5 setting speed bias – Yaskawa DR2 Sigma Servo User Manual
Page 134
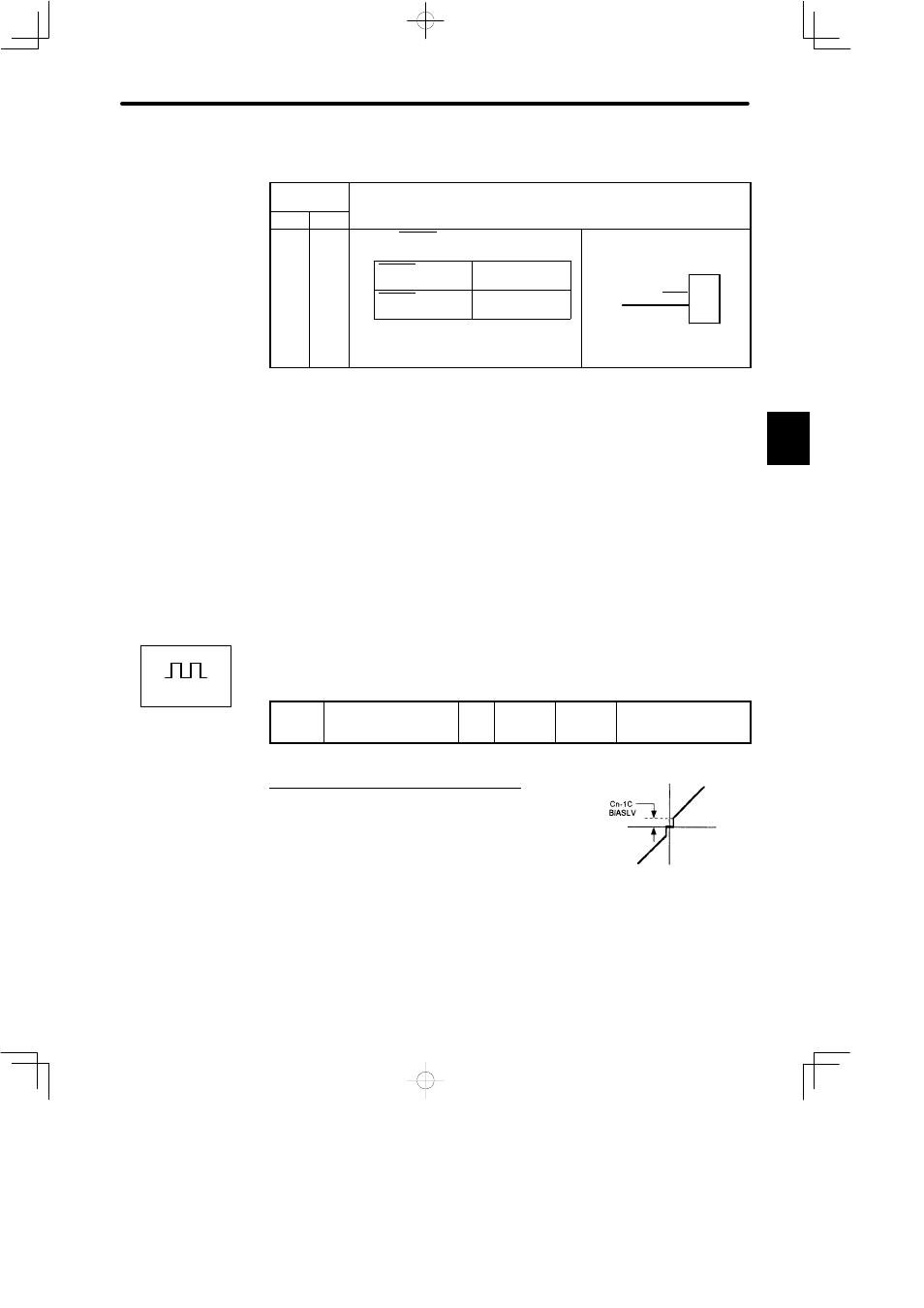
3.6 Minimizing Positioning Time
121
For speed/torque control only.
Cn-01
Setting
Control Mode
Bit B Bit A
Control Mode
D
Signal P-CON (1CN-41) is used to switch
between P control and PI control.
P-CON (1CN-41)
is open (OFF)
PI control
DR2 Servopack
P/PI
0
0
P-CON (1CN-41)
is closed (ON)
P control
P/PI
changeover
P-CON
(1CN-41)
(1CN 41)
D
Torque reference input T-REF (1CN-9)
cannot be used.
2) Proportional control can be used in the following two ways.
a) The host controller can selectively use P control mode for particular conditions only.
This method can prevent the occurrence of overshoot and also shorten settling time.
For particular conditions, refer to 3.6.6 Using Mode Switch.
b) In the speed control mode, if PI control mode is used when the speed reference has a
reference offset, the motor may rotate at a very slow speed and fail to stop even if 0 is
specified as a speed reference. In this case, use P control mode to stop the motor.
3.6.5 Setting Speed Bias
The settling time for positioning can be reduced by assigning bias to the speed reference out-
put part in the Servopack. To assign bias, use the following constant.
Cn-1C
BIASLV
Bias
Unit:
r/min
Setting
Range: 0
to 450
Factory
Setting: 0
For Position Control
Only
This user constant is for position control only.
This user constant is set to assign an offset to a
speed reference in the DR2 Servopack.
Use this constant to shorten settling time.
Set this user constant according to machine conditions.
3
Positions
Internal speed
reference
Error pulse