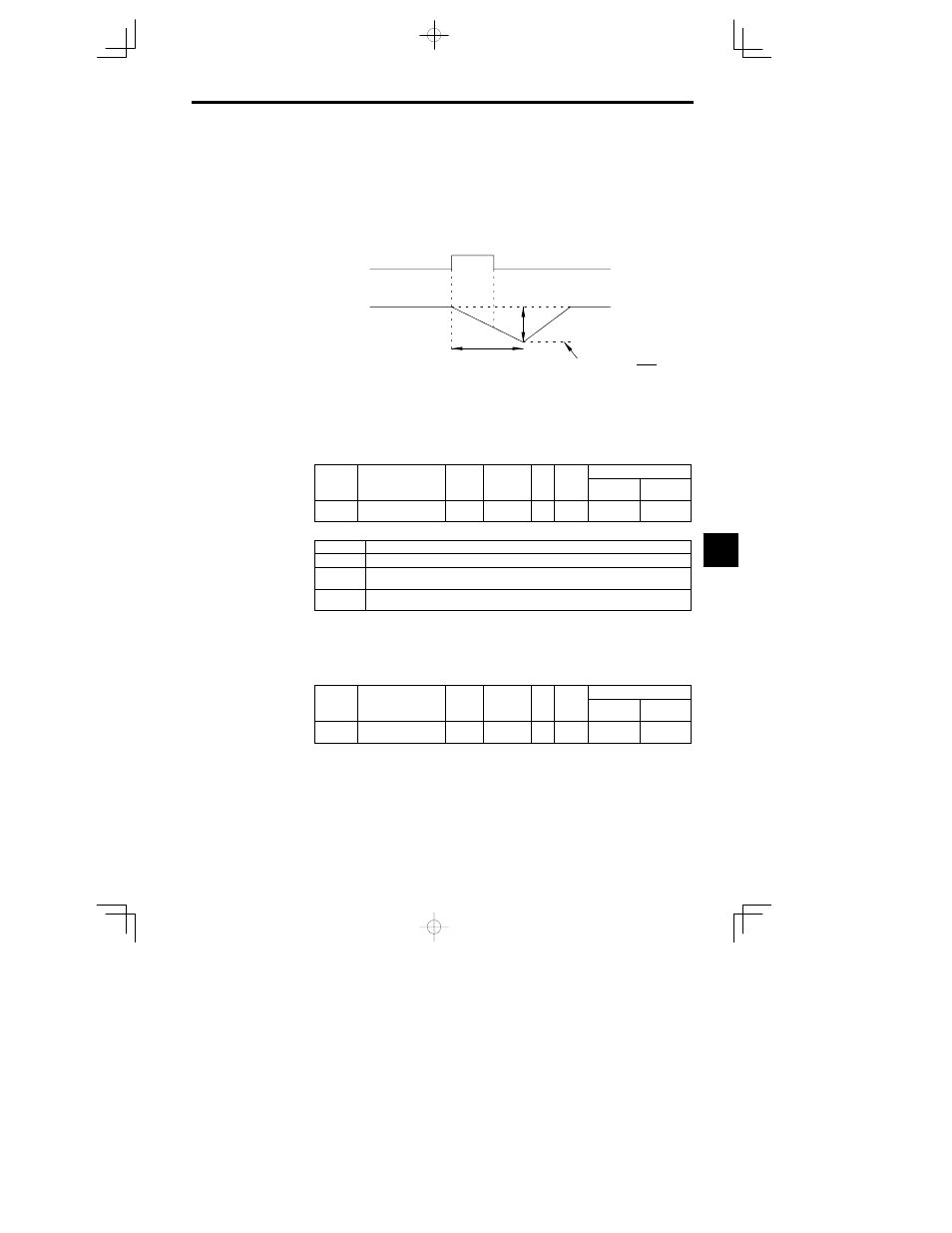
7.3
Common Functions
- 51
Operation
D
L2-06 = 0
The motor is automatically accelerated based on the emergency stop time (C1-09) so that the DC main-
line voltage does not go below the UV level. The momentary power loss ridethru time (L2-02) is not
used.
D
L2-06
0
The motor is decelerated to the KEB frequency level using the momentary power loss ridethru time
(L2-02) and then is accelerated to the original frequency reference using acceleration time 1 (C1-01).
The KEB frequency level is calculated from the KEB frequency rate using the following equation.
KEB frequency level Output frequency before power loss [1 -- (setting of L2-06)/100)]%
Multi-function input
terminal setting
(
H1
-
01
to
06
=
65
or 66)
OFF
ON
Momentary power loss ride-
thru time (L2-02)
L2
-
06
C1
-
01
OFF
Output frequency
Output frequency (1 --
L2-06
100%
)
J
Stall Prevention Function Settings: L3-01 to L3-06
D
A stall occurs if the rotor cannot keep up with the rotating magnetic field on the motor stator side when
a large load is applied to the motor or a sudden acceleration/deceleration is performed.
D
In the Inverter, stall prevention functions can be set independently for accelerating, running, and decel-
erating. (Some functions are restricted depending on the control method.)
Stall Prevention Selection During Acceleration: L3-01
User
Change
during
Setting
Factory
Valid Access Levels
User
Constant
Number
Name
during
Opera-
tion
Setting
Range
Unit
Factory
Setting
Open Loop
Vector
Flux Vector
L3-01
Stall prevention selec-
tion during accel
0 to 2
--
1
B
D
Settings
Setting
Function
0
Disabled. (Accelerate according to the settings. Stalls may occur with large loads.)
1
Enabled. (Stop acceleration if L3-02 setting is exceeded. Accelerate again when current recov-
ers.)
2
Optimum acceleration (Adjust acceleration so that the L3-02 isn’t exceeded by much. Disregard
the acceleration time setting.)
D
When setting 1 (enabled) is selected, acceleration is stopped if the motor current exceeds the accelera-
tion stall prevention level. Acceleration is started again when the current falls below this level. The
acceleration time can be longer than the setting depending on the load.
D
When setting 2 (optimum acceleration) is selected, acceleration is performed using the acceleration
stall prevention level as a basis. In this case, the acceleration time is disregarded.
Stall Prevention Level During Acceleration: L3-02
User
Change
during
Setting
Factory
Valid Access Levels
User
Constant
Number
Name
during
Opera-
tion
Setting
Range
Unit
Factory
Setting
Open Loop
Vector
Flux Vector
L3-02
Stall prevention level
during accel
0 to 200
%
150
B
D
This setting is valid when L3-01 is set to 1 or 2.
D
Normally it isn’t necessary to change this setting.
D
Decrease this setting when the motor capacity is small compared to the Inverter capacity or stalling
occurs when the motor is operated with the factory setting. The standard target setting is 2 to 3 times
the motor’s rated current. (Set this current value as a percentage of the Inverter’s rated current, i.e.,
100% corresponds to the Inverter’s rated current.)
7