Contour recessing, recess turning, Drilling, Cutting data, coolant – HEIDENHAIN CNC Pilot 4290 V7.1 User Manual
Page 553: 1 8 mac h ining inf o rm ation
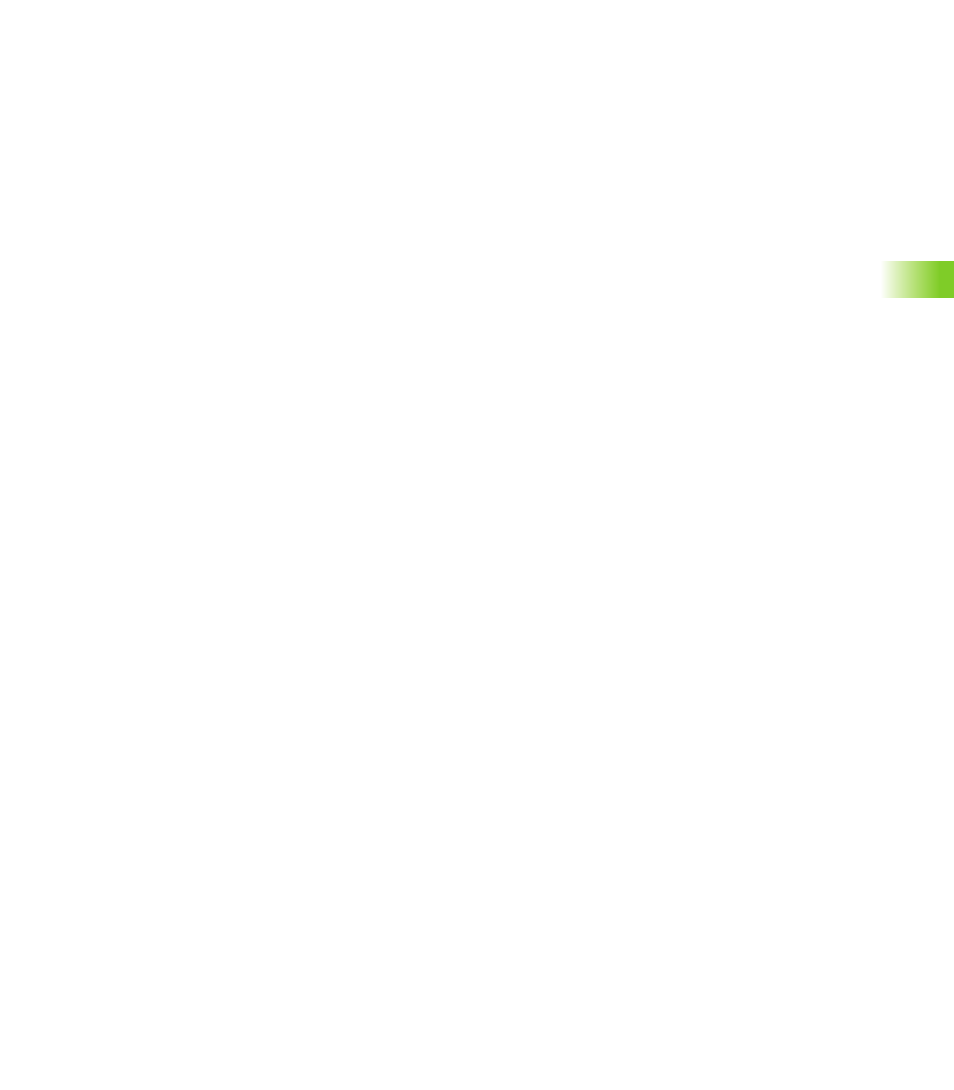
HEIDENHAIN CNC PILOT 4290
553
6.1
8
Mac
h
ining Inf
o
rm
ation
Contour recessing, recess turning
The cutting radius must be smaller than the smallest inside radius of
the recess contour, but >= 0.2 mm. TURN PLUS determines the
width of the recessing tool from the recess contour:
Recess contour includes paraxial base elements with radii on both
sides: SB <= b + 2*r (if radii differ: smallest radius).
Recess contour includes paraxial base elements without radii or
with a radius on one side: SB <= b
Recess contour does not include paraxial base elements: The width
of the recessing tool is determined from the recessing width divisor
(machining parameter 6 – SBD).
Abbreviations:
SB: Width of recessing tool
b: Width of base element
r: Radius
Drilling
Depending on the geometry of the bore hole, the AWG determines
the appropriate tool. For centric bore holes, TURN PLUS uses
stationary tools.
Cutting data, coolant
To determine the cutting parameters, TURN PLUS uses the
Workpiece material (program head)
Cutting material (tool parameters)
Machining mode (main machining operation selected in the IWG;
main machining operation from the machining sequence in the
AWG).
The values determined are multiplied by the tool-dependent
compensation factors (see “Technology Database” on page 641 and
see “Explanation of tool data” on page 622).
Note for roughing and finishing operations:
Main feed rate for use of the primary cutting edge
Auxiliary feed rate for use of the secondary cutting edge
Note for milling operations:
Main feed rate for machining in the milling plane
Auxiliary feed rate for infeed movements
For threading, drilling and milling operations, the cutting speed is
converted into rotational speed.