Pump system fault setup pre-charge operation, Sleep mode (example), Pump running – Yaskawa iQpump1000 AC Drive Quick Start User Manual
Page 9
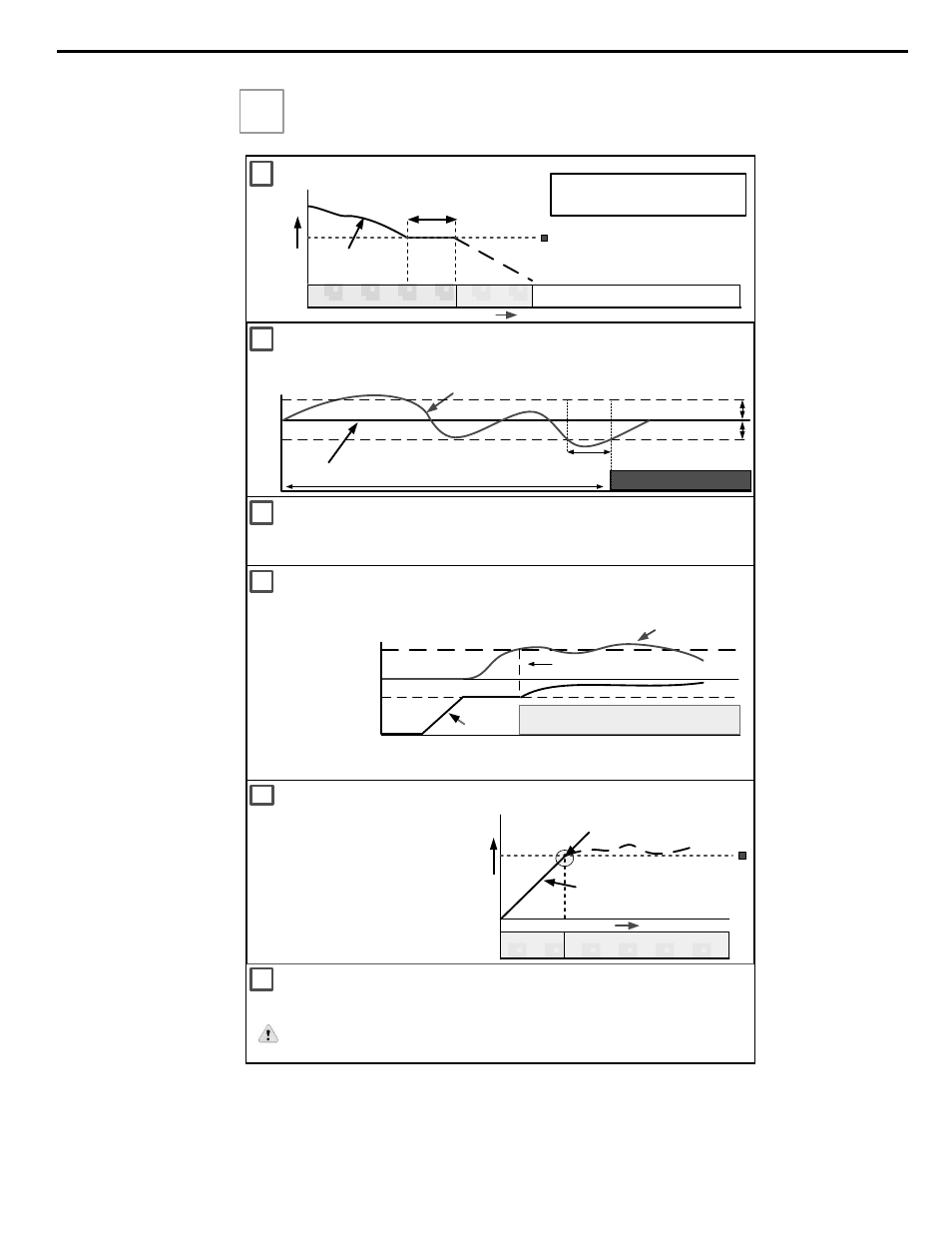
Step
7
iQpump Factory Defaults Overview
(adjust certain settings specific to the application)
THRUST BEARING - SUBMERSIBLE MOTORS
When using a submersible motor in combination
with the iQpump, it is recommended to use the
Thrust Bearing function to prevent excess motor
wear. To enable this function, enter the minimum
motor frequency in parameter
P4-11. Example: Minimum motor speed 1800
RPM, 1800 RPM ÷ 3600 RPM x 60.0 Hz = 30.0 Hz
Output Frequency
Output Frequency
Thrust Bearing Frequency P4-12
(Example 30.0 Hz)
Time
Thrust
Bearing
Auto/Hand Operation
Turn Off Thrust Bearing Function
(Output Frequency Reached)
P4
-04
Accel
. T
ime
Thrust Acceleration Time P4-11
(Example 1.0 sec.)
C1-01 Acceleration Time
PUMP SYSTEM FAULT SETUP
PRE-CHARGE OPERATION
5
4
6
7
LOW/HIGH FEEDBACK LEVEL DETECTION
AUTO OPERATION – POWER DOWN STORAGE
8
Allows iQpump to automatically start after power failure when operated from keypad / digital operator. This function is
recommended for use when operating the iQpump in remote / unmanned areas. Use parameter P4-10 to enable.
When the iQpump is powered down while running , an internal run
command will automatically be initiated upon power -up.
This function is used when the pump system requires to be pre-charged before normal operation. Upon start the
iQpump will run at a fixed speed for a specified time or until the feedback signal reaches a programmed level after
which it will switch to auto mode operation.
Feedback
0 Hz
Pre-Charge Freq. P4-02
Pre-Charge Completed
Pre-Charge Lvl. P4-01
P4-01 Pre-Charge Level: Specified feedback level to stop pre-charge operation
P4-02 Pre-Charge Frequency: Set desired pre-charge speed
P4-03 Pre-Charge Time: Specified maximum pre-charge operation time
FEEDBACK SIGNAL
P1-11
Time
SETPOINT
SET-POINT NOT MET
P1-16
Setpoint -LOP Tim
The iQpump can display a ‘Setpoint Not Met’ fault when the iQpump is unable to maintain the programmed system
setpoint due a problem with the pump system. Set P1-15 to the maximum allowed difference between setpoint and
feedback level.
P1-11
P1-15 Max Setpoint Diff
iQpump continuously monitors the system feedback signal. To display a ‘Low Feedback’ fault set the low feedback
level parameter P1-08 to the minimum feedback level allowed for your system and to display a ‘High Feedback’
fault set the high feedback level parameter P1-11 to the maximum feedback level allowed.
Auto Operation
Output
Frequency
SLEEP MODE (Example)
Minimum Speed P1-06
(Example 40.0 Hz)
Output Frequency
(pump motor speed)
0
Sleep Delay Time (P2-03)
(Example 5.0 sec.)
Ramp or Coast to Stop, b1-02
Output Frequency
60 Hz
Pump Running
Go to Sleep
Time
WAIT FOR PRESSURE TO FALL BELOW
START / DRAW DOWN LEVEL (P1-04)
SYSTEM GOES TO SLEEP WHEN
PUMP MOTOR SPEED DROPS BELOW
40 Hz (2400 RPM for 3600 RPM Motor).
3
YASKAWA TOEP YAIP1W 01B YASKAWA AC Drive - iQpump1000 Quick Start Guide
9