Basler Electric BE1-11m User Manual
Page 535
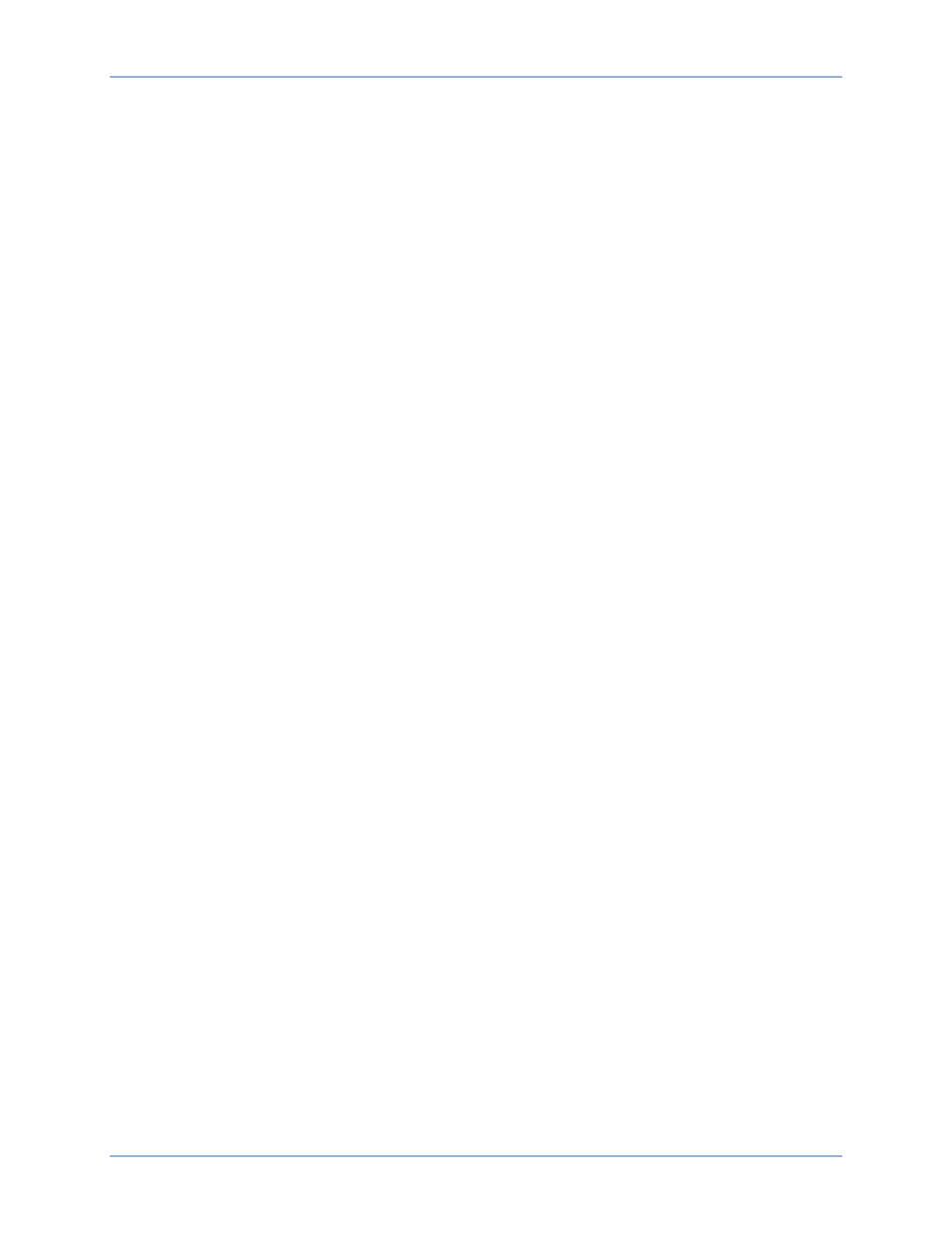
9424200996 Rev L
523
where,
I
eq
= equivalent thermal current in PU (unit of thermal pickup current)
I = maximum phase current in PU
I1 = positive-sequence fundamental component of current in PU
I2 = negative-sequence fundamental component of current in PU
K = constant used to determine additional heating due to negative-sequence
current in PU
•
Overload - By default, the thermal model begins timing towards a trip when the effective motor
current exceeds SF (Service Factor)
• FLA (Full Load Amps). The Overload setting adjusts the pickup
level between 90 and 120 percent of SF
• FLA if needed for the motor application; resulting in a total
pickup equation of S
• SF • FLA. In this example, Overload (S) is left at the default setting of 1.00.
•
Standard Curve Time Dial - Examine the motor manufacturer’s data and select a curve time dial to
coordinate closely with the curve shown in Figure 339. Motor thermal limits have three parts based on
three operational conditions: 1) locked rotor or stall, 2) starting or acceleration, and 3) running
overload. The overload protection curve should be set slightly lower than the thermal limits provided
by the manufacturer to ensure that the motor is tripped before reaching the thermal limit. Examine
Figure 348 to determine the standard curve time dial that best coordinates with the motor running
overload (upper portion of the curve). Curve 2 is chosen in this example. Set the Standard Curve
Time Dial to 2.
•
Max Emergency Thermal Capacity - The standard timing is based on the motor reaching 100
percent of thermal capacity. For emergency starts, it may be desired to allow the motor to reach
greater thermal capacities, or disable tripping on thermal capacity altogether. This setting determines
the maximum motor thermal capacity overload at which an emergency start can be performed. For
this example, the maximum emergency thermal capacity is set to 150 percent. The life of the motor
shortens as the motor is allowed to exceed 100 percent of thermal capacity. Caution should be used
when selecting the Max Emergency Thermal Capacity.
•
RTD Biasing - Thermal overload curves are based on the assumption of a normal 40
°C ambient and
normal motor cooling. In the case of unusual ambient temperature or blocked or reduced motor
cooling, the optional installed RTDs can be used to improve the estimation of thermal capacity. Set
RTD Biasing to Enabled to use the stator RTDs on the motor. See the paragraphs on RTD Bias
Curve to set the bias curve.
•
RTD Source - Any of the RTD blocks can be used as the RTD source for biasing. Previously, the
RTDs were configured in the following three blocks: Stator, Bearing, and Ambient. Set the RTD
Source to Stator. The RTD with the highest temperature in the Stator group is selected for biasing.
•
Running Cool Time Constant - This setting defines the cooling rate of the motor when the 49TC
element is not picked up and the motor is running. Set the Running Cool Time Constant to 60 minutes
per the motor manufacturer data.
•
Stopped Cool Time Constant - This setting defines the cooling rate of the motor when the 49TC
element is not picked up and the motor is stopped. Set the Stopped Cool Time Constant to 75
minutes per the motor manufacturer data.
•
Hot Safe Stall Time - This setting defines the time that the motor is allowed to be in a stalled hot
condition. Motor damage occurs after this time expires. Set the Hot Safe Stall Time to 9 seconds per
the motor manufacturer data.
•
Cold Safe Stall Time - This setting defines the time that the motor is allowed to be in a stalled cold
condition. Motor damage occurs after this time expires. Set the Cold Safe Stall Time to 10 seconds
per the motor manufacturer data.
BE1-11m
Settings Calculation Examples