Connected machinery vibrates when motor rotates, Pi output fault – Yaskawa Z1000 AC Drive HVAC User Manual
Page 233
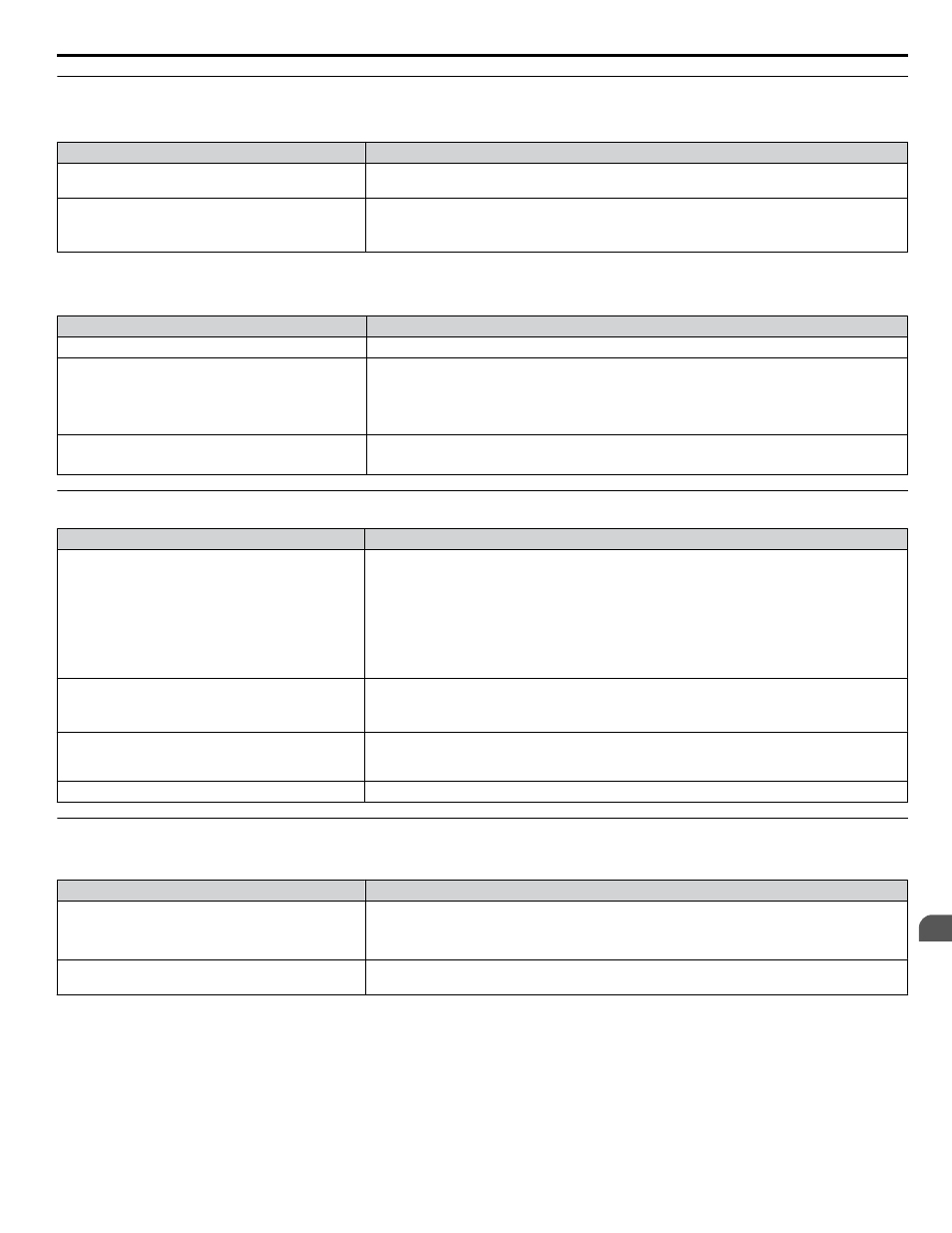
u
Connected Machinery Vibrates When Motor Rotates
n
Unexpected Noise from Connected Machinery
Cause
Possible Solutions
The carrier frequency is at the resonant frequency of
the connected machinery.
Adjust the carrier frequency using parameters C6-02 through C6-05.
The drive output frequency is the same as the resonant
frequency of the connected machinery.
• Adjust the parameters used for the Jump frequency function (d3-01 through d3-04) to skip the
problem-causing bandwidth.
• Place the motor on a rubber pad to reduce vibration.
Note:
The drive may have trouble assessing the status of the load due to white noise generated from using Swing PWM (C6-02 = 7 to A).
n
Oscillation or Hunting
Cause
Possible Solutions
Gain is too low when using PI control.
Refer to b5: PI Control on page 266
The frequency reference is assigned to an external
source and the signal is noisy.
• Ensure that noise is not affecting the signal lines.
• Separate main circuit wiring and control circuit wiring.
• Use twisted-pair cables or shielded wiring for the control circuit.
• Increase the analog input time filter constant (H3-13).
The cable between the drive and motor is too long.
• Perform Auto-Tuning for line-to-line resistance.
• Reduce the length of the cable.
u
PI Output Fault
Cause
Possible Solutions
No PI feedback input.
• Check the multi-function analog input terminal settings.
• Set multi-function analog input terminal A1 or, A2 for PI feedback (H3-02 or H3-10 = B).
• A signal input to the terminal selection for PI feedback is needed.
• Check the connection of the feedback signal.
• Check the various PI-related parameter settings.
• No PI feedback input to the terminal causes the value detected to be 0, causing a PI fault and
the drive to operate at max frequency.
The level of detection and the target value do not
correspond with each other.
• PI control keeps the difference between target and detection values at 0. Set the input level for
the values relative to one another.
• Use analog input gains H3-03 and H3-11 to adjust PI target and feedback signal scaling.
Reverse drive output frequency and speed detection.
When output frequency rises, the sensor detects a
speed decrease.
Set PI output for reverse characteristics (b5-09 = 1).
PI parameter setting adjustments are insufficient.
Refer to b5: PI Control on page 266
for details.
u
Motor Rotates after the Drive Output is Shut Off (Motor Rotates During DC Injection
Braking)
Cause
Possible Solutions
DC Injection Braking is set too low and the drive
cannot decelerate properly.
• Adjust the DC Injection braking settings.
• Increase the current level for DC Injection Braking (b2-02).
• Increase the DC Injection Braking time at stop (b2-04).
The stopping method is set so that the drive coasts to
stop.
Set b1-03 (Stopping Method Selection) to 0 or 2.
5.10 Troubleshooting without Fault Display
YASKAWA ELECTRIC TOEP YAIZ1U 03A YASKAWA AC Drive – Z1000 User Manual
233
5
Troubleshooting