Yaskawa MP2200 Machine Controller User Manual
Page 154
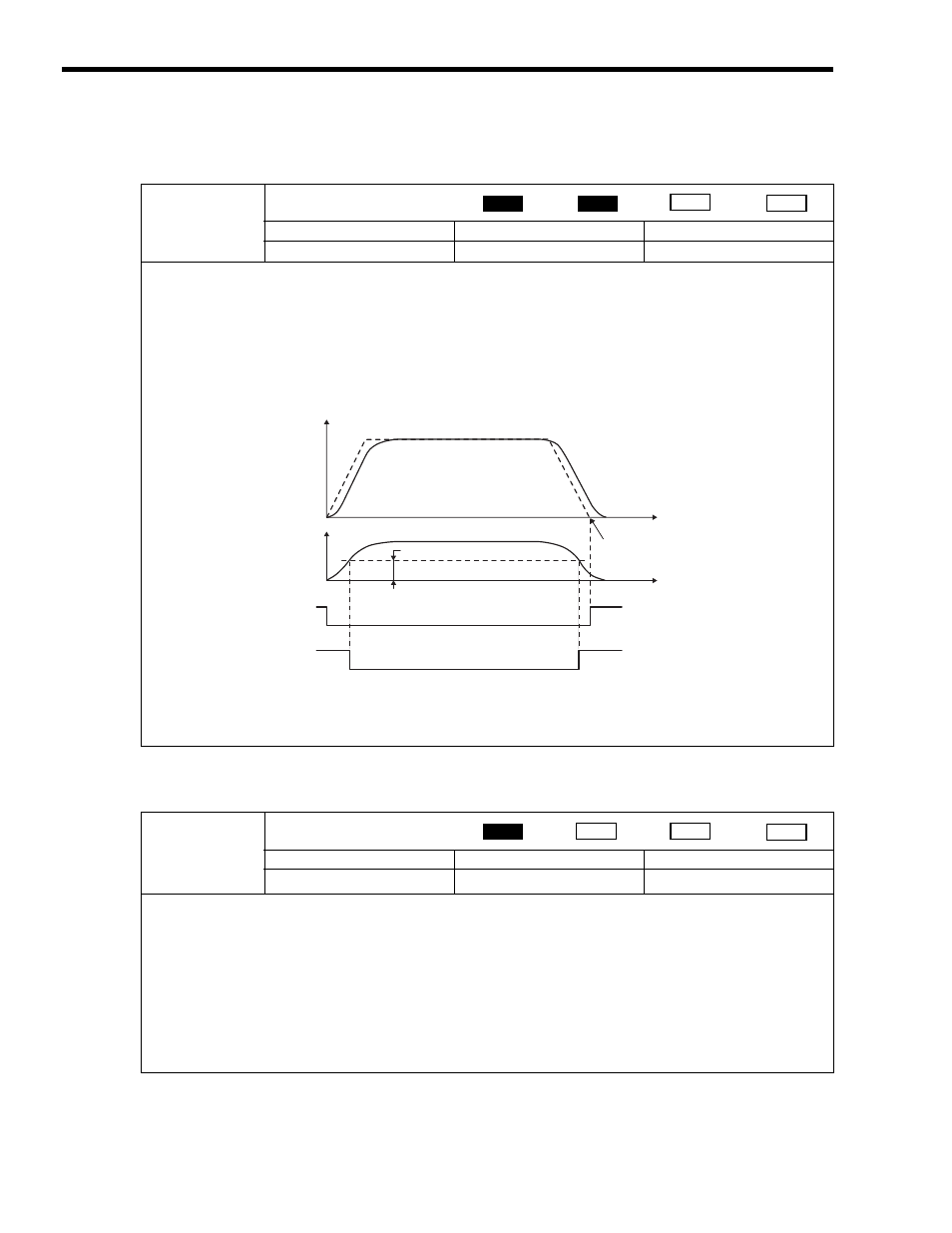
4 Motion Parameters
4.3.2 Motion Setting Parameter Details
4-34
( 17 ) Positioning Completed Width 2
( 18 ) Deviation Abnormal Detection Value
OL20
Positioning Completed Width
2
Setting Range
Setting Unit
Default Value
0 to 65535
Reference unit
0
The Position Proximity (IB0C3) will be turned ON when the absolute value of the difference between the command position
and the feedback position is less than the value set here.
If the Positioning Completed Width 2 is set to 0, the Position Proximity bit (monitoring parameter IB0C3) will be turned ON
when the reference pulses have been distributed. (monitoring parameter IB0C0)
If the Positioning Completed Width 2 is set to a value other than 0, this bit will be turned ON when the result of subtracting the
Machine Coordinate Feedback Position (monitoring parameter IL16) from the Machine Coordinate System Position
(monitoring parameter IL12) is less than the Position Completed Width 2, even if the reference pulses have not been
distributed. This parameter has no relation to the SERVOPACK parameter Position Proximity (NEAR) Signal Width.
■
Related Parameters
IB0C3
Position Proximity
Position
Phase
Speed
Torque
Speed
Position Error
(IL
1A)
Positioning Completed Width 2
Distribution completed
Positioning
Completed
Width 2 = 0
Positioning
Completed
Width 2
≠ 0
OL22
Deviation Abnormal Detection
Value
Setting Range
Setting Unit
Default Value
0 to 2
31
−1
Reference unit
2
31
−1
Set the value to detect an excessively following error during position control.
The Excessively Following Error bit (IB049) will turn ON if the result from subtracting the Machine Coordinate Feedback
Position (monitoring parameter IL16) from the Machine Coordinate System Position (monitoring parameter IL12)
exceeds the value set here. An excessive following error will not be detected if this value is set to 0.
■
Related Parameters
An excessively following error can be set to be treated either as a warning or as an alarm in the Deviation Abnormal Detection
Error Level in Mode 1 (setting parameter OB010).
OB010 = 0
Warning (continues axis operation)
OB010 = 1
Alarm (stops axis operation)
Position
Phase
Speed
Torque