Brake sequence, Inspection operation timing chart, Brake sequence without torque compensation – Yaskawa L1000E AC Drive Technical Manual for CIMR-LE Models for Elevator Applications User Manual
Page 125: 6 setup procedure for elevator applications
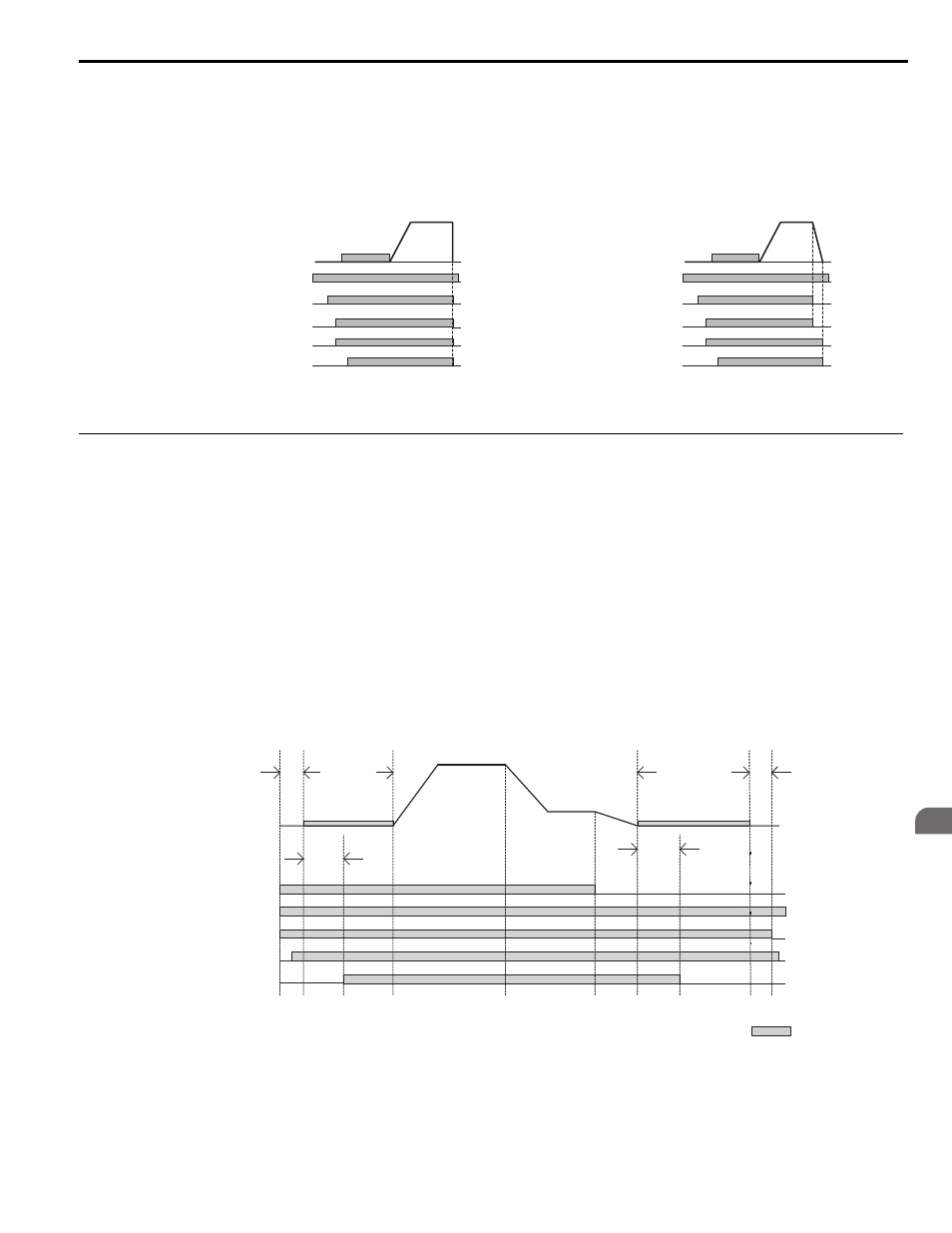
4.6 Setup Procedure for Elevator Applications
YASKAWA ELECTRIC SIEP YAIL1E 01A YASKAWA AC Drive L1000E Technical Manual
125
St
ar
t-
U
p
Pr
og
ra
m
m
in
g
&
Op
er
at
io
n
4
■
Inspection Operation Timing Chart
A timing chart for Inspection Operation appears in
Figure 4.18 Inspection Operation Sequence
◆ Brake Sequence
WARNING! Sudden Movement Hazard. Rapid deceleration may cause the drive to fault on an overvoltage condition, resulting in death
or serious injury due to an uncontrolled motor state. Be sure to set an acceptable deceleration time in parameter C1-09, Fast Stop
Ramp, when using the fast-stop feature.
NOTICE: Always turn off the RUN command before changing the setting of parameters d1-18 (Speed Reference Selection Mode), b1-
01 (Speed Reference Selection), or H1-
(Multi-Function Digital Inputs). If the RUN command is on when changing any of these
settings, the motor may unexpectedly start running, and could result in injury.
The drive supports two types of brake sequences, one with torque compensation at start using an analog input terminal
(H3- = 14) and the other without torque compensation at start.
■
Brake Sequence without Torque Compensation
To configure the brake sequence operation without torque compensation, do not set any analog input terminals for
“Torque compensation” (H3- = 14).
Figure 4.14
Figure 4.19 Brake Sequence without Torque Compensation at Start
is divided into time zones.
explains the sequence in each time zone.
<1> The drive stops if either the Up/Down command or Inspection Operation signals are removed.
Inspection Operation
Speed
DC Injection Braking/
Position Lock at start
DC Injection Braking/
Position Lock at start
Speed
Up/Down command
H1-
= 54 (Inspection Operation)
H2-
= 51 (Output Cont. Contr.)
H2-
= 50 (Brake Control)
Inspection Operation
Speed
Safe disable (terminals H1/H2 on)
and Baseblock off (H1-
= 8/9)
Speed
Up/Down command
H1-
= 54 (Inspection Operation)
H2-
= 51 (Output Cont. Contr.)
H2-
= 50 (Brake Control)
Safe disable (terminals H1/H2 on)
and Baseblock off (H1-
= 8/9)
Inspection Operation without Decel Ramp (C1-15=0)
Inspection Operation with Decel Ramp (C1-15>0)
<1>
<1>
C1-15
t1
t2
t3
t4
t5
t6
t7
t8
t9
S1-06
(Brake
Release
Delay
Time)
S1-07
(Brake
Close
Delay
Time)
DC Injection/
Position Lock at Stop
DC Injection Braking/
Position Lock at Start
Speed
S1-10
(Up/Down Command
Delay Time)
Up/Down Command
Output Contactor Control
(H2-
= 51)
Motor Contactor Response
(H1-
= 56)
Brake Control (H2-
= 50)
Selected Speed
d1-26
(Leveling Speed)
S1-04
(DC Injection/
PositionLock
Time at Start)
S1-05
(DC Injection
Braking/Position
Lock Time at stop)
S1-11
(Output Contactor
Open Delay Time)
Enabled
Safe disable (terminals H1/H2 on)
and Baseblock off (H1-
= 8/9)