Yaskawa G7 Drive User Manual
Page 109
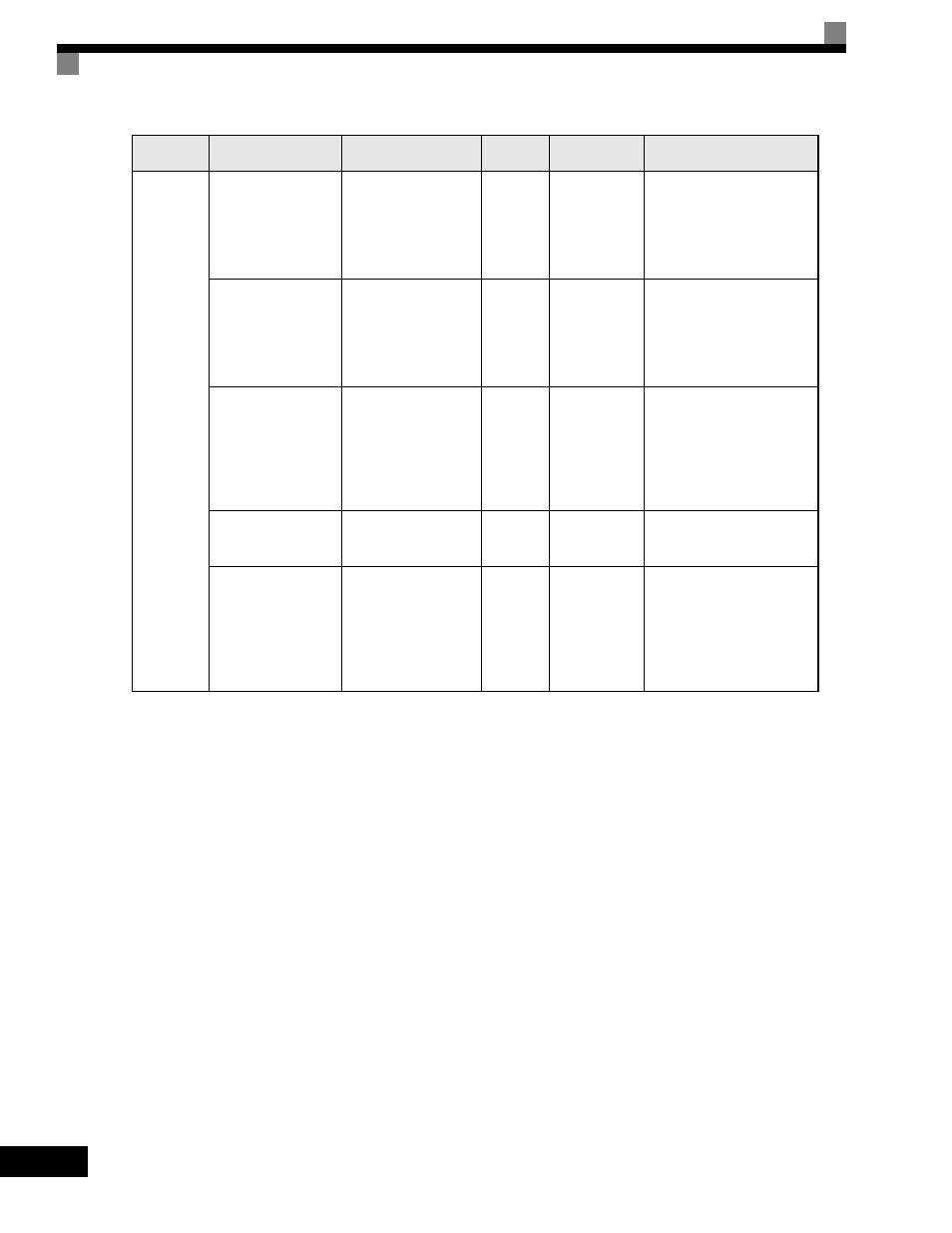
4
-20
* The setting is given for 200-240 V Class Drives. Double the voltage for 380-480V Class Drives.
•
Do not change the Torque Compensation Gain (C4-01) from its default setting of 1.00 when using open-
loop vector control 1.
•
If speeds are inaccurate during regeneration in open-loop vector control 1, enable Slip Compensation Dur-
ing Regeneration (C3-04 = 1).
•
Use slip compensation to improve speed precision during V/f control (A1-02 = 0).
Set the Motor Rated Current (E2-01), Motor Rated Slip (E2-02), and Motor No-load Current (E2-03), and
then adjust the Slip Compensation Gain (C3-01) to between 0.5 and 1.5. The default setting for V/f control
is C3-01 = 0.0 (slip compensation disabled).
•
To improve speed response and stability in V/f control with a PG (A1-02 = 1), set the ASR parameters
(C5-01 to C5-05) to between 0.5 and 1.5 times the default. (It is not normally necessary to adjust this set-
ting.) ASR for V/f control with a PG will only control the output frequency; a high gain, such as is possible
for open-loop vector control 2 or flux vector control, cannot be set.
The following user parameters will also indirectly affect the control system.
Open-loop
vector
control 2
(A1-02 = 4)
ASR proportional
gain 1 (C5-01) and
ASR proportional
gain 2 (C5-03)
• Torque and speed
response
• Controlling hunting
and vibration
10.00
10.00 to 50.00
• Increase the setting if
torque or speed response is
slow.
• Reduce the setting if
hunting or vibration
occurs.
ASR integral time 1
(high-speed) (C5-02)
and
ASR integral time 2
(low-speed) (C5-04)
• Torque and speed
response
• Controlling hunting
and vibration
0.500sec
0.300
to
1.000sec
• Reduce the setting if
torque or speed response is
slow.
• Increase the setting if
hunting or vibration
occurs.
ASR switching
frequency (C5-07)
Switching the ASR
proportional gain and
integral time
according to the
output frequency
0.0Hz
0.0 to max.
output
frequency
Set the output frequency at
which to change the ASR
proportional gain and
integral time when the same
values cannot be used for
both high-speed and
low-speed operation.
ASR primary delay
time (C5-06)
• Controlling hunting
and vibration
0.010sec
0.04 to 0.020
Increase the setting if
machine rigidity is low and
the system vibrates easily.
Carrier frequency
selection (C6-11)
• Reducing motor
magnetic noise
• Controlling hunting
and vibration at low
speeds (3Hz or less)
Depends
on the
capacity.
Default value
• Increase the setting if
motor magnetic noise is
high.
• Reduce the setting if
hunting or vibration occurs
at low to middle-range
speeds.
Table 4.4 Adjusted User Parameters (Continued)
Control
Method
Name
(Parameter Number)
Performance
Factory
Setting
Recommended
Setting
Adjustment Method