B.3.2 manual adjustment – Yaskawa DR2 Sigma Servo User Manual
Page 448
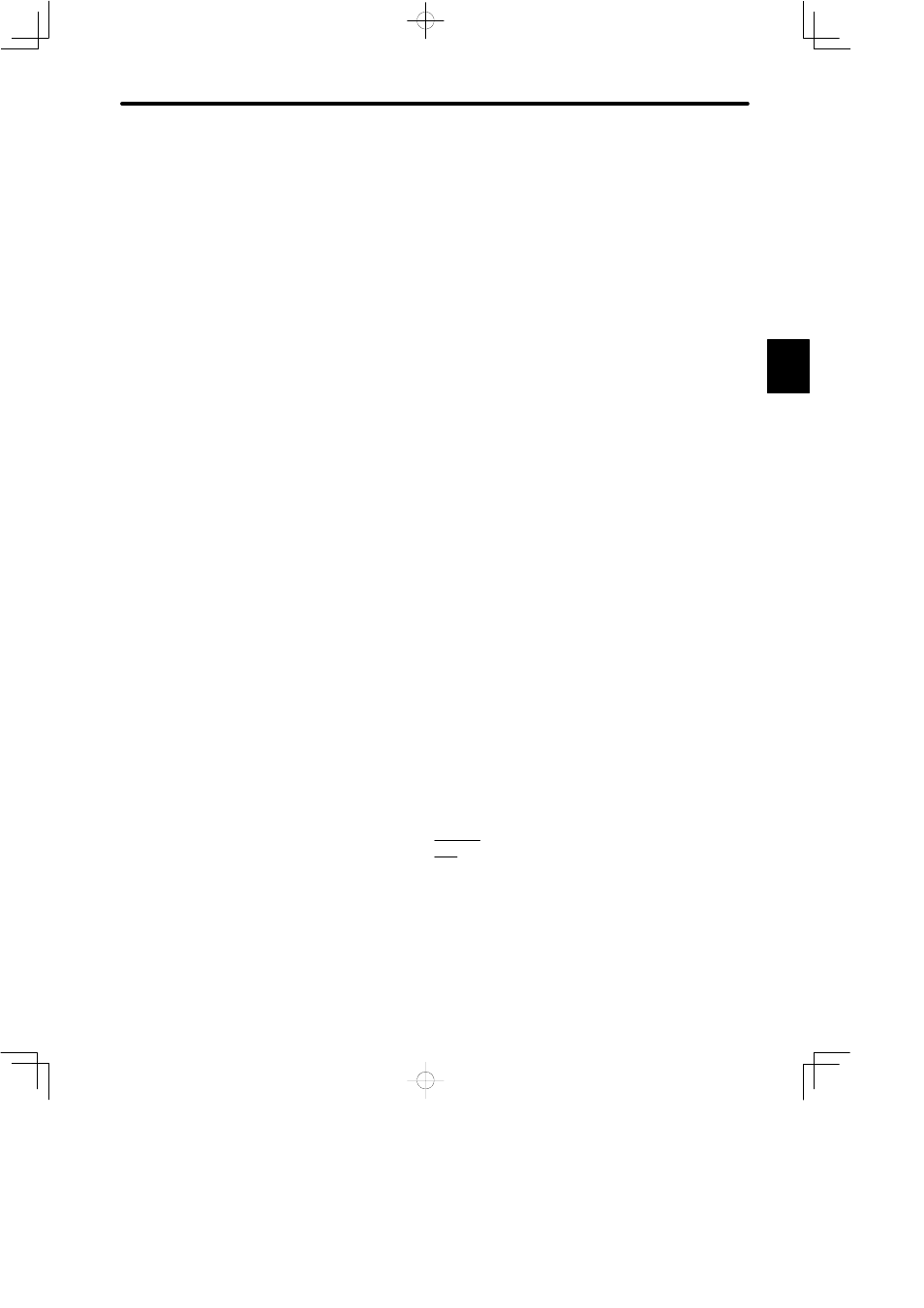
B.3 Adjusting a Servopack for Position Control
437
Auto-tuning may not end if high response is selected for a low-rigidity machine or low
response is selected for a high-rigidity machine.
If this occurs, halt the auto-tuning and change the machine rigidity selection.
2) If Auto-tuning is Unsuccessful
Auto-tuning may be unsuccessful (the end of auto-tuning not displayed) for machines
with large play or extremely low rigidity.
Similarly, auto-tuning may be unsuccessful for a machine with high load inertia (exceed-
ing 15 to 30 times the motor moment of inertia).
In these cases, use conventional manual adjustment.
Even if auto-tuning is successful for a machine with large fluctuations in load inertia or
load torque, vibrations or noise may still occur in some positions.
3) Response During Operation is Unsatisfactory after Auto-tuning
Auto-tuning sets the gain and integration time constant with some safety margin (to avoid
oscillations). This can result in positioning times.
In particular, the target position may not be reached if low response is selected, because
the machine does not move in response to the final minute references. An excessively
high setting of the integration time constant (Cn-05) during auto-tuning is one cause of
this problem.
If response is slow after auto-tuning, the speed loop gain cannot be manually increased
very much before vibration starts.
In this case, manually reduce the integration time constant while observing the machine
behavior to ensure oscillation does not occur.
Auto-tuning does not set the torque reference filter (Cn-17).
B.3.2 Manual Adjustment
1) The role of each user constant is briefly described below.
a) Speed Loop Gain (Cn-04)
This user constant sets the speed loop response.
The response is improved by setting this user constant to the maximum value in the
range which does not cause vibrations in the mechanical system.
The following formula relates the speed loop gain to the load inertia.
Speed Loop Gain Kv [Hz] =
GD
L
2:
Motor Axis Converted Load Inertia
GD
M
2
: Motor Moment of Inertia
2
GDL2
GDM2
+ 1
× (Cn-04 Preset value)
b) Speed Loop Integration Time Constant (Cn-05)
The speed loop has an integration element to allow response to micro-inputs.
B