Torque compensation (flux vector control only) – Yaskawa Matrix Converter User Manual
Page 317
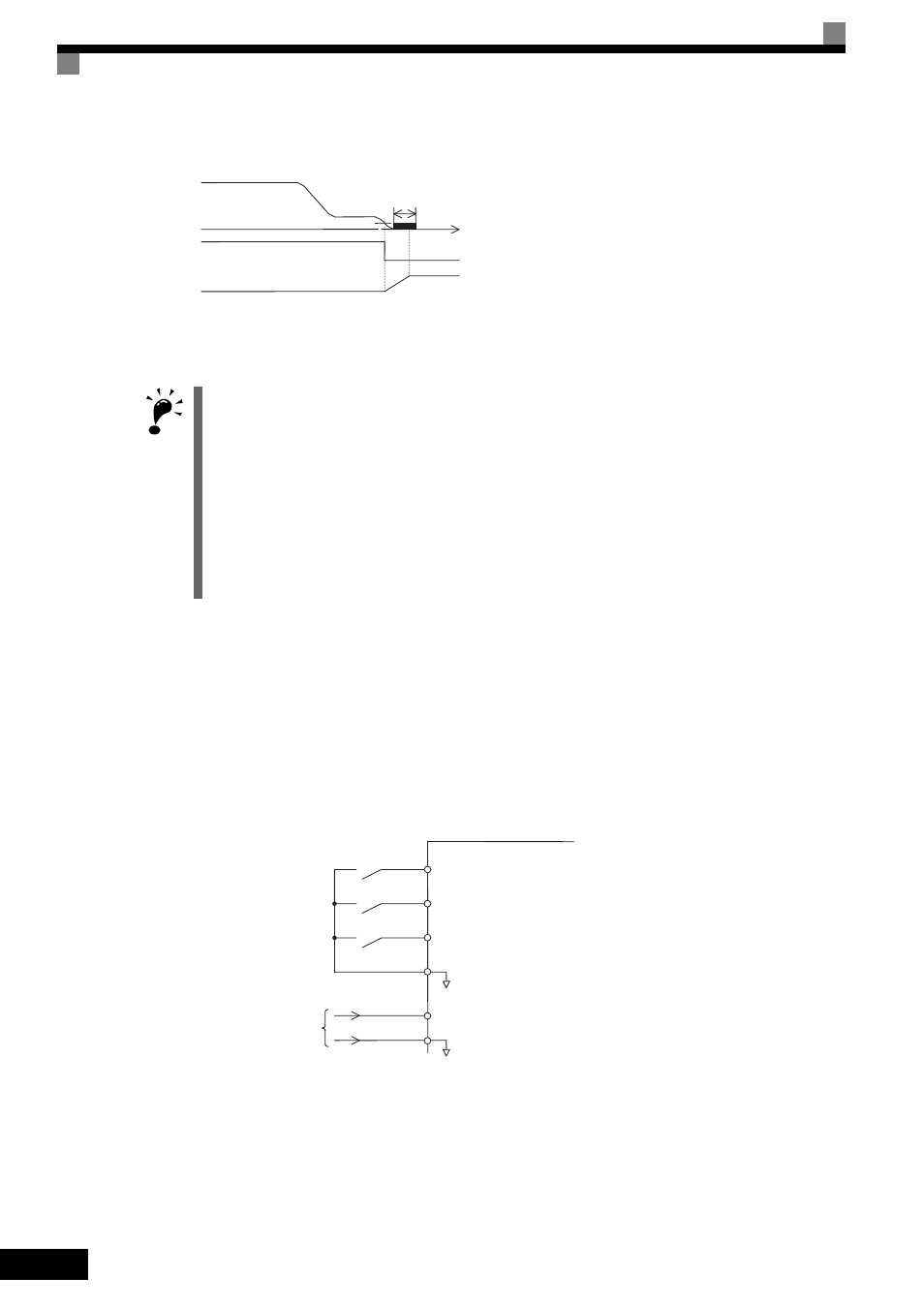
6
-152
Stopping with DC Injection Braking and Zero-Speed Control
When the holding brake’s mechanical operation is slow, use DC Injection Braking (zero-speed control for
Flux Vector Control) until the brakes are fully closed to prevent the brakes from slipping when stopping.
Torque Compensation (Flux Vector Control Only)
When Flux Vector Control is used, the torque compensation signals corresponding to the load can be
input from the multi-function analog input terminals in advance to reduce shock, such as that caused by open-
ing and closing holding brakes. The load size and motoring/regenerating status must be detected at the
machine side in advance. Check that polarity is correct. Incorrect polarity will increase the shock.
Sequence Circuit Configuration
The following diagram shows the sequence circuit configuration for torque compensation.
Fig 6.86 Torque Compensation Sequence Circuit Configuration
IMPORTANT
1. When the load cannot be maintained sufficiently using DC Injection Braking with Open Loop Vector Control
and V/f control, use the Dwell functions at stop.
• b6-03 (Dwell Frequency at Stop): Min. output frequency to 3.0 Hz.
The value must be less than the frequency when frequency detection 2 is off (L4-01
− L4-02).
• b6-04 (Dwell Time at Stop): 0.3 to 0.5 s
[b2-04 (DC Injection Braking Time at Stop): 0.0 s]
2. If the MxC and motor must be isolated while stopping using a magnetic contactor, for example in an eleva-
tor, fully close the holding brakes and isolate the MxC during baseblock (during baseblock signal: on) as
stipulated by law in the EU.
During motor control or DC Injection Braking (zero-speed control), an MxC error may occur due to surge
voltage. When a magnetic contactor is used between the MxC and motor, set L8-07 (Output Phase Loss
Protection) to 1 (enabled).
b2-04 (DC Injection Braking Time at Stop)
0.3 to 0.5 s
(HIGH)
t
Output frequency
Holding brake operation
on off
CLOSE
OPEN
(LOW)
b2-01 (DC Injection Braking Start Frequency)]:
0.1 to 3.0 Hz
b2-02 (DC Injection Braking Current): 50% to
80%
ޓ(open loop vector control, V/f control only)
Frequency
detection 2 or
During run 2
S1
UP
S2 (Reverse
run)
DOWN
HIGH/LOW
S6 (Multi-step speed reference 2)
SC
(Using elevator control circuit)
Torque compensation signal
−10 to +10 V
A3
AC
(Forward run)
H3-04 (Terminal A3 Signal Level Selection) = 1
(
−10 to +10 V)
H3-05 (Terminal A3 Function Selection) = 14 (torque
compensation)
Use H3-06 and H3-07 for fine tuning.