Yaskawa MP920 User's Manual Design User Manual
Page 163
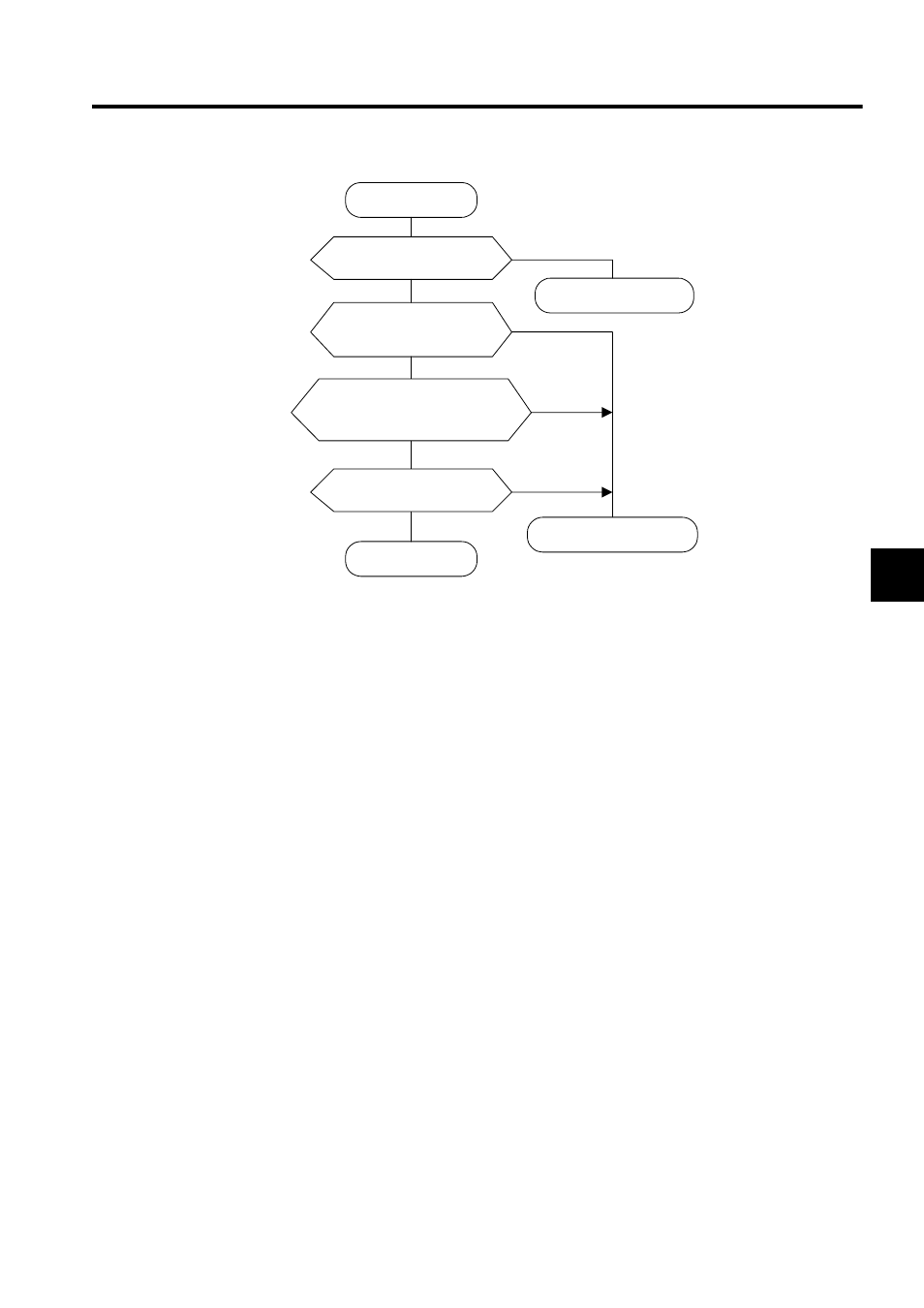
4.4 Position Control Using Motion Commands
4-49
4
6. Start positioning command execution.
The axis starts positioning according to the specified motion parameters. Even during
positioning, the motion parameter settings can be changed.
The positioning command operations are as follows:
a) Operation Start
Servo ON (bit 0 of OW01).
Set the positioning (POSING = 1) to motion command code (OW20).
b) Feed Hold
Set Hold (bit 0 of OW21) to ON.
At feed hold completion, HOLDL (bit 1 of IW15) turns ON.
c) Feed Hold Release
Set Hold (bit 1 of OW21) to OFF. Positioning resumes.
d) Abort
Set Abort (bit 1 of OW21) to ON, or set NOP (= 0) in the motion command code.
Busy (bit 0 of IW15) turns ON during abort processing, and turns OFF at comple-
tion of the abort.
Note: When the abort has been completed and released (ABORT turns
OFF), the following occurs:
• When the Position Reference Type (bit 14 of OW01) is the absolute position mode
(= 0), positioning resumes in the direction of the Position Reference (OL12).
• When the Position Reference Type (bit 14 of OW01) is the incremental addition
mode (= 1), operations remain stopped until the Reference Position (OL12) is reset.
Return (OK)
YES
YES
YES
NO
NO
NO
YES
NO
POSING
Start condition check
Control mode
= position control mode?
Return (NG)
Motion command code
=NOP
||POSING||
ENDOF_INTERPOLATE?
Motion command response
=NOP
||POSING||
INTERPOLATE
||
ENDOF_INTERPOLATE?
Motion command status
BUSY=OFF?
Return (NG)