Momentary power loss ridethrough, Torque limit, I/o phase loss protection and overtorque detection – Yaskawa Matrix Converter User Manual
Page 313: External baseblock signal, Acceleration/deceleration time, Output side magnetic contactor
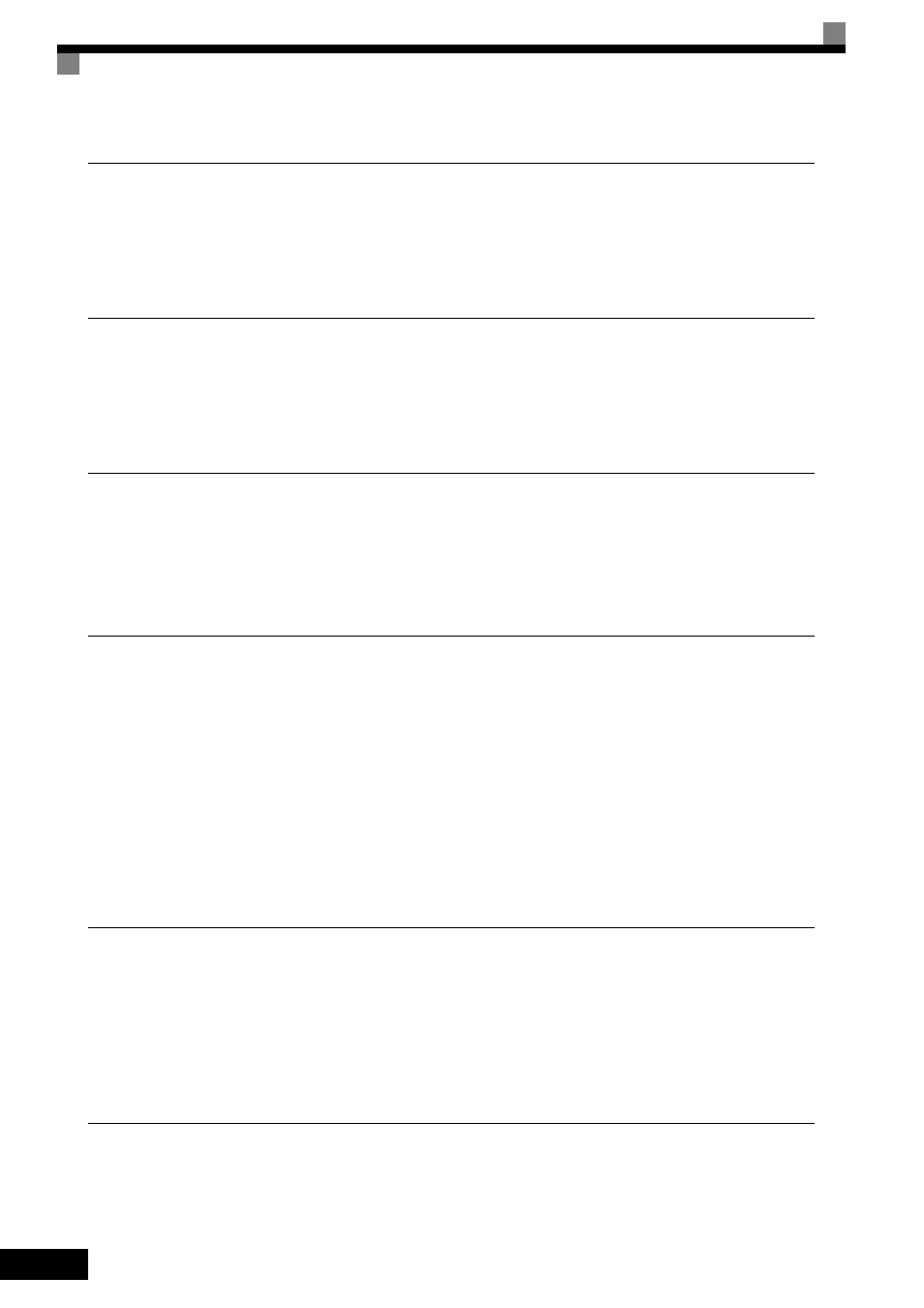
6
-148
Momentary Power Loss Ridethrough
Do not use the Momentary Power Loss Restart and Fault Restart functions in elevator-type applications. Make
sure that L2-01=0 and L5-01=0. If these functions are used, the motor coasts to a stop with the brake contact
open when a momentary power loss or fault occurs during run, possibly resulting in serious accidents.
Torque Limit
The torque limit values (L7-01 to L7-04) are the motor’s rated torque. When there is a possibility of insuffi-
cient torque at start up or other times, increase the MxC capacity and set the torque limit value between 200%
and 300% (default is 200%).
I/O Phase Loss Protection and Overtorque Detection
To prevent the load from falling when phase loss or a similar situation occurs, enable L8-07 (Output Phase
Loss Protection) and L6-01 to L6-06 (Torque Detection Selection). This setting is disabled as a default.
Falling detection or a similar safety measure should also be provided on the load side.
External Baseblock Signal
If the External Baseblock Command (settings 8 and 9 of H1-01 to H1-10) is input while the motor is running,
the motor will immediately coast to a stop. Do not input the External Baseblock Command while the motor is
running unless necessary.
Make sure that the holding brake operates when using the External Baseblock Command for a Fast Stop or
interlock to start the MxC.
If the External Baseblock Command is input and immediately reset, the MxC does not output voltage for the
time set to L2-03 (Momentary Power Loss Minimum Baseblock Time). The default for L2-03 is 0.5 to 2.0 sec-
onds, depending on the MxC capacity. Do not use the External Baseblock Command in an application where
the motor is frequently started and stopped.
Acceleration/Deceleration Time
If the delay time for the holding brake’s mechanical operation is not properly calculated and the accel/decel
time on the MxC side is too short, overcurrent or wear on the brakes may occur at start. This can also cause the
load to slip at stop because the holding brake won’t be triggered in time. If these situations arise, adjust the
timing for the holding brake by using the Dwell function at start or the Dwell function at stop. See page 6-152
for more information.
Output Side Magnetic Contactor
Do not install a magnetic contactor between the MxC and the motor. Other than an emergency situation, if a
magnetic contactor must be installed because of local electrical codes or regulations, or in order to operate cer-