21 ) latch ( 22 ) gain and bias settings – Yaskawa MP2200 Machine Controller User Manual
Page 156
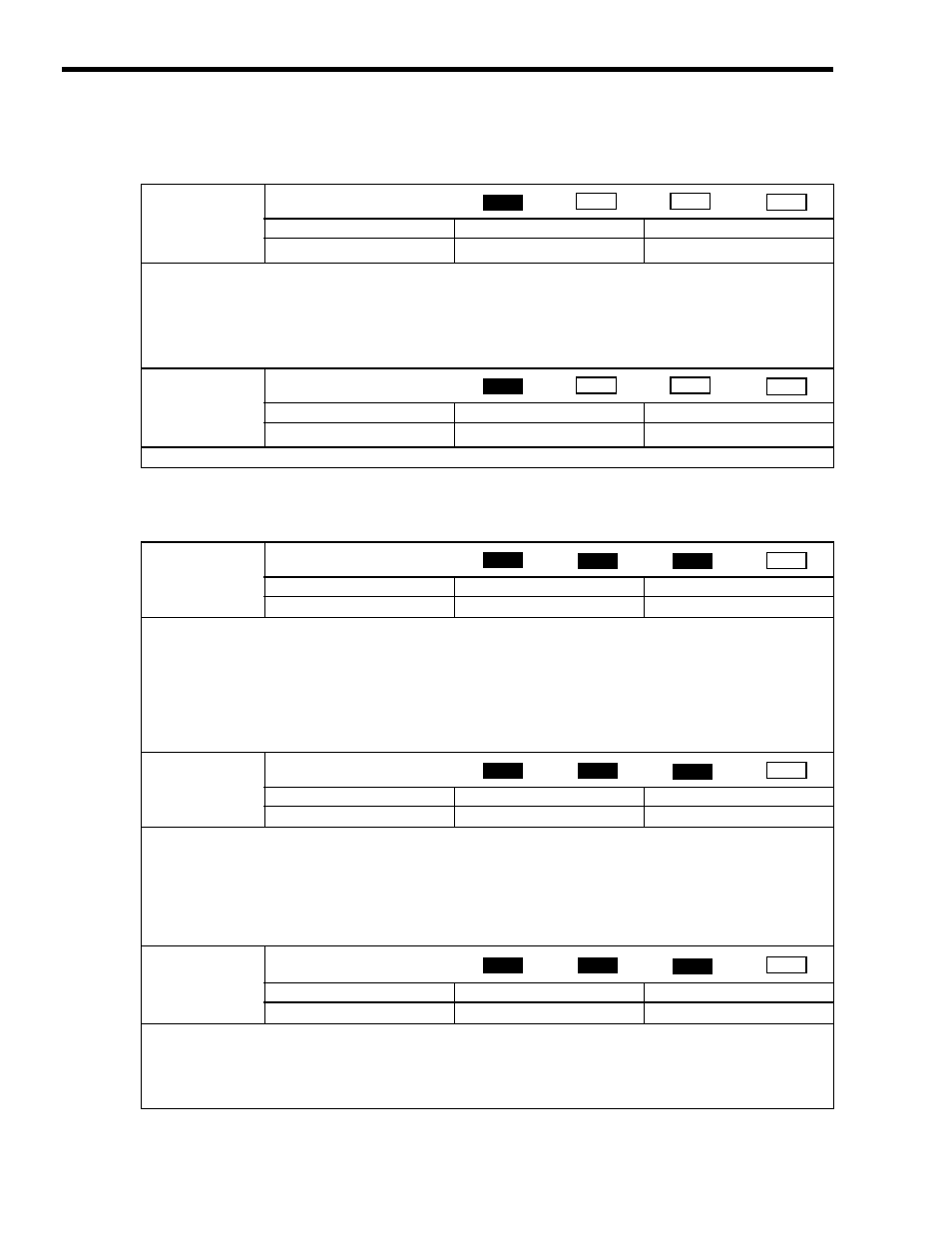
4 Motion Parameters
4.3.2 Motion Setting Parameter Details
4-36
( 21 ) Latch
( 22 ) Gain and Bias Settings
OL2A
Latch Zone Lower Limit
Setting Range
Setting Unit
Default Value
−2
31
to 2
31
−1
Reference unit
−2
31
Set the range in which the latch signal is valid (position from the zero position) for external positioning.
The set value here is written to the SERVOPACK parameters each time an external positioning command is executed as long as
the latch zone is enabled in the Latch Zone Enabled bit in Motion Command Options (setting parameter OW09, bit 4).
The latch zone setting is supported for SGDS SERVOPACKs for MECHATROLINK-II communication only.
Latching Area Upper Limit: Pn820
Latching Area Lower Limit: Pn822
OL2C
Latch Zone Upper Limit
Setting Range
Setting Unit
Default Value
−2
31
to 2
31
−1
Reference unit
2
31
−1
Same as for OL2A.
Position
Phase
Speed
Torque
Position
Phase
Speed
Torque
OW2E
Position Loop Gain
Setting Range
Setting Unit
Default Value
0 to 32767
0.1/s
300
Determine the responsiveness for the SERVOPACK’s position loop.
If the position loop gain is set high, the responsiveness is high and the positioning time is short.
Set the optimum value for the machine rigidity, inertia, and type of Servomotor.
The actual machine operation depends on the settings in the SERVOPACK parameters. Refer to 9.4 Parameters That Are Auto-
matically Updated for details on making parameters automatically effective.
If this parameter changes, the corresponding SERVOPACK parameter will change automatically.
This function is achieved using the Servo command expansion area and can be executed when using the MECHATROLINK-II
(32-byte Mode) communication method. The motion command KPS must be used to make changes to this parameter.
OW2F
Speed Loop Gain
Setting Range
Setting Unit
Default Value
1 to 2000
Hz
40
Determine the responsiveness for the SERVOPACK’s speed loop. The Servo system will be more stable the higher this
parameter is set, as long as the value is within the range in which the mechanical system does not oscillate.
The actual machine operation depends on the settings in the SERVOPACK parameters. Refer to 9.4 Parameters That Are Auto-
matically Updated for details on making parameters automatically effective.
If this parameter changes, the corresponding SERVOPACK parameter will change automatically.
This function is achieved using the Servo command expansion area and can be executed when using the MECHATROLINK-II
(32-byte Mode) communication method. The motion command KVS must be used to make changes to this parameter.
OW30
Speed Feed Forward
Compensation
Setting Range
Setting Unit
Default Value
0 to 32767
0.01%
0
Reduces positioning time by applying feed forward compensation.
This setting is effective for position control commands. Always set this parameter to 0 for phase control.
If this parameter changes, the corresponding SERVOPACK parameter will change automatically.
This function is achieved using the Servo command expansion area and can be executed when using the MECHATROLINK-II
(32-byte Mode) communication method. The motion command KFS must be used to make changes to this parameter.
Position
Phase
Speed
Torque
Position
Phase
Speed
Torque
Position
Phase
Speed
Torque