20 cont our -based t u rn ing cy cles – HEIDENHAIN CNC Pilot 4290 V7.1 User Manual
Page 226
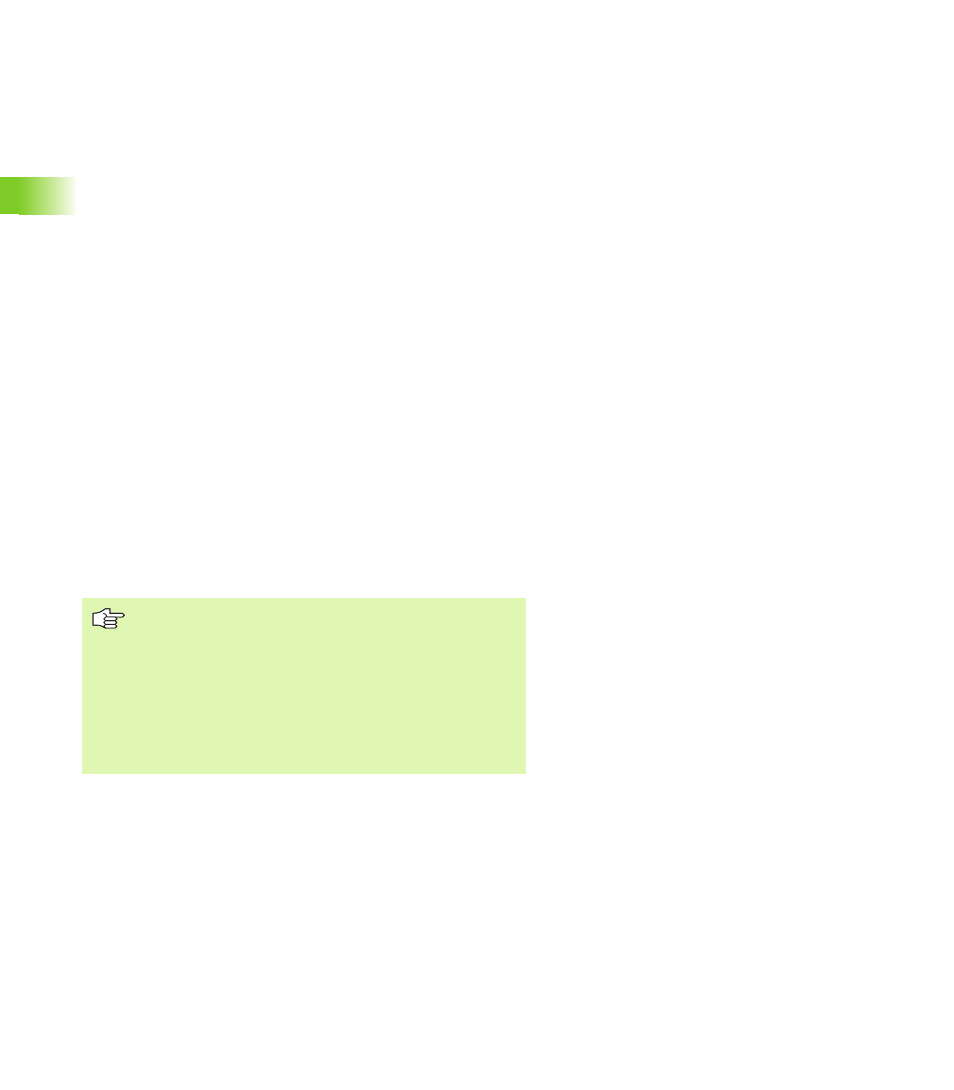
226
4.20 Cont
our
-Based T
u
rn
ing Cy
cles
The CNC PILOT uses the tool definition to distinguish between radial
and axial recesses.
Program at least NS or NS, NE and P.
Turning depth compensation R: Depending on factors such as
workpiece material or feed rate, the tool tip is displaced during a
turning operation. You can correct the resulting infeed error with
turning depth compensation factor. The value is usually determined
empirically.
Offset width B: After the second infeed movement, during the
transition from turning to recessing, the path to be machined is
reduced by the offset width B. Each time the system switches on this
side, the path is reduced by B—in addition to the previous offset. The
total offset is limited to 80% of the effective cutting width (effective
cutting width = cutting width –2*cutting radius). If required, the CNC
PILOT reduces the programmed offset width. After clearance
roughing, the remaining material is removed with a single cut.
V
Identifier beginning/end (default: 0)
A chamfer/rounding arc is machined:
V=0: At start and end
V=1: At start
V=2: At end
V=3: No machining
O
Recessing feed rate (default: active feed rate)
E
Finishing feed rate (default: active feed rate)
B
Offset width (default: 0)
G869 requires tools of the type 26*.
The tool radius compensation: is active.
A G57 oversize enlarges the contour (also inside
contours).
A G58 oversize
>0: Enlarges the contour
<0: Is not offset
G57/G58 oversizes are deleted after cycle end.
Parameters