Troubleshooting table no alarm display – Yaskawa Sigma II Series Servo System User Manual
Page 426
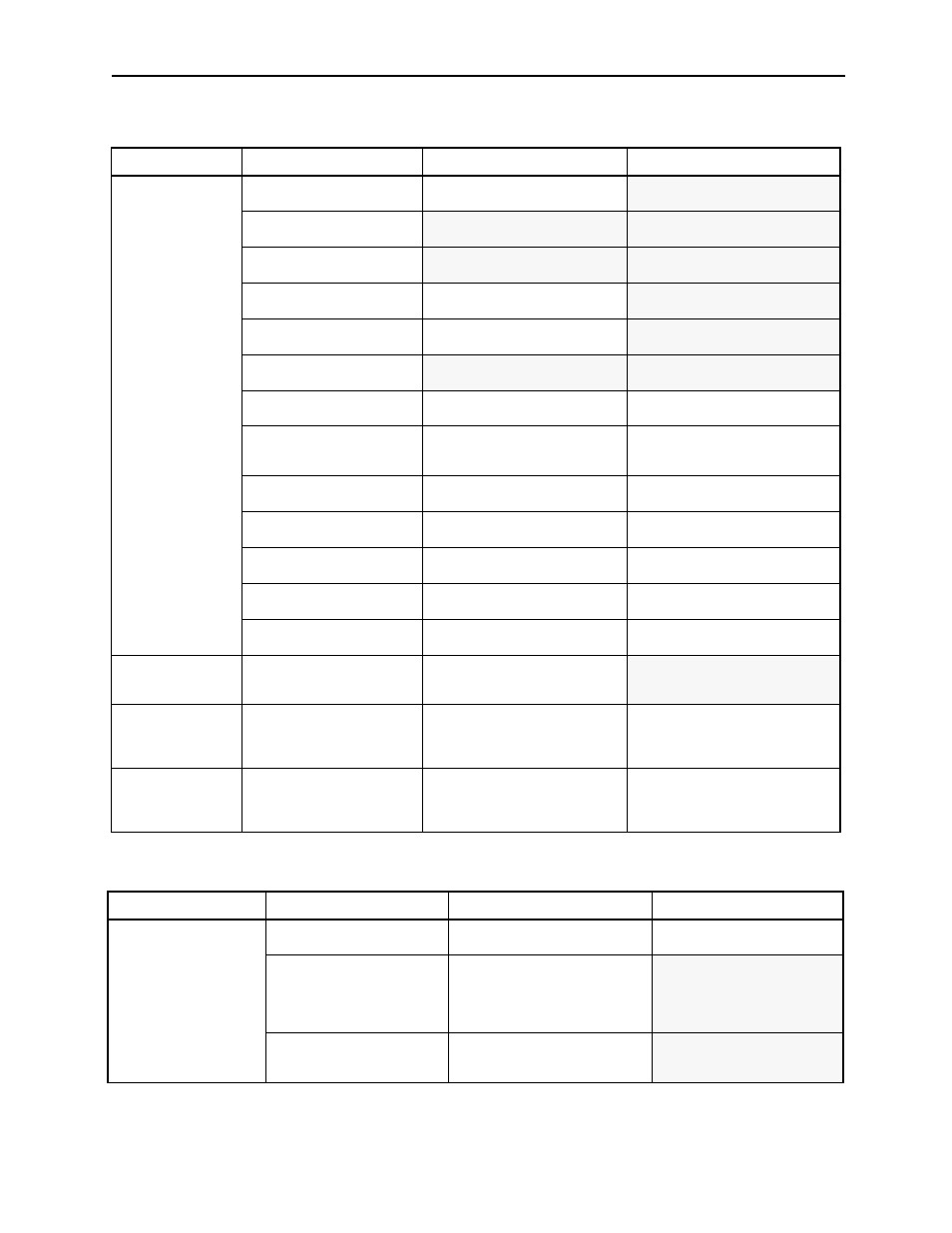
Sigma II User’s Manual
Chapter 9: Inspection, Maintenance, and Troubleshooting
9 - 38
Troubleshooting Table No Alarm Display
Symptom
Cause
Comment
Solution
Servomotor does
not start
Power not connected
Check voltage between
power supply terminals.
Correct the power circuit.
Loose connection
Check terminals of connec-
tors (CN1, CN2).
Tighten any loose parts.
Connector (CN1) external
wiring incorrect
Check connector (CN1)
external wiring
Refer to connection diagram
and correct wiring.
Servomotor or encoder
wiring disconnected.
—
Reconnect wiring
Overloaded
Run under no load.
Reduce load or replace with
larger capacity servomotor.
No speed/position
references input
Check reference input pins.
Correctly input speed/position
references.
/S-ON is turned OFF
Check settings of parameters
Pn50A.0 and Pn50A.1.
Turn /S-ON input ON.
/P-CON input function set-
ting incorrect
Check parameter Pn000.1.
Refer to section 5.3.5 and set
parameters to match
application.
Reference pulse mode
selection incorrect.
Refer to section 5.2.2
Correct setting of parameter
Pn200.0.
Encoder type differs from
parameter setting.
Confirm whether incremental
or absolute encoder is used.
Set parameter Pn002.2 to the
encoder type being used.
P-OT and N-OT inputs
are turned OFF.
Refer to section 5.1.2.
Turn P-OT and N-OT input
signals ON.
CLR input is turned ON
Check status of error counter
clear input.
Turn CLR input OFF.
SEN input is turned OFF.
When absolute encoder is
used.
Turn SEN input ON.
Servomotor
moves suddenly,
then stops
Servomotor or encoder
wiring incorrect.
—
Refer to chapter 3 and
correct wiring.
Suddenly stops
during operation
and will not
restart
Alarm reset signal
(/ALM-RST) is turned ON
because an alarm
occurred
—
Remove cause of alarm. Turn
alarm reset signal (ALM-RST)
from ON to OFF.
Unstable servo-
motor speed.
Defective wiring
connection to the motor.
Check the connections of the
power lead (U-, V-, and
W-phases) and the encoder
connectors.
Tighten any loose terminals or
connectors
Symptom
Cause
Comment
Solution
Servomotor vibrates
at approximately 200
to 400Hz.
Speed loop gain value too
high.
—
Reduce speed loop gain
(Pn100) preset value.
Speed/position reference
input wire too long.
—
Minimize length of speed/
position reference input
wire, with impedance not
exceeding several hundred
ohms
Speed/position reference
input wire is bundled with
power cables.
—
Separate reference input
wire at least 30cm from
power cables.