Load monitoring parameters, 7 load monit o ri ng – HEIDENHAIN CNC Pilot 4290 V7.1 User Manual
Page 105
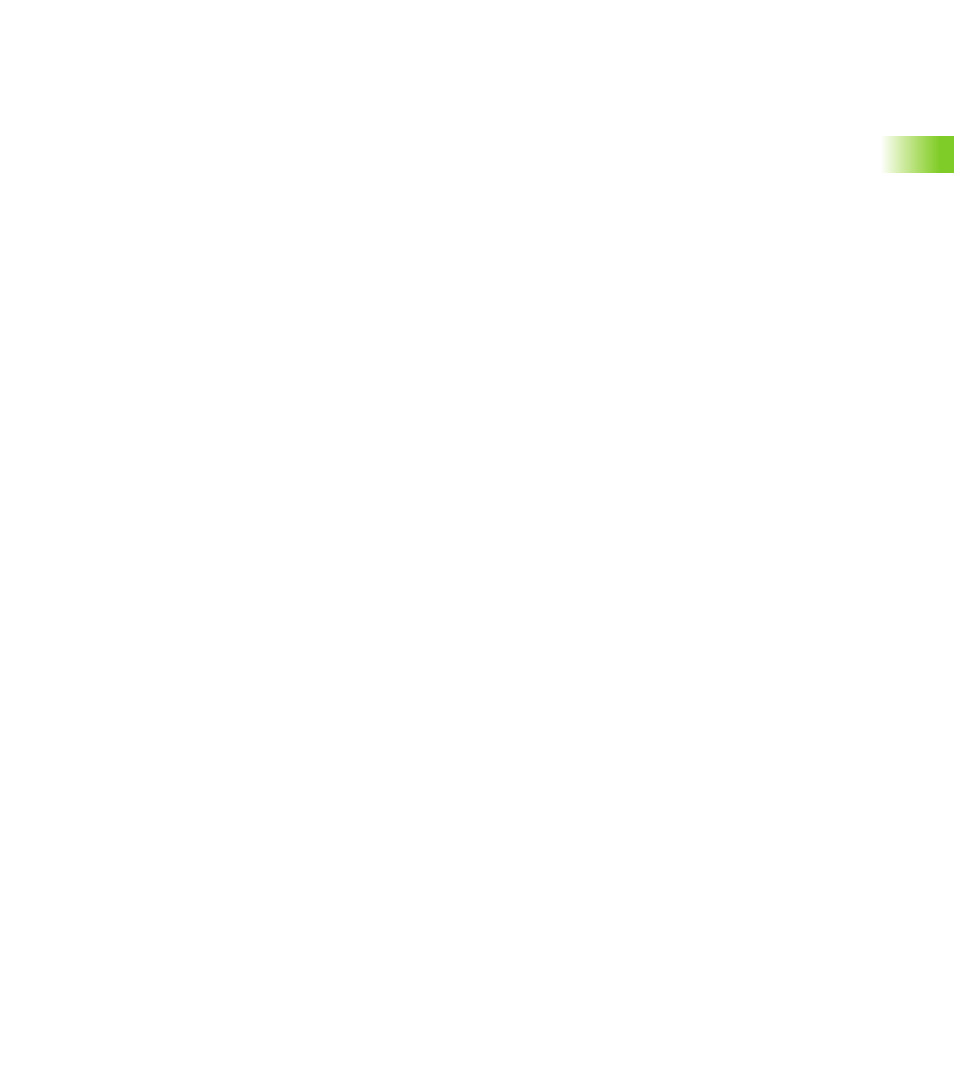
HEIDENHAIN CNC PILOT 4290
105
3.7 Load Monit
o
ri
ng
“Analyzer (file display)” submenu:
Set cursor: Position the cursor with the left/right arrow keys or to
the
Beginning of file
Next beginning zone
Maximum in zone
Display menu item: Select the component from the “Display file”
dialog box.
Setting - Zoom: Set the zoom factor. (Small values increase the
accuracy of the display and reduce the step size of the cursor.)
The settings defined for the grid, the time reference grid of the
measured value registration and the cursor position are shown in
the line below the graphic display relative to the start of reference
machining. Time 0:00.00 sec = Start of reference machining cycle.
Load monitoring parameters
Machine parameters for load monitoring (spindle: MP 809, 859, ...;
C axis: MP 1010, 1060; linear axes: MP 1110, 1160, ...):
Start-up time for monitoring [0..1000 ms] is evaluated if “Omit
paths of rapid traverse” is active:
Spindles: A limit value is calculated from the acceleration and
brake ramps. As long as nominal acceleration exceeds the limit
value, the monitoring function is deactivated. As soon as nominal
acceleration falls below the limit value, the monitoring function is
delayed by the start-up time for monitoring.
Linear and C axes: After rapid traverse has changed to feed rate,
the monitoring function is delayed by the “start-up time for
monitoring.”
Number of sample values to be averaged [1..50]
The mean value reduces the sensitivity to short-term peak load
during monitoring.
Maximum torque of drive [Nmm]
Delay in reaction P1, P2 [0..1000 ms]: The CNC PILOT indicates
that torque limit 1/2 has been exceeded after the time “P1/P2” has
passed.