Thermal curve (49tc) protection, Element operation, Modes of protection – Basler Electric BE1-11m User Manual
Page 107
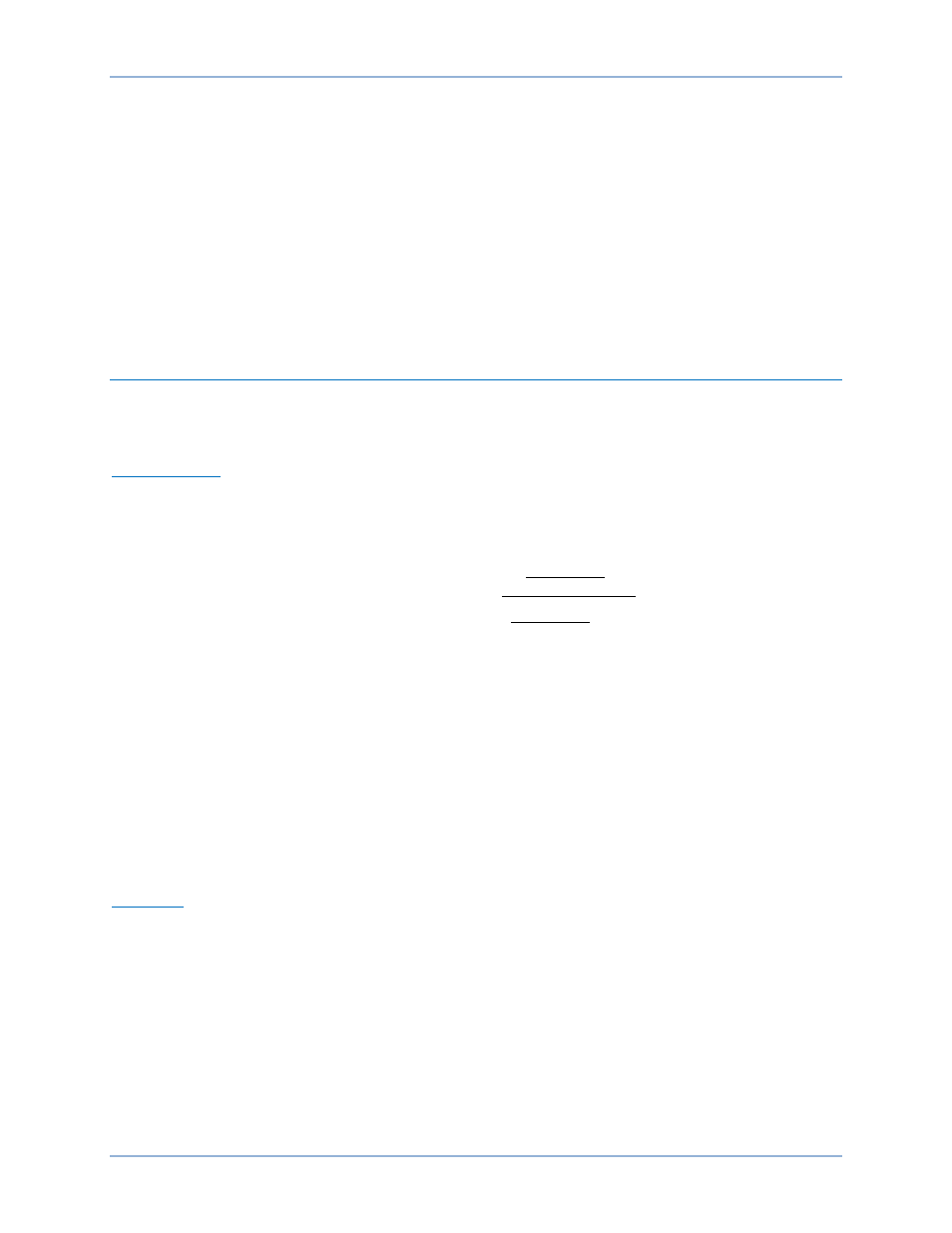
9424200996 Rev L
95
Thermal Curve (49TC) Protection
The thermal curve (49TC) element models the thermal capacity in a motor to provide thermal protection.
The element uses voltage level and negative-sequence current to modify the thermal curve.
Element logic connections are made on the BESTlogic
™Plus screen in BESTCOMSPlus® and element
operational settings are configured on the Thermal Curve (49TC) settings screen in BESTCOMSPlus. A
summary of the logic inputs and outputs and operational settings appears at the end of this chapter.
BESTCOMSPlus Navigation Path: Settings Explorer, Protection, Thermal, Thermal Curve (49TC)
HMI Navigation Path: Settings Explorer, Protection, Settings Group x (where x = 0 to 3), Thermal
Protection, Thermal Curve 49TC
Element Operation
Modes of Protection
Three modes of protection are available: Standard Curve, IEC Curve, and User Curve.
Standard Curve
The Standard Curve Time Dial setting determines the time to trip when the 49TC element is configured
for Standard Curve mode. The standard curve provides a I
2
curve with a range of time dial settings that
accommodate a wide range of motor timings. The standard curve equation is shown in Equation 4.
t = TD × 88.744132 × ln
⎣
⎢
⎢
⎢
⎡ �
I
eq
S ∙ SF ∙ FLA�
2
�
I
eq
S ∙ SF ∙ FLA�
2
− 1⎦⎥
⎥
⎥
⎤
With max value of I
eq
/(S
•SF•FLA) of 10.
Equation 4. Standard Curve
Where:
t
= Operating time
I
eq
= Measured equivalent motor current
TD = Time Dial
FLA = Full Load Amps
SF = Service Factor
S
= Overload Scaler
ln
= Natural log
IEC Curve
IEC curves provide the ability to automatically change between two curves based on whether the motor is
hot or cold. The hot or cold status is shown on the front-panel display under Metering Explorer, Status,
Motor Status, Thermal Curve.
An internal cold-to-hot timer is initiated when the motor is started from a cold state. The timer continues
after the motor is running. The motor is determined as hot when the internal timer exceeds the Running
Cool Time Constant (RCTC) setting and the hot curve shown in Equation 5 is used. If the motor is
stopped before the RCTC setting is exceeded, the motor remains in a cold state and the timer resets at
zero. It is recommended that the IEC Hot Curve Current setting (I
p
) is set no greater than 95% of the
thermal current pickup (S
• SF • FLA).
An internal hot-to-cold timer is initiated when the motor is stopped while in a hot state and the thermal
capacity is less than 10%. The motor is determined as cold when the internal timer exceeds the Stopped
Cool Time Constant (SCTC) setting and the cold curve shown in Equation 6 is used. If the motor is
BE1-11m
Thermal Curve (49TC) Protection