E.3 user setting table – Yaskawa L1000E AC Drive Technical Manual for CIMR-LE Models for Elevator Applications User Manual
Page 470
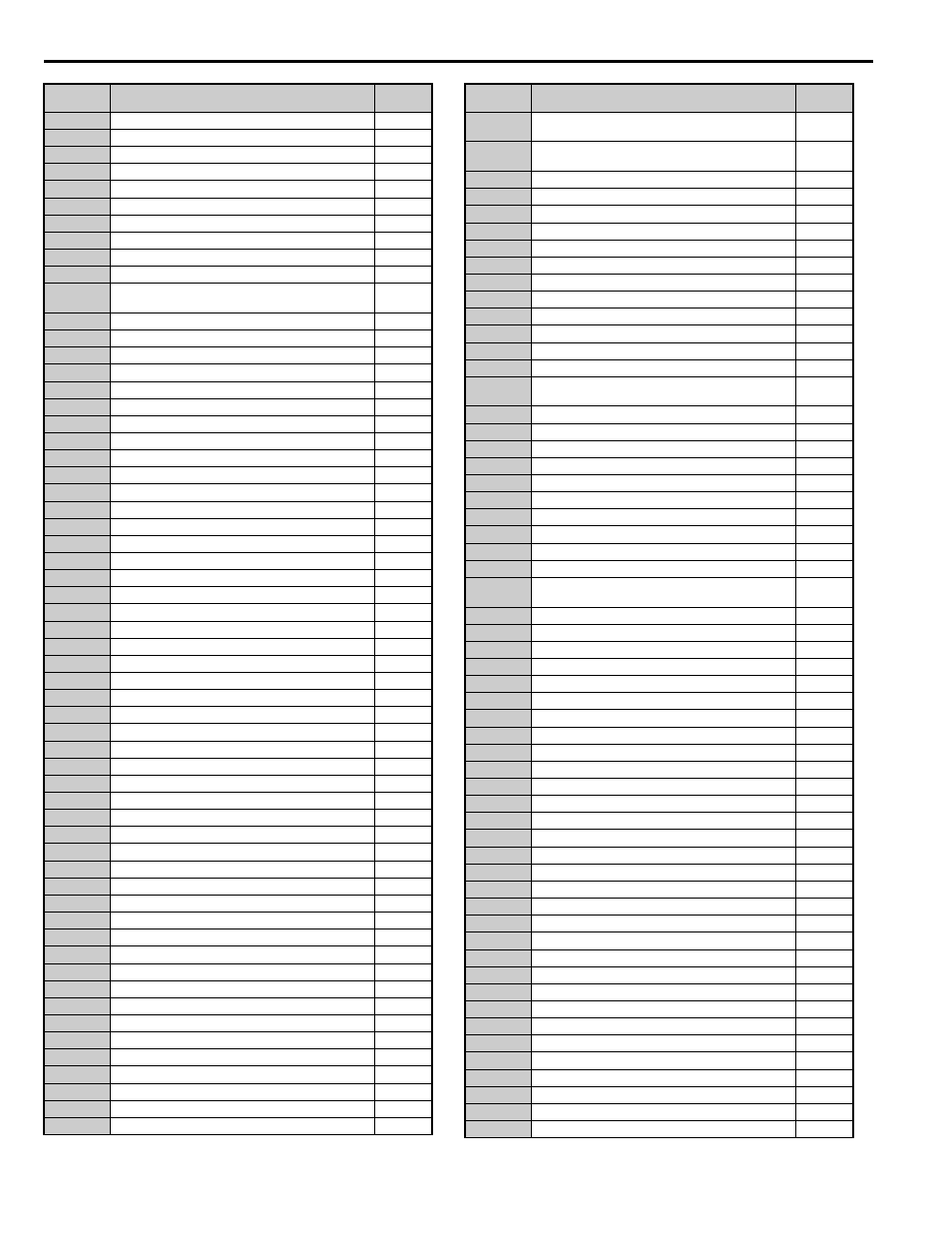
E.3 User Setting Table
470
YASKAWA ELECTRIC SIEP YAIL1E 01A YASKAWA AC Drive L1000E Technical Manual
o1-12
Length Units
o1-20
Traction Sheave Diameter
o1-21
Roping Ratio
o1-22
Mechanical Gear Ratio
o1-23
HBB Non Display Select
o2-01
LO/RE Key Function Selection
o2-02
STOP Key Function Selection
o2-03
User Parameter Default Value
o2-04
Drive Model Selection
o2-05
Speed Reference Setting Method Selection
o2-06
Operation Selection when Digital Operator is
Disconnected
o3-01
Copy Function Selection
o3-02
Copy Allowed Selection
o4-01
Cumulative Operation Time Setting
o4-02
Cumulative Operation Time Selection
o4-03
Cooling Fan Operation Time Setting
o4-05
Capacitor Maintenance Setting
o4-07
DC Bus Pre-charge Relay Maintenance Setting
o4-09
IGBT Maintenance Setting
o4-11
U2, U3 Initialization
o4-12
kWh Monitor Initialization
o4-13
Number of Travels Counter Reset
o4-15
Maintenance Alarm Snooze Period
o4-16
Maintenance Monitoring Selection
S1-01
Zero Speed Level at Stop
S1-02
DC Injection Current at Start
S1-03
DC Injection Current at Stop
S1-04
DC Injection / Position Lock Time at Start
S1-05
DC Injection / Position Lock Time at Stop
S1-06
Brake Release Delay Time
S1-07
Brake Close Delay Time
S1-10
Run Command Delay Time
S1-11
Output Contactor Open Delay Time
S1-12
Motor Contactor Control During Auto-Tuning Selection
S1-26
Emergency Stop Start Level
S2-01
Motor Rated Speed
S2-02
Slip Compensation Gain in Motoring Mode
S2-03
Slip Compensation Gain in Regenerative Mode
S2-05
Slip Compensation Torque Detection Delay Time
S2-06
Slip Compensation Torque Detection Filter Time Constant
S3-01
Position Lock Gain at Start 1
S3-02
Position Lock Gain at Start 2 (Anti-Rollback Gain)
S3-03
Position Lock Gain at Stop
S3-04
Position Lock Bandwidth
S3-10
Starting Torque Compensation Increase Time
S3-12
Starting Torque Compensation Bias in Down Direction
S3-14
Torque Compensation Fade Out Speed
S3-15
Torque Compensation Fade Out Time
S3-16
Torque Limit Reduction Time
S3-20
Dwell 2 Speed Reference
S3-21
Dwell 2 End Speed
S3-25
DC Injection Gain in Regenerative Operation
S3-26
DC Injection Gain in Motoring Operation
S3-27
Torque Compensation Value with Load Condition 1
S3-28
Torque Compensation Value with Load Condition 2
S3-29
Analog Input from Load Cell with Load Condition 1
S3-30
Analog Input from Load Cell with Load Condition 2
S3-34
Anti-Rollback Torque Bias 1
S3-35
Anti-Rollback Torque Bias 2
No.
Name
User
Setting
S3-37
Position Deviation Level to Apply Anti-Rollback Torque
Bias 1
S3-38
Position Deviation Level to Apply Anti-Rollback Torque
Bias 2
S3-39
Anti-Rollback Integral Gain
S3-40
Anti-Rollback Movement Detection
S3-41
Position Lock Gain at Start Reduction
S4-01
Light Load Direction Search Selection
S4-02
Light Load Direction Search Method
S4-03
Light Load Direction Search Time
S4-04
Light Load Direction Search Speed Reference
S4-05
Rescue Operation Torque Limit
S4-06
Rescue Operation Power Supply Selection
S4-07
UPS Power
S4-08
UPS Operation Speed Limit Selection
S4-12
DC Bus Voltage during Rescue Operation
S4-13
Rescue Operation Power Supply Deterioration Detection
Level
S4-15
Speed Reference Selection at Rescue Operation
S5-01
Short Floor Operation Selection
S5-02
Nominal Speed for Short Floor Calculation
S5-03
Short Floor Minimum Constant Speed Time
S5-04
Distance Calculation Acceleration Time Gain
S5-05
Distance Calculation Deceleration Time Gain
S5-10
Stopping Method Selection
S5-11
Deceleration Distance
S5-12
Stop Distance
S5-13
Direct Landing Minimum Speed Level
S6-01
Motor Contactor Response Error (SE1) Detection/Reset
Selection
S6-02
Starting Current Error (SE2) Detection Delay Time
S6-03
SE2 Detect Current Level
S6-04
Output Current Error (SE3) Detection Delay Time
S6-05
Brake Response Error (SE4) Detection Time
S6-10
Overacceleration Detection Level
S6-11
Overacceleration Detection Time
S6-12
Overacceleration Detection Selection
S6-15
Speed Reference Loss Detection
S6-16
Restart after Baseblock Selection
T1-00
Motor 1/Motor 2 Selection
T1-01
Auto-Tuning Mode Selection
T1-02
Motor Rated Power
T1-03
Motor Rated Voltage
T1-04
Motor Rated Current
T1-05
Motor Base Frequency
T1-06
Number of Motor Poles
T1-07
Motor Base Speed
T1-08
Encoder Resolution (pulses per revolution)
T1-09
Motor No-Load Current (Stationary Auto-Tuning 1 and 2)
T1-10
Motor Rated Slip (Stationary Auto-Tuning 2)
T2-01
Auto-Tuning Mode Selection
T2-04
Motor Rated Power
T2-05
Motor Rated Voltage
T2-06
Motor Rated Current
T2-08
Number of Motor Poles
T2-09
Motor Base Speed
T2-10
Single Phase Stator Resistance
T2-11
Motor d-Axis Inductance
T2-12
Motor q-Axis Inductance
T2-13
Induced Voltage Constant Unit Selection
T2-14
Motor Induced Voltage Constant
No.
Name
User
Setting