Control related adjustments – Yaskawa Matrix Converter User Manual
Page 314
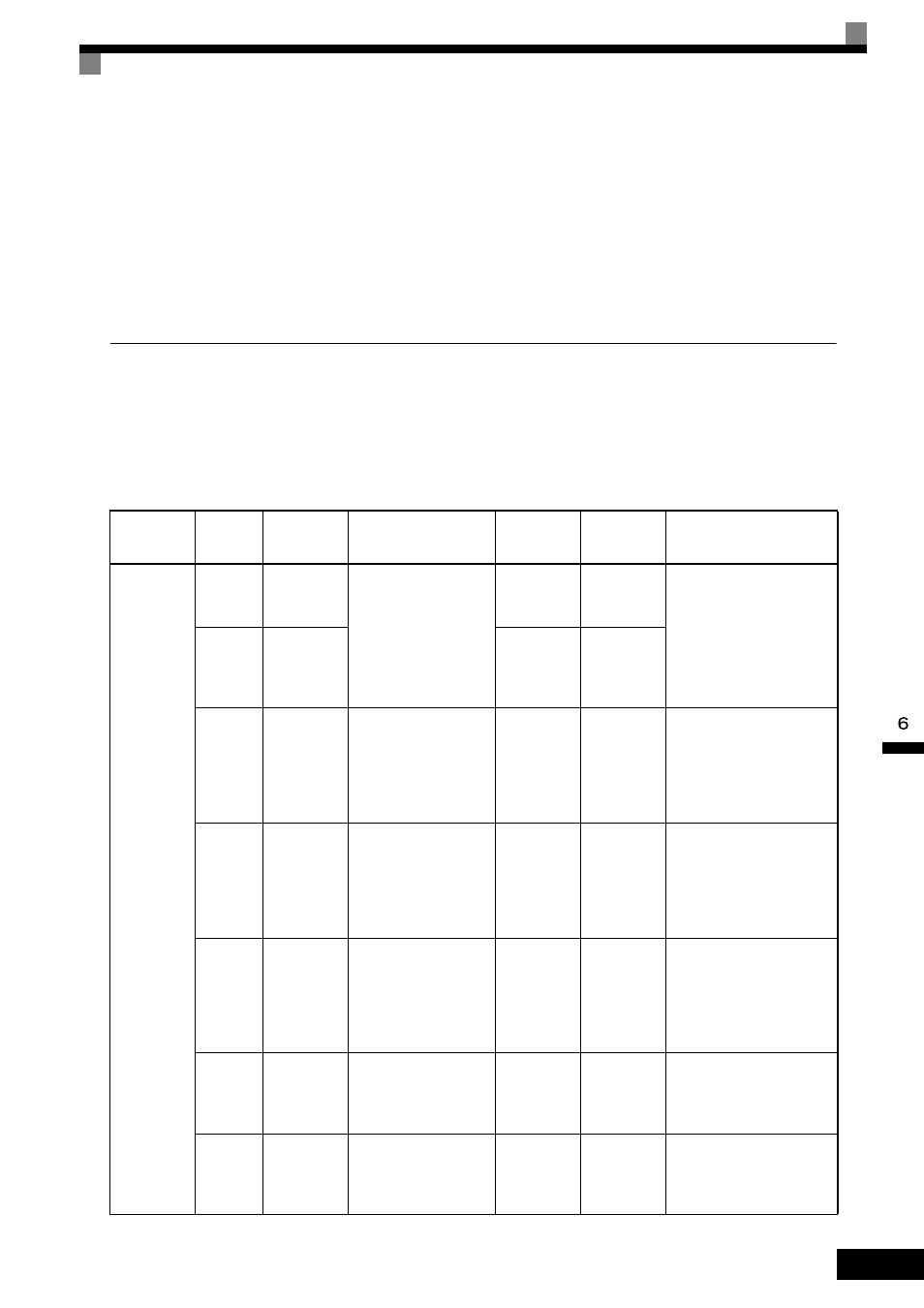
Elevator and Hoist Type Applications
6-
149
tain motors with an MxC, open or close the magnetic contactor only when the holding brake is fully closed
and the MxC is in baseblock status with the baseblock signal on.
If the magnetic contactor is opened or closed while the MxC is controlling the motor or during DC Injection
Braking (Zero-speed control), surge voltage or current from the motor by a full-voltage start may cause an
MxC fault.
When a magnetic contactor is installed between the MxC and the motor, set L8-07 (Output Phase Loss Protec-
tion) to 1 or 2 (Enabled).
Control Related Adjustments
The MxC is designed to provide sufficient performance for elevator and hoist type applications. However, if
problems related to controllability should occur such as oscillation or slipping, adjust the following parameters
in accordance with the control method. Only parameters that frequently require adjustment are listed in this
table.
Table 6.4 Control-Related Adjustments
Control
Method
Parame-
ter Num-
ber
Name
Performance
Factory
Setting
Recom-
mended
Setting
Adjustment Method
Open Loop
Vector Con-
trol (A1-02 =
2)
E1-08
Mid Output
Frequency
Voltage (VC)
• Improves torque and
speed response at low
speeds
• Controls shock at start
up
13.0 VAC
*
12.0 to 15.0
VAC
*
• Torque or speed response
is insufficient: Increase
the setting
• Shock at startup is large:
Reduce the setting
E1-10
Min. Output
Frequency
Voltage
(VMIN)
2.5 VAC
*
2.0 to 3.0
VAC
*
n2-01
Speed Feed-
back Detec-
tion Control
(AFR) Gain
• Increases torque and
speed response
• Controls hunting and
oscillation in mid-
range speeds (10 to 40
Hz)
1.00
0.50 to 2.00
• Torque or speed response
is insufficient: Reduce the
setting
• Hunting or oscillation
occurs: Increase the set-
ting
n2-03
Speed Feed-
back Detec-
tion Control
(AFR) Time
Constant 2
Increases torque and
speed response
750 ms
100 to 750
ms
• Speed response is slow
during sudden load
change: Reduce the setting
• Hunting or oscillation
occurs: Increase the set-
ting
C4-02
Torque Com-
pensation
Primary
Delay Time
Constant
• Increases torque and
speed response
• Controls hunting and
oscillation
100 ms
20 to 200 ms
• Torque or speed response
is insufficient: Reduce the
setting
• Hunting or oscillation
occurs: Increase the set-
ting
C3-02
Slip Com-
pensation
Primary
Delay Time
• Increases speed
response
• Improves speed sta-
bility
200 ms
100 to
500 ms
• Speed response is slow:
Reduce the setting
• Speed is not stable:
Increase the setting
C3-01
Slip Com-
pensation
Gain
Improves speed accu-
racy
1.0
0.5 to 1.5
• Speed is slow: Increase
the setting
• Speed is too fast: Reduce
the setting